Volume 11 - Year 2024 - Pages 425-434
DOI: 10.11159/jffhmt.2024.042
Thermal Analysis and Optimization of a Disc Brake Rotor for a Formula SAE Race Car
Murat Otkur
College of Engineering and Technology
American University of the Middle East, Kuwait
Murat.Otkur@aum.edu.kw
Abstract - Society of Automotive Engineers (SAE) is organizing Formula SAE (FSAE) competitions considering university students since 1981 targeting development of students via designing, manufacturing and racing with one-seated open wheeled race cars. The brake system plays a crucial role as a major component in designing a one-seated race vehicle for FSAE student competition. To avoid failures from brake fade and thermal stress, car brakes must not only be robust enough to withstand extreme mechanical loads but also dissipate the heat generated during braking in order to prevent the temperature breach the Maximum Design Temperature (MDT) limit. Additionally, the weight of the brake disc rotors plays a crucial role in the overall weight and of course performance of the vehicle. The methodological analysis, in order to determine a disc brake rotor's temperature profile under sporadic loads during consecutive braking and acceleration/cruise events considering a race, is presented in this work. OptimumLap software is used to determine a time-dependent vehicle speed and braking intensity profile for the 2019 Formula SAE competition Michigan endurance track and default Formula SAE vehicle configuration in OptimumLap software. The temperature distribution of the bicycle brake disc rotor (TEKTRO brand 6-bolt TR-8) during a sequence of successive braking and acceleration/cruise events across 2 laps is simulated using "SolidWorks" thermal analysis. Thermal simulations are continued until the temperature difference between consecutive laps is less than 10 K. A total of 106 thermal simulations were performed where the maximum temperature of the disc rotor is simulated as 1713 K which is above the MDT and the consecutive simulation are replaced with a single simulation maintaining the maximum simulation temperature via modifying thermal simulation input parameters. A DOE based optimization is carried using the single simulation method and the maximum temperature is reduced below the MDT limit. This study examines a practical approach for Formula SAE racing car disc brake temperature profile analysis and optimization.
Keywords: Thermal analysis, Formula student, SolidWorks, Minitab, DOE, OptimumLap, Disc Rotor.
© Copyright 2024 Authors - This is an Open Access article published under the Creative Commons Attribution License terms. Unrestricted use, distribution, and reproduction in any medium are permitted, provided the original work is properly cited.
Date Received: 2024-09-30
Date Revised: 2024-10-28
Date Accepted: 2024-11-30
Date Published: 2024-12-16
1. Introduction
Formula SAE is a well-known engineering competition that began in 1981 at the University of Texas in Austin and has since spread around the world [1]. College students are tasked with designing, building, and competing in formula-style one-seated open wheel race cars. Teams need to develop high-performance vehicles under stringent budgetary, safety, and design limitations. These vehicles must then be evaluated in fast-paced dynamic events like autocross and endurance races to evaluate their durability, speed, and agility [2]. Simultaneously, static exercises like design presentations assess technical ideas and economic viability. These activities provide students excellent chances to refine their problem-solving, collaborative, and project management abilities while advancing automotive technology and developing a community of driven engineers committed to innovation in motorsports. Formula SAE cars are designed with a braking system that provides superior stopping force and control. To lower weight and enhance handling, it usually has lightweight brake parts like aluminium callipers and high strength metal brake disc rotor components.
Numerous research studies have examined various aspects in thermal analysis of disc brake design in Formula SAE vehicles including material choices, heat dissipation techniques, and thermal control tactics to improve the effectiveness and dependability of these braking systems. Chengal Reddy (2013) used “Pro-E” and “Ansys” to model and analyse solid and vented disc brakes [3]. “Pro-E” is used to produce finite element (FE) models of the brake disc, and “Ansys”, which is based on the finite element method (FEM), is used to analyse the FSAE car disc brake. The optimum material for a disc brake is determined as maraging steel, according to the study results. It is concluded that ventilated type disc brake is the best possible profile for the present application. Eshaan Gupta (2022) made a study that optimizes the FSAE race car's braking system for weight reduction and performance enhancement compared to OEMs [4]. Employing “Matlab” for calculations and innovative design tools like “Altair Inspire”, the researcher iteratively designed and simulated components with “SolidWorks” and “Ansys” for safety and effectiveness. This study has found the following results: Shear force of 4500 N, max stress of 3.10x108 Pa, heat flux of 18000 W/m2 and maximum temperature of 194.04 °C. Manthan Vidiya and Balbir Singh (2017) conducted thermal analysis of brakes, including energy conversion methods, convection coefficients, and temperature rise [5]. They validated findings through simulations and real-world car testing. This paper goes beyond previous studies by analysing temperatures across laps, crucial for optimizing brakes in formula student cars. Using “Ansys” Transient Thermal profile, they plotted temperatures on the disc, with a maximum of 61.3°C. A temperature-time graph showed increase with each braking, aiding comparison with real-world testing. Actual car testing revealed a maximum disc temperature of 62.3°C, showing a similar trend. Comparing simulation and experimental results, they found nearly identical temperature variations, with a maximum difference of around 5°C. Pragya Mahajan (2021) conducted a research with the goal of creating an effective braking system with an emphasis on thermal stability, weight reduction, and compactness [6]. For optimum performance and safety compliance, he entails calculating braking torque, choosing components, CAD modelling, simulations, and real-world testing. The study's conclusions show that even under severe braking situations, the planned brake components, especially the disc, remain thermally and structurally robust. For manufacturing, laser cutting is used. Determining the boundary conditions for the thermal analysis depends heavily on the airflow surrounding the disc. In a later study, using “CFX”, Belhocine and Omar conducted a computational fluid dynamics (CFD) investigation to ascertain the airflow around the disc rotor and the heat transfer coefficients (HTCs) in each surface [7]. The authors were able to model the temperature distribution for the grey cast iron material disc using the HTCs. Karnik created a coupled model with Matlab and Ansys to calculate torque to be used in thermal analysis [8]. The researchers examined three distinct discs: Rotors without slots, with slots, and with slots and dimples. The use of dimples increases the rate of convective cooling. Deepak Hugar and Kadabadi (2017) investigated various slot designs with the goal of enhancing thermal conductivity and reducing weight through thermal analysis on an actual disc brake rotor model [9]. The author's objective is to increase disc brake efficiency in order to lower daily accident rates. The researchers used “Catia” for modelling and “Ansys” for static and transient thermal analysis. When compared to the regular Bajaj Pulsar 2-wheeler disc brake and other new designs, the study reveals that a modified disc brake design, known as "new disc 5," improves brake performance. Its safety is confirmed by structural study, and its temperature distribution is improved. In a similar study, Kumar, Thriveni, Reddy, and Gawd (2014) discussed how to optimize automotive brake discs and examine the steady-state thermal behaviour of the contact between the disc and pads during braking [10]. The authors performed this by using “Ansys”, “SolidWorks”, and “HyperMesh” for design, analysis, and optimization, paying close attention to thermal-structural details. The findings indicated that while the curved vented disc has a larger heat flux than the straight vented disc, substituting straight vents with curved vents in the brake disc lowers von Mises stresses, displacement vector sum, and disc weight.
Verification of the thermal simulation is needed in order to prove the developed models. Within this perspective Vecchiato et al. designed a specialized test bench in order to simulate real braking conditions with the ability of measuring critical parameters such as braking torque and disc temperature [11-12]. Similarly. Carvalho and Melo developed a test bench setup in order to evaluate coefficient of friction variation versus disc brake rotor temperature [13].
The aim of this study is to design a disc brake rotor component that will be employed in a formula SAE student single-seater open-wheel race car, allowing it to meet the SAE constraints and driver requirements. The disc brake is designed to be strong so that it withstands the braking forces while having adequate heat dissipation which reduces maximum operating temperatures. The disc brake should be light weight so that it satisfies the brake weight requirement.
2. Methodology
There are several phases in the project's methodology that must be followed in order. First, a market benchmarking study of disc brakes already available at the market was carried out to gather information on common designs. The disc brake's geometric configuration was then the focus of attention, which was performed by using “SolidWorks” to create a 3D model. Afterwards, available track and vehicle files (Michigan 2019 endurance track and FSAE aero vehicle) are employed in OptimumLap in order to determine the FSAE race endurance event brake profile. Later on, the thermal simulations were performed for consecutive braking/accelerating events using “SolidWorks” to obtain the brake rotor’s maximum temperature profile. The flowchart of the method is represented in Figure 1.
2.1. Braking Profile Determination
Standard FSAE Aero vehicle and endurance track used in FSAE Michigan 2019 competition is used for braking profile determination. All specifications of the track and vehicle used in the study are listed in Tables 1 and 2.
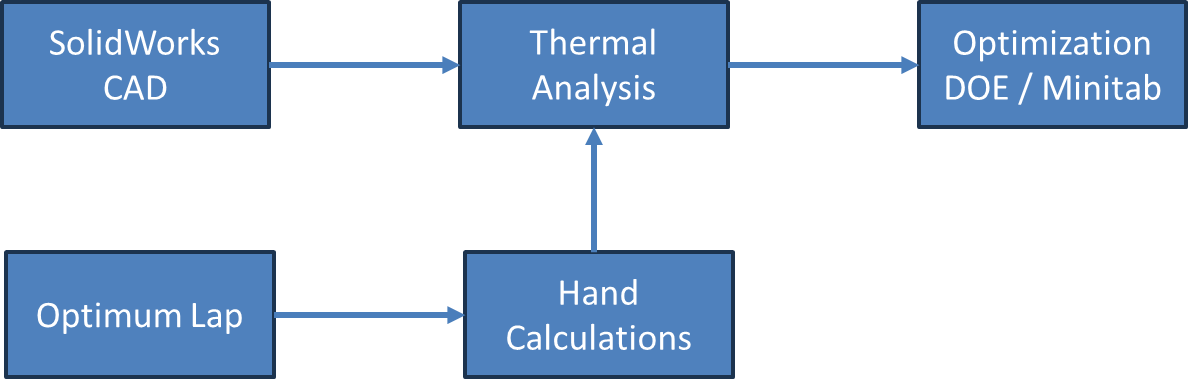
Table 1. Specifications of the “FSAE Aero” vehicle used in “OptimumLap”.
Parameter |
Value |
Total Mass |
230 kg |
Max Torque |
75.5 N.m at 7862 rpm |
Type of Fuel |
Gasoline |
Type of Transmission |
Sequential Gearbox |
Max Power |
93.8 hp at 9264 rpm |
Power Mass Ratio |
0.41 hp/kg |
Downforce @ 100 km/h |
624.36 N |
Drag @ 100 km/h |
502.66 N |
2. Thermal Simulation
The brake rotor used for the study is shown in Figure 2. The disc brake rotor is TEKTRO brand 6-bolt brake rotor TR-8 with outer diameter of 161 mm and thickness of 2 mm. For the thermal analysis, the inner part of brake rotor is excluded from the thermal analysis as shown in Figure 3 since the heat power generated by the callipers is only applied on the outer part of the disc brake rotor. As a result, more accurate temperature profiles are obtained in the simulation. Heat power applied to the disc circularly through the brake pad projection on both sides during the brake event is calculated using Equations 1-2. [14]
Table 2. Specifications of the “Michigan 2019” endurance track.
Parameter |
Value |
Type of Track |
Temporary Circuit |
City |
Michigan |
Country |
United States |
Track Direction |
Forward Direction |
Total Track Length |
2168.21 |
Percent Left Corners |
33.96% |
Percent Right Corners |
32.46% |
Percent Straights |
33.58% |
Average Corner Radius |
25.4 m |
Minimum Corner Radius |
1.39 m |
Longest Straight |
45.95 m |
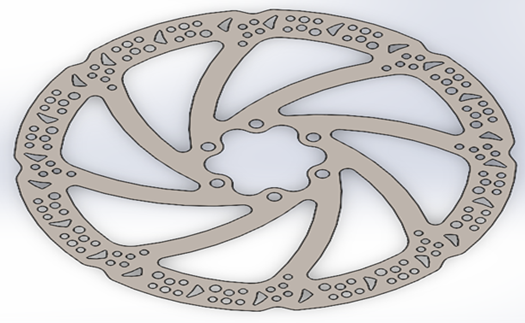

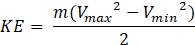
where:
- P is the power
- KE is the kinetic energy that will be converted to heat during the brake event,
- ΔT is the duration of the brake event,
- m is the ¼ of the mass of the vehicle and the driver,
- Vmax and Vmin are the starting and end longitudinal velocities of the vehicle.
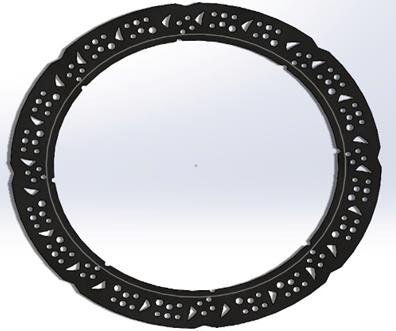
The heat convention coefficient between the rotor side surfaces and air is calculated based on Equations 3-4 for each acceleration and brake event. [14]
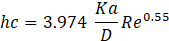
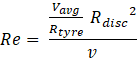
where:
- Ka is air heat transfer coefficient,
- D is the rotor diameter,
- Re is the Reynolds number,
- Vavg is average speed of the vehicle for the event,
- Rtyre is the radius of the tyre,
- Rdisc is the radius of the disc rotor
- v is air kinematic viscosity.
Values used in the calculations are listed in Table 3.
Table 3. Thermal analysis parameters.
Parameter |
Value |
m |
95 kg |
Ka |
0.0294 W/(mK) |
D |
0.161 m |
Rtyre |
0.2 m |
Rdisc |
0.0805 m |
v |
1.93 10 -5 kg/m.s |
2. 3. Optimization
Optimization of the disc brake rotor is performed using an equivalent thermal simulation (see section 3.3 for the methodology). A full factorial DOE with the variables thickness, inner diameter and disc material has been performed in Minitab software. Thickness values are defined as 2. 4 and 6 mm, inner diameter values are set as 12, 13 and 14 cm. Considering disc brake rotor material, plain carbon steel, AISI 4330 annealed steel are utilized in the thermal simulations. Maximum disc rotor temperature value of 873 K (600 °C) is set as a constraint and weight minimization is set as the optimization goal.
3. Results and Discussion
The outcomes are divided into three sections: The OptimumLap vehicle simulation and hand calculation results, “SolidWorks” thermal analysis results and optimization results.
3.1. OptimumLap Vehicle Simulation and Hand Calculation Results
Figure 4 show the outcomes of the OptimumLap simulation that is run for successive laps, which means that the starting vehicle speed is not equal to 0 kph. The car finishes one lap in 142 seconds. The vehicle was simulated to have a peak speed of 110 kph and a minimum speed of 17.5 kph. There are 70 braking and accelerating events in total. The events that has a duration of less than 0.2 seconds are neglected, and previous and later events are combined together. During braking and accelerating, the maximum longitudinal acceleration is simulated to be 6.8 m/s2 and the maximum longitudinal deceleration to be -19 m/s2 respectively. It can be noticed that the high deceleration values are due to additional downforce with aero components of the vehicle such as like and diffusers.
Table 4 presents a summary of the heat power for braking events and heat transfer coefficients for brake and acceleration events using vehicle speed results from OptimumLap software outcomes for a single lap. Only the first four and last two braking and acceleration events are displayed on the table due to space restriction.
Table 4. Heat power and convection heat transfer coefficient results obtained from OptimumLap software vehicle speed profile.
|
Start time (s) |
Start speed (m/s) |
End time (s) |
End speed (m/s) |
Duration (s) |
Average speed (m/s) |
KE (J) |
P (W) |
Re |
hc (W/m2.K) |
brake 1 |
0.63 |
26.49 |
1.66 |
14.62 |
1.0260 |
22.96 |
23170.02 |
22582.87 |
38548.07 |
241.57 |
acceleration 1 |
1.68 |
14.40 |
3.78 |
19.80 |
2.1010 |
17.51 |
NA |
NA |
29393.36 |
208.11 |
brake 2 |
3.79 |
19.76 |
4.01 |
18.27 |
0.2250 |
19.11 |
2695.03 |
11977.90 |
32088.80 |
218.40 |
acceleration 2 |
4.02 |
18.16 |
6.41 |
26.69 |
2.3910 |
21.67 |
NA |
NA |
36384.25 |
234.02 |
brake 3 |
6.42 |
26.73 |
7.15 |
16.82 |
0.7270 |
21.43 |
20506.81 |
28207.44 |
35973.87 |
232.56 |
acceleration 3 |
7.16 |
16.68 |
9.56 |
29.57 |
2.4030 |
23.17 |
NA |
NA |
38894.09 |
242.76 |
brake 4 |
9.57 |
29.49 |
11.05 |
11.28 |
1.4820 |
24.00 |
35273.57 |
23801.33 |
40291.24 |
247.52 |
…….. |
…….. |
…….. |
…….. |
…….. |
…….. |
…….. |
…….. |
…….. |
…….. |
…….. |
brake 34 |
128.50 |
23.45 |
129.77 |
10.44 |
1.2660 |
17.13 |
20952.82 |
16550.37 |
28757.28 |
205.62 |
acceleration 34 |
129.79 |
10.39 |
137.36 |
14.07 |
7.5683 |
11.43 |
NA |
NA |
19186.13 |
164.59 |
brake 35 |
137.37 |
13.93 |
137.81 |
7.71 |
0.4344 |
11.08 |
6392.32 |
14715.25 |
18596.21 |
161.78 |
acceleration 35 |
137.84 |
7.29 |
141.99 |
23.11 |
4.1555 |
16.86 |
NA |
NA |
28312.39 |
203.86 |



3.2. Solidworks Thermal Simulation Results
Using “SolidWorks”, a total of 70 braking and accelerating events were simulated inputting parameters such as power, heat transfer coefficient, duration and increment for each event using Table 4 values. Also, an ambient temperature of 298.15 K has been set for the first braking event in the first lap. Afterwards, for all the events after the first braking event, the temperature of the previous event was used as an input temperature for the current event. Simulations are continued until the temperature difference between two consecutive laps is less than 10 K (Figure 5). Figures 6 & 7 show the temperature distribution profile for the first braking event in the first lap and the first braking event in the second lap. Figure 8 shows the temperature profile for the maximum temperature the brake rotor reached (Lap2, Brake 15).
Table 5. “SolidWorks” simulation results.
|
Max Temp Lap 1 (K) |
Max Temp Lap 2 (K) |
Lap 2 and 1 Temp Difference (K) |
brake 1 |
663.60 |
1211 |
547.40 |
acceleration 1 |
607.90 |
1073 |
465.10 |
brake 2 |
649.70 |
1104 |
454.30 |
acceleration 2 |
583.90 |
954 |
370.10 |
brake 3 |
897.80 |
1244 |
346.20 |
acceleration 3 |
781.20 |
1060 |
278.80 |
brake 4 |
1256.00 |
1499 |
243.00 |
…….. |
…….. |
…….. |
…….. |
brake 34 |
1446.00 |
|
|
acceleration 34 |
1030.00 |
|
|
brake 35 |
1118.00 |
|
|
acceleration 35 |
899.90 |
|
|
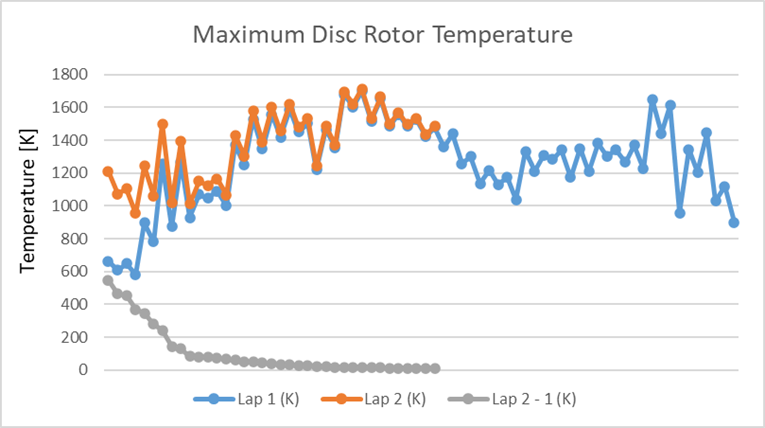
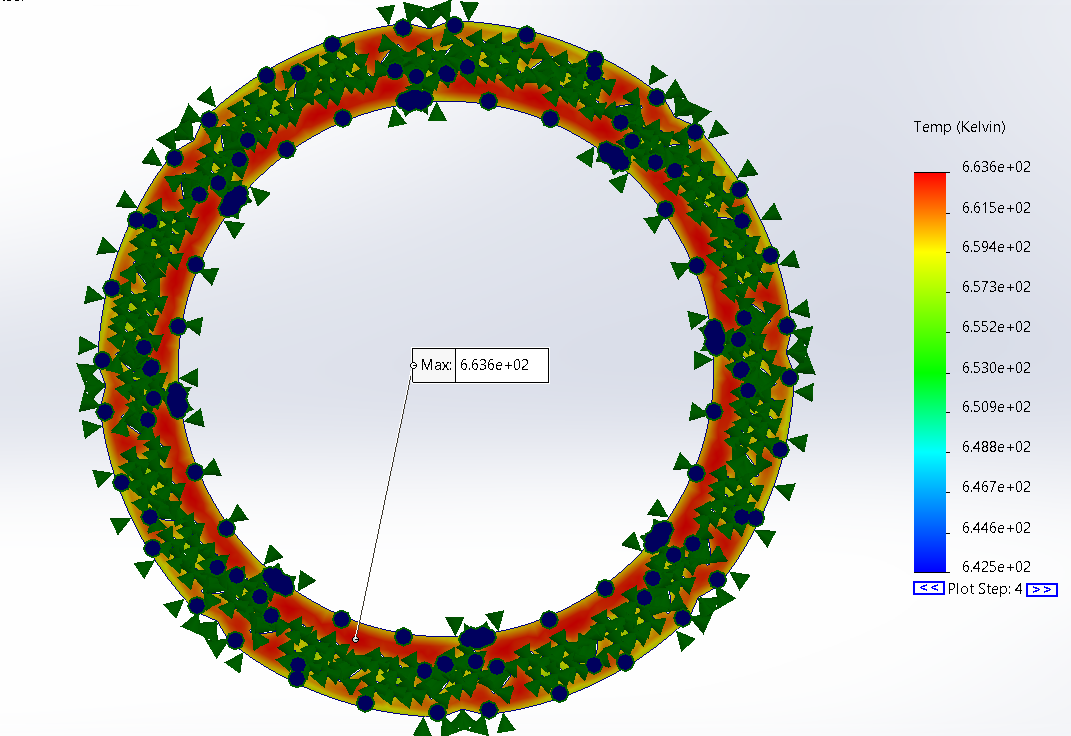
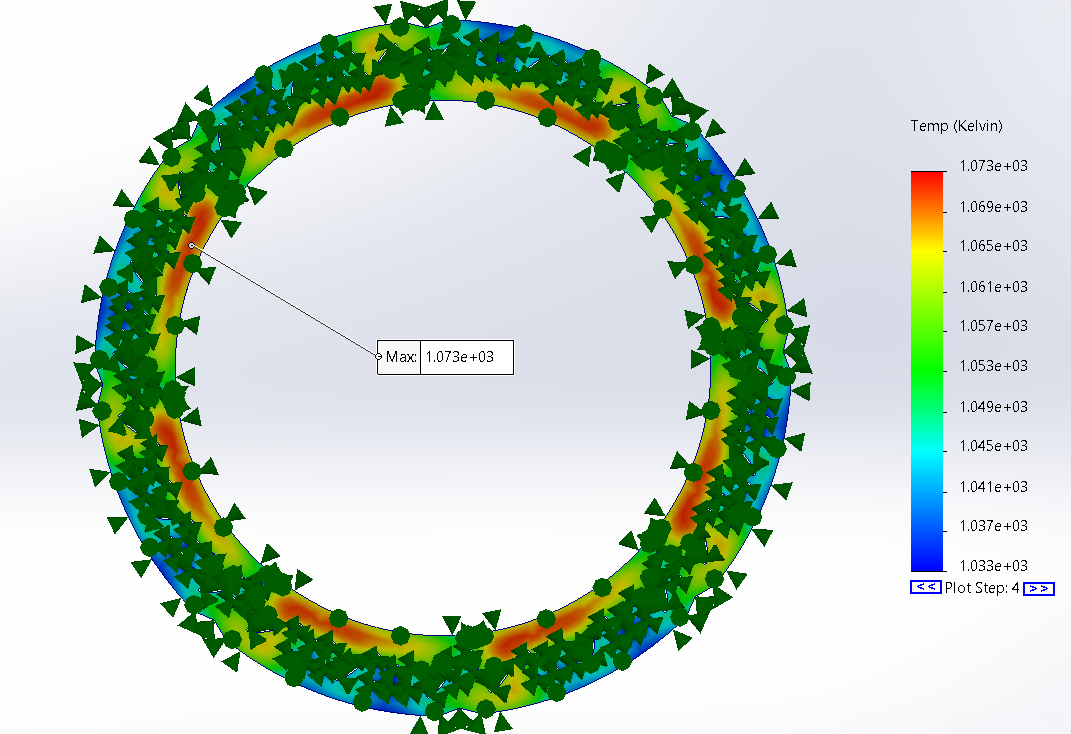
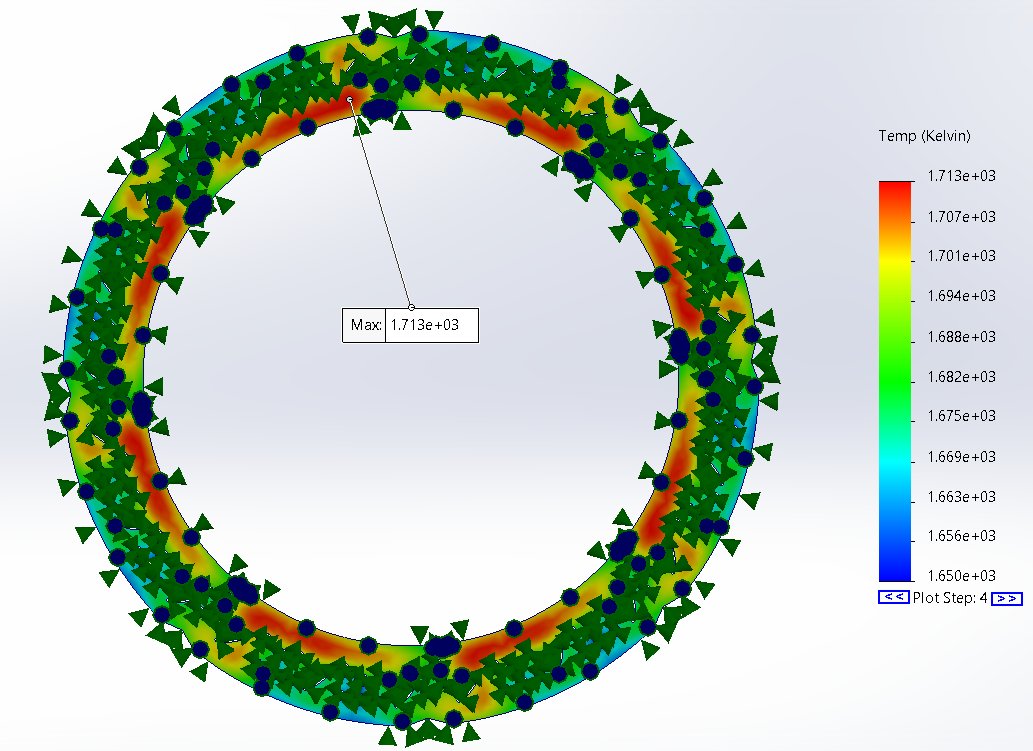
It is noticed that the maximum temperature that the brake rotor can reach is 1,713 K which is higher than the MDT of 873 K for the brake rotor to operate properly. Therefore, a modification at the disc brake rotor geometry of material is definitely necessary. However, any validation on the optimization and validation process requires running the 70 consecutive simulation and it is very time consuming. In order to make a disc brake rotor geometry and material optimization, 70 consequent thermal simulations are replaced with a single brake event simulation that aimed to achieve the maximum temperature. Considering the thermal equivalent simulation ambient temperature of 298.15 K is set with a brake heat power value of 45937 W and heat convection coefficient of 250.2 w/m2K. The simulation duration is set as 2.1 second. With the equivalent simulation maximum temperature of 1713 K and minimum of 1649 K where as the maximum temperature observed at lap 2 brake event 15 had maximum and minimum temperatures of 1713 K and 1650 K respectively (Figure 9). Comparison of the maximum and minimum temperatures observed proves that the equivalent single thermal simulation is appropriate to replicate the consecutive simulations.
3.3. Optimization Results
Minitab software is used in order to model the maximum brake disc rotor temperature and for the optimization process. A nonlinear regression model is built and response optimizer function is used to minimize the weight with the maximum temperature less than 873 K (Figure 10). Optimized parameters are determined as disc thickness value of 3.55 mm, inner diameter value of 12.2 cm with AISI 4330 annealed steel. As a result, a modified design of the brake rotor has been made with bigger thickness value as shown in Figure 11 obtaining a maximum temperature of 847.7 K which is less than the MDT of 873 K.
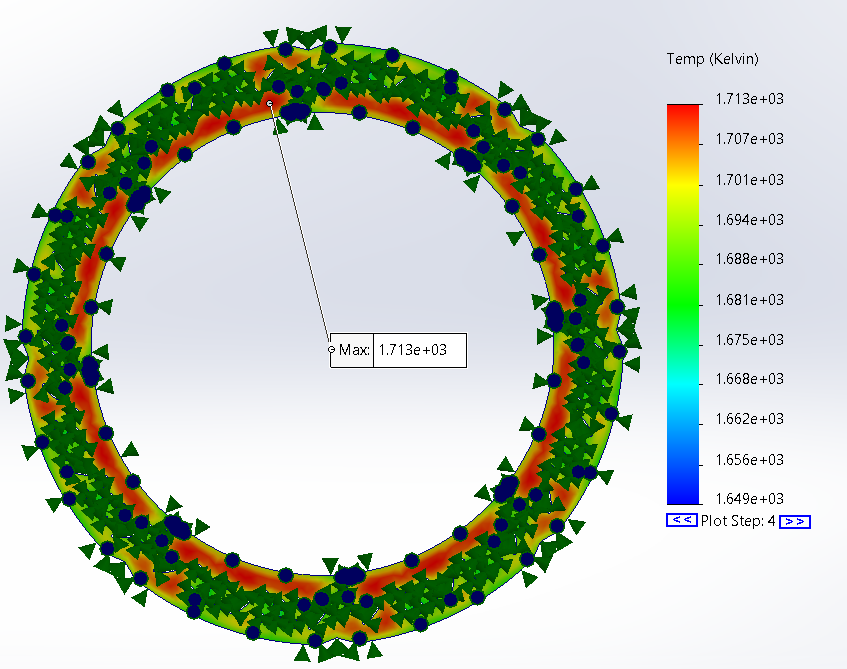
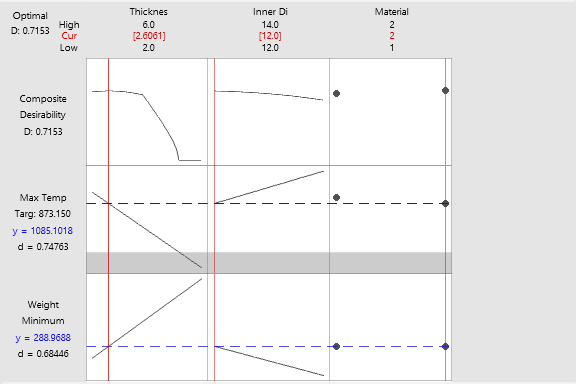
3.4. Discussion
SolidWorks thermal simulations use the input parameters obtained from the OptimumLap race simulations such as the duration of the simulation, heat power resulting from the brake event and heat transfer coefficient. Inevitably any potential error in the OptimumLap simulations will affect the SolidWorks thermal simulation results. Additionally, OptimumLap software results are generated based on vehicle maximum performance and optimum driving capabilities. During a race event, the drivers may not always be able to drive at the maximum possible speed conditions. Therefore, the simulations represent the worst-case conditions. Additionally, the accuracy of the OptimumLap simulations results depends on the input parameters for the race car and the track and is defined by the capability of the software. In general, OptimumLap is a well know software commonly used by many state-of-the-art universities participating in FSAE competitions [15 – 17]. Similarly, SolidWorks thermal simulations is a well-recognized tool for universities used for optimizing disc brake geometries [18 - 21]. Considering the thermal simulations in this study the heat transfer coefficients is obtained using the formulas from the study conducted by Huang and Chen [22]. The presented study does not involve any validation (due to lack of testing facilities). However, main goal of the presented study is to develop a methodology for disc brake rotor design to keep the maximum temperatures within the material maximum design limit. Therefore, the methodology can use used for any future disc brake rotor design task for a race simulation with the condition that the temperature profile results are validated with thermal camera test measurements.
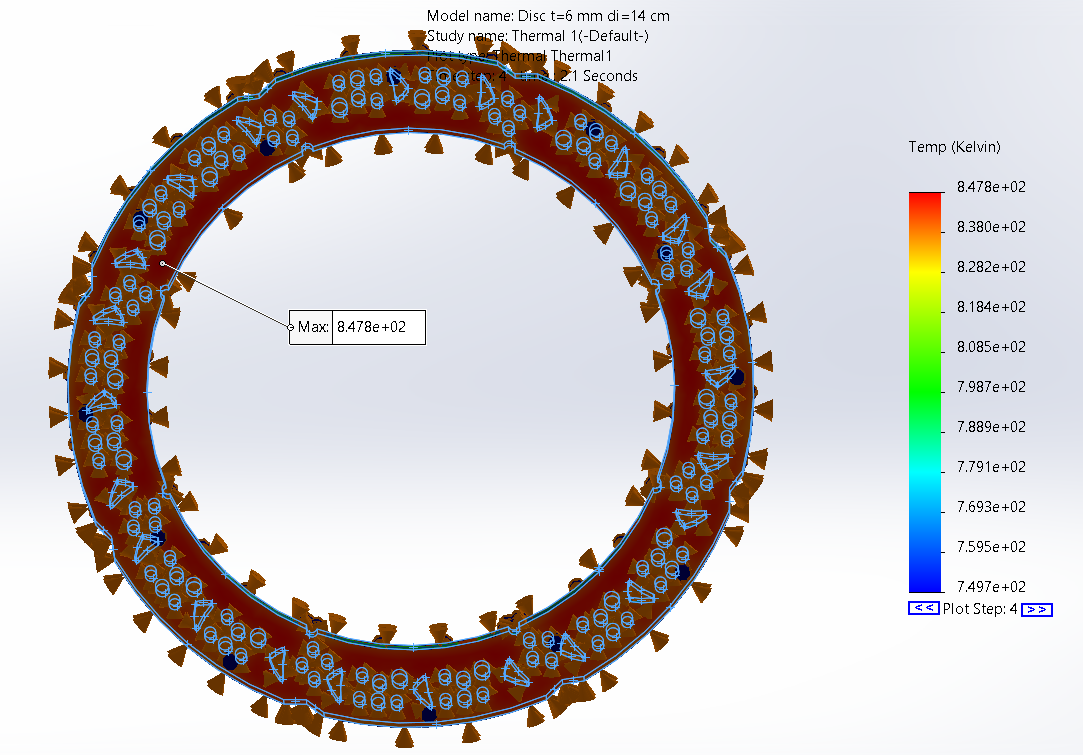
4. Conclusions
One of the main goals for the disc brake design in the FSAE student contests is rotor dimension optimisation. To outperform its competitors, the majority of colleges develop and produce their own rotors. Better results will undoubtedly come from optimising the rotor particularly for the event that is being attended, as every race has different circumstances. When thermal analysis is considered, the worst-case scenario - sequential braking during dynamic events (such endurance and autocross) when the disc rotors reach their maximum temperatures - is used to establish the boundary conditions.
Most of the prior research in the literature has relied on a single braking event, which is unrealistic given the worst-case situation in which acceleration and braking events occur consecutively. In order to optimise the design of disc rotors and account for subsequent braking and acceleration events in a racing scenario, this paper outlines a methodology. The vehicle and track pair are used to create the driving cycle for the race using OptimumLap. Following that, the thermal simulation's input parameters are determined using the acceleration and deceleration events. Heat power is computed using the kinetic energy change that occurs during the braking event, and the heat convection coefficient is computed for both occurrences taking average velocities into account. Thermal simulations showed that the maximum temperature achieved is higher than the MDT. A DOE based optimization is performed using mathematical modelling of maximum temperature using Minitab software via response optimizer. Thickness of the rotor is increased and inner diameter is reduced in order to reduce the maximum temperature and prevent the MDT breach while minimizing the weight.
References
[1] Formula SAE Knowledge. (n.d.).
View Article
[2] Formula. (2024, April 7). SAE International Student Chapter.
View Article
[3] Reddy V. C., Reddy M. G., Gowd G.H.,. (September, 2013). Website: www.ijetae.com (ISSN 2250-2459, ISO 9001:2008 Certified Journal, Volume 3, Issue 9, September 2013)
View Article
[4] Gupta, E., Bora, D. K. S., & A, R. (2022). Design and analysis of brake system for FSAE race car. Engineering Research Express. https://doi.org/10.1088/2631-8695/ac6ecd
View Article
[5] Vidiya. M, Singh.B. (March, 2017). Experimental and Numerical Thermal Analysis of Formula Student Racing Car Disc Brake Design. Retrieved from http://www.jestr.org/
[6] Mahajan. P. (2021). Design and analysis of brake disc assembly for an FSAE vehicle. Retrieved from https://www.sciencedirect.com/science/article/abs/pii/S2214785321051440
View Article
[7] Belhocine, A., Omar, W.W.Z., "Computational fluid dynamics (CFD) analysis and numerical aerodynamic investigations of automotive disc brake rotor", Australian Journal of Mechanical Engineering, 16(3), pp. 188-205, (2018).
[8] Karnik, A., Gudela, M.D., Sawant, A., Auti, S.M., "Numerical Analysis of Different Design Iterations of a Brake Disk", SAE Technical Paper, 1(5215), 2020
View Article
[9] Hugar, D., S., Kadabadi, U. B., & KLE Dr. M S Sheshgiri College of Engineering and Technology. (n.d.). Design and thermal analysis of disc brake for minimizing temperature. In International Research Journal of Engineering and Technology (IRJET) (p. 3483)
[10] Kumar.G, Thriveni. S, Reddy. M, Gowd. G. (August, 2014). Design analysis & optimization of an automotive disc brake. [Vol-1, Issue-3, Aug- 2014]
[11] Vecchiato, L.; Negri, M.; Picci, G.; Viale, L.; Zaltron, G.; Giacometti, S.; Meneghetti, G. Design and Development of a Brake Test Bench for Formula SAE Race Cars. Machines 2024, 12, 135.
View Article
[12] Vecchiato L, Capraro F, Meneghetti G. Design, Topology Optimization, Manufacturing and Testing of a Brake Caliper MADE of Scalmalloy® for Formula SAE Race Cars. Vehicles. 2024; 6(3):1591-1612.
View Article
[13] Carvalho, D. and Melo, C., "Simulation Model and Testing of a Formula SAE Brake System," SAE Technical Paper 2021-36-0430, 2022, https://doi.org/10.4271/2021-36-0430.
View Article
[14] Otkur, M. (2023). FSAE Single Seater Race Car Disc Brake Numerical Thermal Analysis: A Case Study. 8th Thermal and Fluids Engineering Conference (TFEC). https://doi.org/10.1615/tfec2023.ahp.046135
View Article
[15] Costa, R. and Bortolussi, R., "Lap Time Simulation of Formula SAE Vehicle with Quasi-steady State Model," SAE Technical Paper 2016-36-0164, 2016, https://doi.org/10.4271/2016-36-0164.
View Article
[16] Doyle, D., Cunningham, G., White, G., and Early, J., "Lap Time Simulation Tool for the Development of an Electric Formula Student Car," SAE Technical Paper 2019-01-0163, 2019.
View Article
[17] Dubey, M., Bhardwaj, S., Harish, R., & Kumar, M. S. (2020, October). Simulation of electric vehicle using scilab for formula student application. In IOP Conference Series: Earth and Environmental Science (Vol. 573, No. 1, p. 012026). IOP Publishing.
View Article
[18] Lokesh, S. (2021). Design and Thermal Analysis on Disc Brake Rotor Using Solidworks (Doctoral dissertation, Andhra University).
[19] Ismael, A. M. (2018). Study of thermal analysis of disc brake rotor for different disc brakes. International Journal of Mechanical Engineering and Technology, 9(3), 731-738.
[20] Rivera-López, J. E., García-León, R. A., Quintero-Orozco, A., Diaz-Torrez, E. J., Gutiérrez-Paredes, G. J., Echavez-Diaz, R., & Arévalo-Ruedas, J. H. (2019, November). Thermal and fluid-dynamic analysis of an automotive disc brake with ventilation pillars aerodynamic type. In Journal of Physics: Conference Series (Vol. 1386, No. 1, p. 012112). IOP Publishing.
View Article
[21] García-León, R.A., Quintero-Quintero, W. and Rodriguez-Castilla, M. (2020), "Thermal analysis of three motorcycle disc brakes", Smart and Sustainable Built Environment, Vol. 9 No. 2, pp. 208-226. https://doi.org/10.1108/SASBE-07-2019-0098.
View Article
[22] Huang, Y M., Chen, S., "Analytical Study of Design Parameters on Cooling Performance of a Brake Disk", SAE Technical Paper Series, 1(0692), (2006).
View Article
[1] Formula SAE Knowledge. (n.d.). View Article
[2] Formula. (2024, April 7). SAE International Student Chapter. View Article
[3] Reddy V. C., Reddy M. G., Gowd G.H.,. (September, 2013). Website: www.ijetae.com (ISSN 2250-2459, ISO 9001:2008 Certified Journal, Volume 3, Issue 9, September 2013) View Article
[4] Gupta, E., Bora, D. K. S., & A, R. (2022). Design and analysis of brake system for FSAE race car. Engineering Research Express. https://doi.org/10.1088/2631-8695/ac6ecd View Article
[5] Vidiya. M, Singh.B. (March, 2017). Experimental and Numerical Thermal Analysis of Formula Student Racing Car Disc Brake Design. Retrieved from http://www.jestr.org/
[6] Mahajan. P. (2021). Design and analysis of brake disc assembly for an FSAE vehicle. Retrieved from https://www.sciencedirect.com/science/article/abs/pii/S2214785321051440 View Article
[7] Belhocine, A., Omar, W.W.Z., "Computational fluid dynamics (CFD) analysis and numerical aerodynamic investigations of automotive disc brake rotor", Australian Journal of Mechanical Engineering, 16(3), pp. 188-205, (2018).
[8] Karnik, A., Gudela, M.D., Sawant, A., Auti, S.M., "Numerical Analysis of Different Design Iterations of a Brake Disk", SAE Technical Paper, 1(5215), 2020 View Article
[9] Hugar, D., S., Kadabadi, U. B., & KLE Dr. M S Sheshgiri College of Engineering and Technology. (n.d.). Design and thermal analysis of disc brake for minimizing temperature. In International Research Journal of Engineering and Technology (IRJET) (p. 3483)
[10] Kumar.G, Thriveni. S, Reddy. M, Gowd. G. (August, 2014). Design analysis & optimization of an automotive disc brake. [Vol-1, Issue-3, Aug- 2014]
[11] Vecchiato, L.; Negri, M.; Picci, G.; Viale, L.; Zaltron, G.; Giacometti, S.; Meneghetti, G. Design and Development of a Brake Test Bench for Formula SAE Race Cars. Machines 2024, 12, 135. View Article
[12] Vecchiato L, Capraro F, Meneghetti G. Design, Topology Optimization, Manufacturing and Testing of a Brake Caliper MADE of Scalmalloy® for Formula SAE Race Cars. Vehicles. 2024; 6(3):1591-1612. View Article
[13] Carvalho, D. and Melo, C., "Simulation Model and Testing of a Formula SAE Brake System," SAE Technical Paper 2021-36-0430, 2022, https://doi.org/10.4271/2021-36-0430. View Article
[14] Otkur, M. (2023). FSAE Single Seater Race Car Disc Brake Numerical Thermal Analysis: A Case Study. 8th Thermal and Fluids Engineering Conference (TFEC). https://doi.org/10.1615/tfec2023.ahp.046135 View Article
[15] Costa, R. and Bortolussi, R., "Lap Time Simulation of Formula SAE Vehicle with Quasi-steady State Model," SAE Technical Paper 2016-36-0164, 2016, https://doi.org/10.4271/2016-36-0164. View Article
[16] Doyle, D., Cunningham, G., White, G., and Early, J., "Lap Time Simulation Tool for the Development of an Electric Formula Student Car," SAE Technical Paper 2019-01-0163, 2019. View Article
[17] Dubey, M., Bhardwaj, S., Harish, R., & Kumar, M. S. (2020, October). Simulation of electric vehicle using scilab for formula student application. In IOP Conference Series: Earth and Environmental Science (Vol. 573, No. 1, p. 012026). IOP Publishing. View Article
[18] Lokesh, S. (2021). Design and Thermal Analysis on Disc Brake Rotor Using Solidworks (Doctoral dissertation, Andhra University).
[19] Ismael, A. M. (2018). Study of thermal analysis of disc brake rotor for different disc brakes. International Journal of Mechanical Engineering and Technology, 9(3), 731-738.
[20] Rivera-López, J. E., García-León, R. A., Quintero-Orozco, A., Diaz-Torrez, E. J., Gutiérrez-Paredes, G. J., Echavez-Diaz, R., & Arévalo-Ruedas, J. H. (2019, November). Thermal and fluid-dynamic analysis of an automotive disc brake with ventilation pillars aerodynamic type. In Journal of Physics: Conference Series (Vol. 1386, No. 1, p. 012112). IOP Publishing. View Article
[21] García-León, R.A., Quintero-Quintero, W. and Rodriguez-Castilla, M. (2020), "Thermal analysis of three motorcycle disc brakes", Smart and Sustainable Built Environment, Vol. 9 No. 2, pp. 208-226. https://doi.org/10.1108/SASBE-07-2019-0098. View Article
[22] Huang, Y M., Chen, S., "Analytical Study of Design Parameters on Cooling Performance of a Brake Disk", SAE Technical Paper Series, 1(0692), (2006). View Article