Volume 10 - Year 2023 - Pages 43-50
DOI: 10.11159/jffhmt.2023.007
Flow Boiling Heat Transfer of R134a at Varying Heat Fluxes
Ernest Gyan Bediako1*, Petra Dancova1, Anas F. A. Elbarghthi2, Tomas Vit1
1 Technical University of Liberec
Department of Power Engineering Equipment, Faculty of Mechanical Engineering, Technical University of Liberec,
461 17 Liberec, Czech Republic
2 Technical University of Liberec
Department of Applied Mechanics, Faculty of Mechanical Engineering, Technical University of Liberec,
461 17 Liberec, Czech Republic
ernest.gyan.bediako@tul.cz , petra.dancova@tul.cz, anas.elbarghthi@tul.cz, tomas.vit@tul.cz
Abstract - This study presents an experimental analysis of flow boiling heat transfer of R134a refrigerant in a smooth horizontal stainless-steel tube with the goal of investigating the effect of heat flux on heat transfer coefficient and dry-out characteristics. The experiment was performed for heat fluxes ranging from 7.2 kW/m2 to 47.4 kW/m2, mass flux of 300 kg/m2s and saturation pressure of 460 kPa. The results showed that at low heat fluxes, the heat transfer is predominantly controlled by convective boiling with a higher slope of heat transfer coefficient. As heat flux increases, nucleate boiling begins to predominate the heat transfer. The predominance of nucleate boiling is strongly experienced at low vapor quality when the higher slope in convective boiling begins to disappear as nucleate boiling dominates. Dry-out vapor quality incipience ( ) is not affected appreciably by heat flux. All the dry-out vapor quality incipience correlations investigated predicted well the vapor quality for which dry-out begins and ends.
Keywords: heat transfer coefficient, mass flux, heat flux, vapor quality, dry-out, R134a, convective boiling, nucleate boiling.
© Copyright 2023 Authors - This is an Open Access article published under the Creative Commons Attribution License terms Creative Commons Attribution License terms. Unrestricted use, distribution, and reproduction in any medium are permitted, provided the original work is properly cited.
Date Received: 2023-06-04
Date Revised: 2023-07-10
Date Accepted: 2023-07-20
Date Published: 2023-08-18
1. Introduction
Research in the area of two-phase flow boiling heat transfer has garnered a lot of attention for many decades now. This is due to the fact that flow boiling heat transfer is encountered in numerous industrial applications such as evaporators of heat exchangers, electronic cooling systems, boilers and many other thermal management systems. For two phase flow boiling heat transfer, key areas of interest that has drawn the attention of researchers include understanding the heat transfer characteristics, occurrence of dry-out, flow instabilities and properly predicting the heat transfer coefficient [1]. Despite extensive studies in this area, results published over the years have shown discrepancies on the effect of flow conditions such as heat flux, mass flux and saturation conditions on heat transfer coefficient. Also, the dominant mechanism that controls the heat transfer is not clear up to now. This is evidenced in the large number of prediction models available in literature with varying derivation concepts [2]. Flow boiling heat transfer is considered to be controlled by either convective boiling where the heat transfer coefficient is dependent on mass flux and vapor quality or nucleate boiling where the heat transfer coefficient is dependent on heat flux and saturation conditions or by both mechanisms where heat transfer coefficient depends on vapor quality for the varying effect of heat flux, mass flux and saturation conditions. For the effect of flow parameters such as heat flux, mass flux and saturation conditions, numerous studies have been conducted [3], [4] . However, the interrelation between these parameters on heat transfer coefficient is not clearly understood and with some contradicting opinions [5], [6].
For two phase systems, it is important to understand dry-out characteristics and control such occurrence. Dry-out, especially for annular flow occurs when the heating surface is deprived of liquid, which is as a result of gradual thinning of the annular liquid film moving along the tube wall. For this, there is a sharp drop in heat transfer coefficient which is as a result of a sudden rise in wall surface temperature. Going beyond this limit is not a safe operating condition for two phase devices. Understanding this phenomenon helps to know the maximum safe operation conditions for two phase devices [7], [8].
This research therefore investigates flow boiling heat transfer of R134a refrigerant with the goal of understanding the effect of heat flux on heat transfer characteristics, trend evolution and dry-out phenomenon. Because of contradicting results from different studies on the effect of flow parameter on heat transfer, this experiment was systematically conducted with small increment of vapor quality to be able to capture the trend evolution over a wide vapor quality range for an increasing heat flux.
2.0 Experimental Test Rig
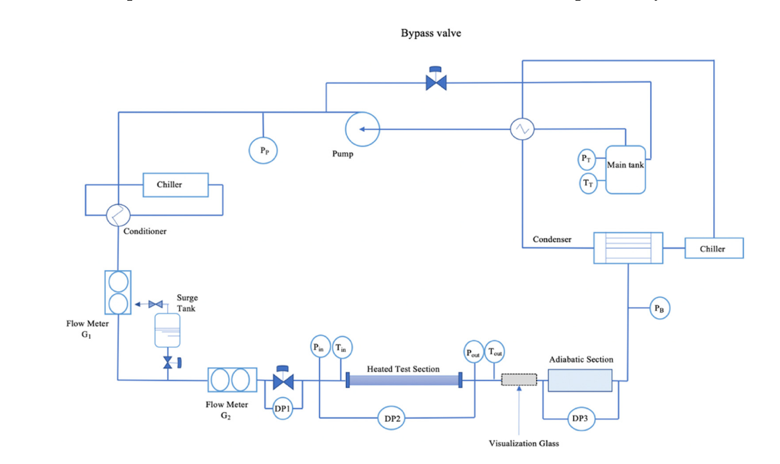
Figure 1 describes the experimental setup used in this study. The setup is a closed loop system that includes a condenser, a pump, a horizontal glass test section, a Coriolis flow meter, a visualization glass, and a tank filled with R134a refrigerant. The tank's saturation conditions are adjusted to control pressure, and a shell and tube type heat exchanger is used to control the inlet temperature of the working fluid. The test section has a length of 2035 mm, internal diameter of 5 mm, and an outer diameter of 8 mm, divided into 5 sections, each of which can be heated independently by joule's effect. The power input to each section is calculated using a controller and rectifier circuit that convert AC power to DC. To prevent heat losses, the test section's outer surface is insulated, and 17 thermocouples are fixed to the outside wall of the tube to measure temperature. Another set of thermocouples is used to measure the internal flow temperature at specific locations (top, bottom and sidewalls at locations 1117 mm and 1917 mm). The experimental data is recorded using a LabVIEW National Instrument data acquisition system at a frequency of 10Hz. The experiment is conducted by heating the facility to a desired power and then systematically decreasing the applied electrical heat input to avoid a jump in wall temperature observed at the onset of nucleate boiling and ensure reproducibility of the experiment.
2.1 Data Reduction
Heat losses, caused by convection or conduction through the surroundings, cables, and thermocouples, can cause the applied heat to vary from the electrical power input. By accounting for the heat losses, the total heat supplied is given by:

where V is voltage, I is the current supplied and Qloss is the heat loss obtained during calibration
The heat flux is thus obtained by:

where q" is the heat flux, di is the inner diameter and L is the length of the heated section of the tube.
Because the tube has a small diameter, measuring the temperature directly from the inner wall is challenging. As a solution, the temperature on the outer wall diameter is noted and a correction factor for the pipe's thermal resistance is applied. This correction involves using the heat conduction equation on a cylindrical wall with a constant heat flux to determine the inner wall temperature.
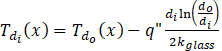
where Tdo(x) is the outer wall temperature, do and di are the outer and inner wall diameters respectively, kglass is the thermal conductivity of the glass.
From the balance of energy in the tube, the temperature of the fluid is determined by:

here, Tfluid,inlet is the inlet temperature of the fluid, is the mass flow rate and cp is the specific heat. The temperature of the fluid is assumed equal to the saturation temperature for instances where two phase flow occurs in the heater.
The local heat transfer coefficient is then calculated as:
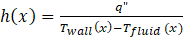
Experimental Validation
To assess the reliability of the experimental setup, heat transfer coefficient data for single-phase liquid and vapor flow was compared to the Dittus Beolter correlation, represented by the equation:

For this equation, Nu denotes the Nusselt number, Re represents the Reynolds number, and Pr signifies the Prandtl number. The comparison results can be seen in Figure 2. It can be observed that, the single-phase heat transfer results were predicted within a margin of ± 30% which is an acceptable range for trusting the experimental facility.
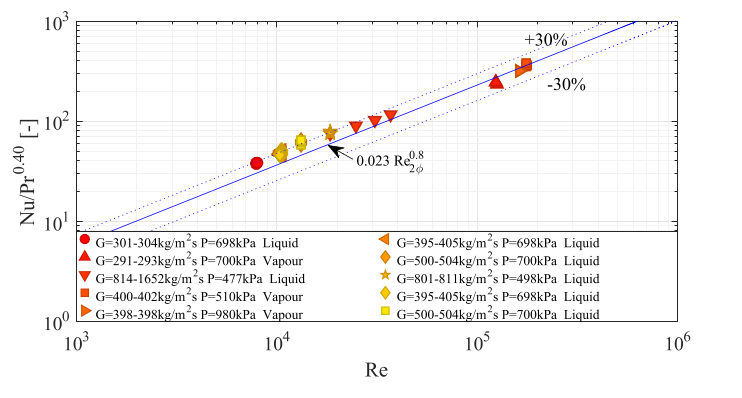
Results and Discussion
Figure 3 presents experimental results of heat transfer coefficient versus vapor quality for mass flux of 300kg/m2s, saturation pressure of 460 kPa for a varying heat flux from 7.2 – 14.3 kW/m2. With respect to the heat transfer coefficient, it can be observed that, at these low heat flux conditions, heat transfer coefficient increases with vapor quality until dryout occurs. This trend is characterized with big steepness in slope of the heat transfer coefficient up to dryout. For this case, convective boiling is deemed to dominate the heat transfer. Convective boiling dominates the heat transfer when heat transfer coefficient has a dependency on vapor quality and mass flux.
Increasing heat flux begins to decrease the slope toward zero as observed in Figure 4 for heat fluxes from 28.1 to 47.4 kW/m2. The zero slope of the heat transfer coefficient at high heat flux indicates the dominance of nucleate boiling characteristics. Nucleate boiling is assumed to be highly favored by heat flux and saturation condition with minimal effect of mass flux and vapor quality. It is worth mentioning that, for low heat flux conditions, there is an observance of a local minimum. This local minimum is a region of transition from one flow pattern (slug) to another (intermittent). The vapor quality at which the local minimum occur is highly influenced by heat flux. Also, for low heat flux conditions (7.2 and 14.3 kW/m2) where convective boiling dominates the heat transfer, increasing heat flux only produces an observable increase in heat transfer coefficient in the low vapor quality region. However, at high vapor quality, the plots merge into a single plot without showing any effect of heat flux. This indicates the dominance of convective boiling at high vapor quality.
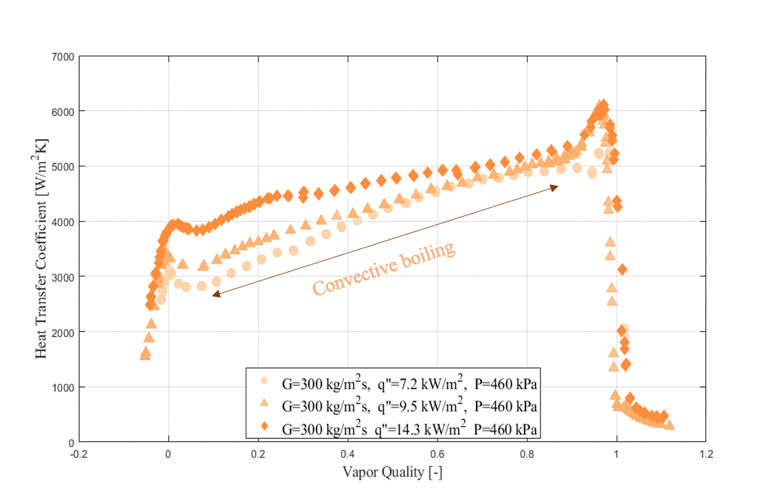
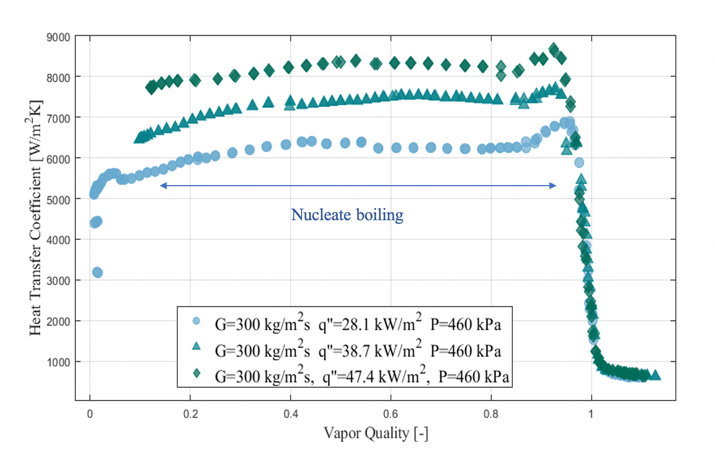
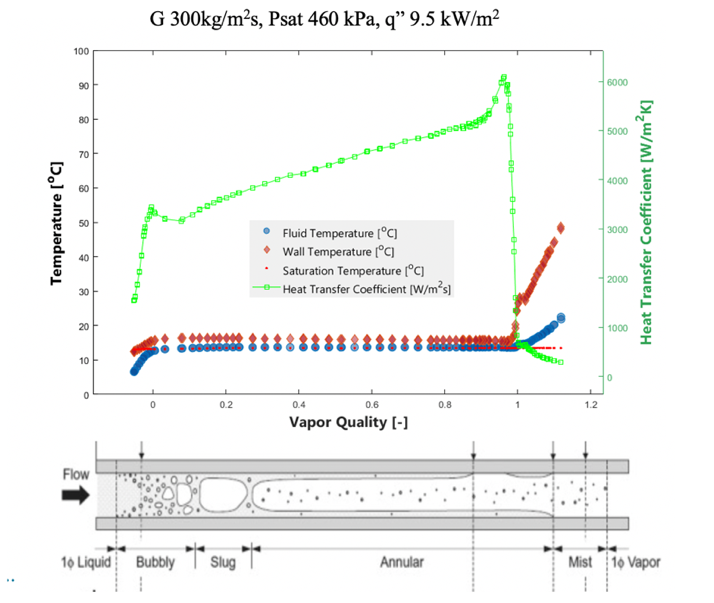
a. Convective boiling case
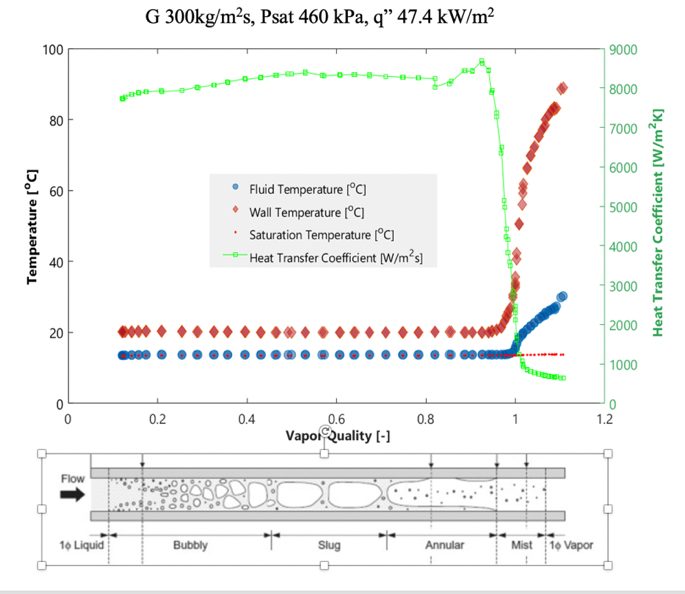
b. Nucleate boiling case
Figure 5a and 5b indicate plots of the wall, fluid, saturation temperature against vapor quality and their corresponding effect on heat transfer coefficient and flow patterns respectively. From these plots and as indicated in equation 5, for an imposed heat flux, the ratio of the applied heat flux to the difference between the heated wall temperature and the fluid temperature gives the local heat transfer coefficient. For the zone of saturated boiling, the heated wall temperature is higher than the bulk fluid temperature. The bulk fluid temperature is equal to the saturated temperature of the fluid (Tfluid = Tsat as observed in Figure 5a and 5b. At low heat flux conditions as observed in Figure 5a, with increasing vapor quality, bubbles begin to form, grow, detach from the heated walls and form slugs at low vapor quality. As vapor quality increases, annular flow develops where thin liquid films flow near the walls of the tube with vapor core at the center. Eventually, dry-out occurs where the liquid film dries out at higher vapor quality region where the wall temperature rises abruptly followed by the fluid temperature. This then leads to a sudden drop in the heat transfer coefficient. This is the case description for convective boiling heat transfer as described above. At high heat fluxes as observed in Figure 5b where nucleate boiling dominates the heat transfer, bubble formation predominantly controls the heat transfer coefficient. In this case, heat transfer coefficient is not appreciably affected with increasing vapor quality. At very high vapor quality, there is some effect of convective boiling as can be seen with the annular effects. Bubbles even nucleate in the thin liquid film in the annular region until dryout and mist flow occur where the liquid film dries out at higher vapor quality region and the wall temperature rises abruptly followed by the fluid temperature. This phenomenon is an accurate description of heat transfer coefficient in a horizontal tube as described by Kim and Mudawar [9] and temperature profile by Ohrby [10].
Dry-out Incipience Vapor Quality and Dry-out completion Vapor quality
Figure 6 depicts dryout incipience and dryout completion around the horizontal tube for the conditions studied. Dryout incipience vapor quality (xdi) in this study is considered the vapor quality at which the heat transfer coefficient
begins to drop abruptly in the high vapor quality region as implemented by Wojtan et al [8]. The point of interception of the near horizontal dashed line and the vertical dashed line at the top indicated as xdi in Figure 6 is the dryout incipience at the top wall of the horizontal tube. The dryout continues around the tube wall until it reaches the bottom wall where it is considered as dryout completion indicated as xde. From the plot, it can be observed that, heat flux does not have any appreciable effect on the dryout incipience vapor quality. It is also worth mentioning that, the region around the dryout incipience shows different characteristics without any notable trend. The heat transfer around this region either increases sharply before the sudden drop or it drops abruptly without any sharp increase. This could be due to the unstable nature of the heat transfer around this region before the change of flow pattern from annular to dryout.

Comparison with Prediction Methods
Because of the relevance of the dryout incipience vapor quality in two phase systems, different prediction methods have been developed under different conditions for predicting the dryout incipience vapor quality. This study considered the prediction methods of Wojtan et al, Mastrullo et al. and Chen et al. [11]–[13] shown in equations 6 – 9. The comparison of the trend of heat flux with dryout incipience vapor quality is shown in Figure 7
inception with heat flux increase. Although the prediction methods of Mastrullo et al [12] and Chen et al [13] were able to predict the dryout vapor quality within a reasonable range, they could not capture the trend evolution. Error! Reference source not found. below shows the comparison of experimental dryout vapor quality with the prediction methods and the mean absolute error (MAE) of each comparison.




Where ,
,
,
,
are the Weber number of the vapor phase, Froude number of the vapor phase, vapor density, liquid density, heat flux, critical heat flux, mass velocity, latent heat of vaporization, liquid phase viscosity and reduced pressure respectively.
Table 1: comparison of experimental dryout incipience and dryout completion vapor quality with the prediction method
Heat flux [W/m2] |
Xdi_Exp [-] |
Xde_Exp [-] |
Xdi_Wojtan [-] |
Xde_Wojtan [-] |
Xdi_Mastrullo [-] |
Xdi_Chen [-] |
7200 |
0.984 |
1.04 |
0.94 |
1.074 |
0.999 |
0.95 |
9500 |
0.972 |
1.03 |
0.93 |
1.074 |
0.999 |
0.95 |
1900 |
0.971 |
1.02 |
0.90 |
1.073 |
0.999 |
0.94 |
47400 |
0.93 |
1.01 |
0.85 |
1.072 |
0.999 |
0.93 |
Absolute Error (MAE) (%) |
6.3 |
4.3 |
3.4 |
2.4 |
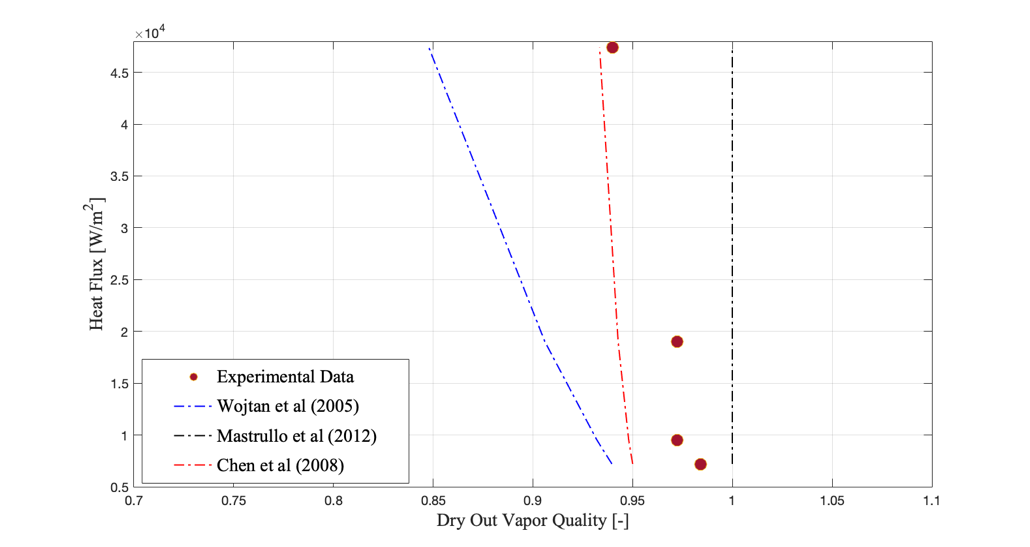
Conclusion
In this study, experimental analysis of flow boiling heat transfer of R134a refrigerant in a smooth horizontal stainless-steel tube with the goal of investigating the effect of heat flux on heat transfer coefficient and dry-out characteristics was performed. The experiment was performed for heat fluxes ranging from 7.2 kW/m2 to 47.4 kW/m2, mass flux of 300 kg/m2s and saturation pressure of 460 kPa. The main findings of this work are:
- At low heat fluxes, the heat transfer is predominantly controlled by convection boiling with a higher slope of heat transfer coefficient.
- As heat flux increases, nucleate boiling predominates the heat transfer. The predominance of nucleate boiling is strongly experienced at low vapor quality when the higher slope in convective boiling begins to disappear as nucleate boiling dominates.
- Dry-out vapor quality inception was not affected appreciably by heat flux contrary to what is generally reported in literature.
- All the dry-out vapor quality incipience correlations considered in this study predicted the inception vapor quality for which dry-out begins and ends reasonably well but only the correlation of Wojtan et al was able to capture the trend.
7. Acknowledgement
This research was funded by SGS project at the Technical University of Liberec with grant number SGS-2023-5345.
References
[1] M. V. Sardeshpande and V. V. Ranade, "Two-phase flow boiling in small channels: A brief review," Sadhana - Academy Proceedings in Engineering Sciences, vol. 38, no. 6, pp. 1083-1126, 2013, doi: 10.1007/s12046-013-0192-7. View Article
[2] E. G. Bediako, P. Dančová, and T. Vít, "Flow Boiling Heat Transfer of R134a in a Horizontal Smooth Tube: Experimental Results, Flow Patterns, and Assessment of Correlations," Energies (Basel), vol. 15, no. 20, Oct. 2022, doi: 10.3390/EN15207503. View Article
[3] R. J. da Silva Lima, J. M. Quibén, and J. R. Thome, "Flow boiling in horizontal smooth tubes: New heat transfer results for R-134a at three saturation temperatures," Appl Therm Eng, vol. 29, no. 7, pp. 1289-1298, 2009, doi: 10.1016/j.applthermaleng.2008.06.021. View Article
[4] C. A. Dorao, O. B. Fernandez, and M. Fernandino, "Experimental Study of Horizontal Flow Boiling Heat Transfer of R134a at a Saturation Temperature of 18.6 °c," J Heat Transfer, vol. 139, no. 11, 2017, doi: 10.1115/1.4037153. View Article
[5] S. Paul, M. Fernandino, and C. A. Dorao, "On the scaling of convective boiling heat transfer coefficient," Int J Heat Mass Transf, vol. 164, 2021, doi: 10.1016/j.ijheatmasstransfer.2020.120589. View Article
[6] R. Charnay, R. Revellin, and J. Bonjour, "Flow boiling characteristics of R-245fa in a minichannel at medium saturation temperatures," Exp Therm Fluid Sci, vol. 59, pp. 184-194, 2014, doi: 10.1016/j.expthermflusci.2014.01.011. View Article
[7] S. M. Kim and I. Mudawar, "Universal approach to predicting saturated flow boiling heat transfer in mini/micro-channels - Part I. Dryout incipience quality," Int J Heat Mass Transf, vol. 64, pp. 1226-1238, 2013, doi: 10.1016/j.ijheatmasstransfer.2013.04.016. View Article
[8] L. Wojtan, T. Ursenbacher, and J. R. Thome, "Investigation of flow boiling in horizontal tubes: Part I - A new diabatic two-phase flow pattern map," Int J Heat Mass Transf, vol. 48, no. 14, pp. 2955-2969, 2005, doi: 10.1016/j.ijheatmasstransfer.2004.12.012. View Article
[9] S. M. Kim and I. Mudawar, "Review of databases and predictive methods for heat transfer in condensing and boiling mini/micro-channel flows," Int J Heat Mass Transf, vol. 77, pp. 627-652, 2014, doi: 10.1016/j.ijheatmasstransfer.2014.05.036. View Article
[10] F. F. Fredrik¨ohrby, "Numerical modeling of subcooled nucleate flow boiling in engine cooling systems." 2014. Accessed: Feb. 23, 2023. [Online]. Available: https://hdl.handle.net/20.500.12380/207401
[11] L. Wojtan, T. Ursenbacher, and J. R. Thome, "Investigation of flow boiling in horizontal tubes: Part I - A new diabatic two-phase flow pattern map," Int J Heat Mass Transf, vol. 48, no. 14, pp. 2955-2969, 2005, doi: 10.1016/j.ijheatmasstransfer.2004.12.012. View Article
[12] R. Mastrullo, A. W. Mauro, and L. Viscito, "Flow boiling of R452A: Heat transfer data, dry-out characteristics and a correlation," Exp Therm Fluid Sci, vol. 105, no. February 2019, pp. 247-260, 2019, doi: 10.1016/j.expthermflusci.2019.04.006. View Article
[13] L. Cheng, G. Ribatski, L. Wojtan, and J. R. Thome, "New flow boiling heat transfer model and flow pattern map for carbon dioxide evaporating inside horizontal tubes," Int J Heat Mass Transf, vol. 49, no. 21-22, pp. 4082-4094, Oct. 2006, doi: 10.1016/J.IJHEATMASSTRANSFER.2006.04.003. View Article