Volume 9 - Year 2022 - Pages 136-147
DOI: 10.11159/jffhmt.2022.017
Hydrogen/Air Supersonic Combustion Modelling and Validation for Scramjet Applications
Guido Saccone1, Pasquale Natale1, Luigi Cutrone1, Marco Marini1
1CIRA (Italian Aerospace Research Centre)
Via Maiorise snc, 81043 Capua (CE), Italy
g.saccone@cira.it; p.natale@cira.it; l.cutrone@cira.it; m.marini@cira.it
Abstract - In the field of air-breathing hypersonic scramjet vehicles design and development, the Italian Aerospace Research Centre – CIRA contributed to an international project, called Stratospheric Flying Opportunities for High-Speed Propulsion Concepts – STRATOFLY, in collaboration with several European organizations, coordinated by Politecnico di Torino under the EC Horizon 2020 programme financial support. The aim of this project was the improvement of enabling technologies for the realization of a commercial hypersonic aircraft, able to fly at Mach 8, at 30÷35 km of altitude, for at least 4 hours with a minimum environmental impact and especially low NOx emissions. Understanding the complex, supersonic, turbulent, combustion processes occurring during scramjet operations is of fundamental importance. For this purpose, a thorough 0D kinetic assessment was carried out by means of the open-source Cantera software for the identification of the most suitable kinetic mechanisms, able to predict with satisfactory accuracy both the ignition delay times and the NOx emissions at the relevant scramjet operating conditions. Several kinetic schemes were investigated and the computed results were compared with the literature available shock tubes experimental data. In the entire investigated operative box, the best agreement, in terms of induction times, was achieved using the kinetic mechanism developed by Zettervall and Fureby with the exception of the ignition tests carried out in presence of argon as diluent bath gas, where the kinetic schemes by Kéromnès and CRECK together with the Aramco-II full mechanism provide the best matching. Moreover, for considering the generation of NOx, the three fundamental thermal route reactions by Zel’dovič, were added. Furthermore, full 3D CFD simulations were carried out by means of Ansys® Fluent in order to compare experimental data and evaluate the predictivity and accuracy of the chemical/kinetic sub-model conceived in this way when coupled with mixing, turbulence and fluid dynamic interactions arising from the simulations of the whole propulsive system. For the sake of comparison, the experiments carried out on the small-scale scramjet vehicle of LAPCAT-II by the HEG (DLR) were rebuilt.
Keywords: scramjet, hypersonic flight, hydrogen combustion, kinetic analysis, CFD.
© Copyright 2022 Authors - This is an Open Access article published under the Creative Commons Attribution License terms Creative Commons Attribution License terms. Unrestricted use, distribution, and reproduction in any medium are permitted, provided the original work is properly cited.
Date Received: 2022-09-21
Date Accepted: 2022-09-30
Date Published: 2022-10-23
1. Introduction
Civil hypersonic, scramjet, and trans-atmospheric transportation is becoming increasingly central in the global economy in order to connect passengers and goods between terrestrial antipodal hubs in a few hours.
For this purpose, hydrogen is a promising candidate as fuel for hypersonic air-breathing, long-term passenger transportation vehicles, because it can be burned in an efficient and reliable manner in supersonic combustion engines [1].
Furthermore, H2 is esteemed as a clean fuel with lower environmental impact compared to hydrocarbons, since the overall product of its complete oxy-combustion is only water, even if, when reacts with air, it produces also NOx, due to the elevated flame temperature reached during combustion. However, a comprehensive understanding of the supersonic hydrogen/air combustion could allow the optimized design of the combustion chamber able to decrease the flame temperature and consequently the pollutant NOx emissions.
Hydrogen combustion for scramjet applications is a very challenging process, consisting in several critical phenomena i.e., injection, compressible mixing, chemical kinetics, ignition, flame holding, vortices generation, turbulence combustion modelling, interactions among shock waves, boundary layer and heat release, etc. Moreover, scramjet operation is further complicated by the very short residence time (∼ 10-3 s) of the flow through the combustor chamber, which is of the same order of magnitude as the chemical kinetic ignition time of stoichiometric hydrogen/air mixtures at the typical conditions of scramjet combustion.
Since the experimental investigation is often unfeasible due to several difficulties in measuring multispecies, reacting, high-speed, unsteady flow fields [1], the most convenient way for the design and development of scramjet vehicles relies on CFD modelling and simulations. For this purpose, hydrogen/air kinetic mechanisms assessment is an important, preliminary task for the development of physical-chemical combustion models to be implemented into Computational Fluid Dynamics (CFD) codes. The optimal scheme arises as a suitable trade-off between the accuracy, required for a reliable description of ignition and combustion phenomena and the computational cost, associated with the available calculation speed and memory storage capacity. For this purpose, a preliminary zero-dimensional kinetic analysis of hydrogen/air combustion at the most relevant operative conditions for this application was performed using seven kinetic mechanisms of hydrogen ignition and combustion, selected as the most suitable ones based on the author’s experience and the literature review by Gerlinger et al. [2], Olm and co-workers [3] and Hu et al. [4] i.e., both the detailed [5] and reduced version of the Jachimowski mechanism [6-7], CRECK – 2012 [8], Kéromnès – 2013 [9] and Z22 -– 2018 [10]. Moreover, further two full mechanisms i.e., Aramco-II [11-13] and GRI-Mech 3.0 [14], conceived respectively for large hydrocarbons and natural gas modelling, but in any case, endowed with a well-established H2/O2 sub-mechanism, were investigated and used as references.
In addition, full 3D CFD analyses were carried out in order to numerically rebuild the achievements of a specifically conducted experimental testing campaign and compare laser absorbance measurements to computational predictions and evaluate the accuracy and reliability of such chemical/physical models. In particular, a reduced version of the Jachimowski scheme [6-7] was compared to the mechanism developed by Zettervall.
2. Kinetic Mechanism Assessment
- Jachimowski detailed – 1988
This is a detailed mechanism, consisting of 13 chemical species and 33 reactions.
It was based on experimental data acquired in shock-tube and laminar flame tests, carried out at NASA-Langley Research Center in the framework of the American National Aero-Space Plane (NASP) project with the aim to investigate hydrogen/air combustion for propulsion systems of vehicles able to operate at flight speed up to Mach 25 [5].
It includes all the main atomic, radical and molecular species of the hydrogen-oxygen-nitrogen system relevant at elevated Mach number conditions (M > 12) i.e., H2, O2, H, O, OH, H2O, HO2, H2O2, N, NO, HNO. Moreover, this mechanism was refined, through a comparison between calculated and experimental kinetic data. Therefore, rate coefficients for certain reactions were adjusted in order to obtain the best agreement with the experimental measurements of real hydrogen-air mixtures i.e., ignition delay times reported by Slack and Grillo [15] and laminar burning velocities of Warnatz [16] and Milton and Keck [17]. Other available experimental data were discarded because achieved for diluted e.g., H2/O2/Ar mixtures.
Comparison of the computed ignition delay times, calculated as a sudden increase of pressure in isochoric conditions, with the reflected shock-tube data of Slack and Grillo [15], reveals that at pressures of 0.5, 1 and 2 atm and for stoichiometric hydrogen/air mixtures, the induction times are very sensitive to the rate coefficients assigned to the second and ninth reactions of the whole scheme:
Furthermore, it was worth noting that at high flight Mach numbers (M > 12) conditions, reactions involving nitric oxide become greatly important. Indeed, experimental data by Slack and Grillo [15] show that a limited addition of nitric oxide to stoichiometric hydrogen/air mixtures decreases the ignition delay times. It is justified on the basis that NO converts the chain-terminating species HO2 into the very reactive OH radical, according to the following reactions:
So, the produced OH radicals strongly promote the chain branching reaction lowering the ignition delay times.
- Jachimowski reduced – 2008
This is the reduced version of the previous mechanism specifically formulated for hydrogen/air combustion and consisting of 9 chemical species and 12 reversible and elementary kinetic steps.
It is the result of a first simplification of the Jachimowski detailed scheme implemented by Star [6] and subsequently refined by Battista et al. [7].
The reactivity among nitrogen/hydrogen/oxygen was roughly described including only the three-fundamental thermal Zel’dovich generation reactions of NO [18]. Instead, other reacting paths leading to nitrogen oxides and dominant at low-temperature conditions were neglected. Therefore, the accuracy of this simplified kinetic mechanism is generally acceptable only at medium-high temperatures and atmospheric pressure. Otherwise, the computational efficiency and the numerical stability of the Jachimowski reduced mechanism [6-7] are quite elevated due to its compactness and thanks to the mathematical optimization accomplished on the Arrhenius parameters. Thus, it is very suitable to be implemented as a good chemical sub-mechanism also in 3D CFD simulations of supersonic combustion chambers exhibiting complex geometrical features and discretized with very fine computational meshes.
- CRECK - 2012
It is a hierarchical mechanism developed by the CRECK Modelling Group of Politecnico di Milano as a fundamental sub-mechanism to be incorporated into heavier fuels i.e., from hydrocarbons up to jet biodiesels. This kinetic mechanism was assessed both by means of 0D ignition delay times and 1D laminar flame speed calculations and by comparison against the available experimental data using a specifically formulated and developed in-house kinetic and thermodynamic tool i.e., OpenSMOKE.
It was upgraded starting from a detailed kinetic H2/O2 combustion scheme using new kinetic and thermodynamic measurements and it was validated over a wide range of temperatures, pressures and equivalence ratios [8]. Moreover, the mechanism’s performance at high pressures was greatly improved in particular by adapting higher rate parameters for the following termolecular reaction:
The authors increased the frequency factor of this step by a factor of 2 in comparison to the original mechanism [19] since further investigations demonstrated that the [RC-10] reaction is of noticeable importance for the laminar flame speed propagation at high pressure, while it is less sensitive under flow reactor and shock tube conditions. Furthermore, the Chaperon efficiencies of the bath gases were slightly modified in order to improve the agreement with the whole considered set of experimental measurements.
Additionally, the high-pressure limit was added to the mechanism according to Troe’s parameters models aimed to suitably describe the fall-off behaviour of the reaction [RC-10], which plays a paramount role, especially for very elevated pressure applications.
Finally, all the thermodynamic and transport properties of the CRECK – 2012 mechanism were taken from the CHEMKIN database with the significant exception of the enthalpy of the radicals OH and HO2 formation, which were revised according to the theoretical and experimental recommendations of Ruscic et al. [20].
More recently, the CRECK-2012 model was further improved and it coupled the H2/O2 with C1-C2 sub-mechanisms from [9, 21], as revised in [22], and heavier fuels sub-mechanisms from Ranzi et al. [23] to be efficiently used as syngas combustion chemical kinetic mechanism.
- Kéromnès – 2013
This is a detailed kinetic mechanism suitably conceived for investigating the oxidation of a syngas mixture consisting of H2/CO/O2/N2/Ar at pressures from 1 to 70 bar, over a temperature range from 900 to 2550 K and equivalence ratios from 0.1 to 4 [9]. This kinetic scheme involves 10 chemical species comprising also the excited radical OH* and interacting among them through 31 reversible reactions.
Several reactions were identified in the most relevant literature as being important for hydrogen oxidation concluding that its reactivity is mainly controlled by the competition between the chain-branching reaction:
and the pressure-dependent chain-propagating reaction:
For this reason, [RK-1] and [RK-9] reactions were extensively investigated and it was noticed that, at high-pressure conditions, the thermal decomposition of hydrogen peroxide (H2O2) through the pressure-dependent reaction:
For this reason, [RK-1] and [RK-9] reactions were extensively investigated and it was noticed that, at high-pressure conditions, the thermal decomposition of hydrogen peroxide (H2O2) through the pressure-dependent reaction:
is important in the prediction of accurate ignition delay times.
At the low-to-intermediate temperatures (< 1000 K), usually encountered in the Rapid Compression Machines (RCM), hydrogen oxidation is predominantly governed by reaction [RK-9], which leads to the production of hydroperoxyl radical i.e., HO2. It reacts with molecular hydrogen thus generating H2O2 according to the reaction [RK-17]. Finally, oxygenated water decomposes into two OH radicals as prescribed by the reaction [RK-15].
Instead, at the high temperatures experienced by shock tube equipment, the competition between [RK-1] and [RK-9] leads to a pressure dependence of ignition delay times. Indeed, depending on the pressure, at high temperatures, the oxidation process is mainly controlled by reaction [RK-1]. Due to the pressure dependence of reaction [RK-9], the temperature range in which the competition between the kinetic steps [RK-1] and [RK-9] occurs depends on the operative pressure.
The authors [9] investigated the effects of the reaction rate constants on ignition delay times by means of sensitivity analysis over a wide range of pressures between 1 and 100 bars and temperatures between 850 and 1200 K. They concluded that at low temperatures (<1000 K) and relatively low pressure (1 bar) the reaction kinetics is mainly controlled by the competition between the chain-branching reaction [RK-1] and the chain-terminating one [RK-9], while at more elevated temperature (>1000 K) the reactivity is only governed by the chain-branching reaction [RK-1]. Instead, under high pressure and intermediate temperature conditions, the reaction kinetics is determined by the sequence first identified by Pitz and Westbrook of steps [RK-15] and [RK-17], involving H2 and the HO2 radical producing and consuming H2O2 which subsequently decomposes to release two OH radicals leading to the chain branching reaction
The Kéromnes – 2013 mechanism includes also the OH* sub-mechanism in order to more accurately predict the experimental ignition delay times measured in shock tube tests recording the onset, the maximum rate of increase or the peak of the chemiluminescence emission of OH*.
- Z22 - 2018
This is a detailed, hydrogen/oxygen kinetic mechanism consisting of 9 species and 22 irreversible elementary reactions [10].
It arises the H2/O2 chemical structure from [24] with three additional fuel breakdown reactions from [25] and [26]
Analogously to Kéromnès et al. [9], also Zettervall and Fureby [10] highlight the importance of the competition between the chain-branching reaction [RZ-4] H + O2 → OH + O and the chain-propagating reaction [RZ-12]: H + O2 (+M) → HO2 (+M).
The first creates a pool of radical species effectively decreasing the ignition time, while the second produces the hydroperoxyl radical, which inhibits the chain-branching combustion process and therefore increases the induction time.
The competition between these reactions, and the consequent distribution of fast O, H and OH radicals and the slow radical HO2, is strongly temperature dependent. Furthermore, in the P-T diagram shown in Figure 1, a region of rapid ignition corresponding to chain-branching explosion at high temperatures and a region of slow ignition, associated with the thermal explosion at low temperatures are separated by a crossover region, corresponding to intermediate temperatures and dominated by extremely complex chemical processes. However, for instance, several ramjets, scramjets and dual-mode engines operate exactly in this connecting, critical zone.
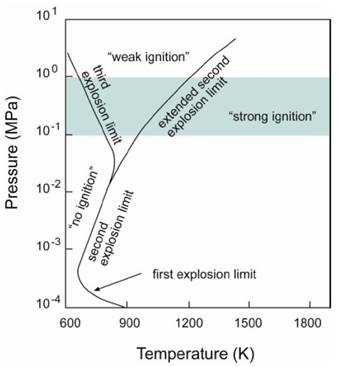
Z22 includes reactions important for the complete temperature spectrum, below and above the crossover region. In the mechanism development, authors spent particular efforts on improving its capability to match the ignition experimental behaviour also in the intermediate connecting region, because it is extremely useful for ensuring flame anchoring and stabilization within the supersonic combustion engines [1].
At low temperatures, reaction [RZ-12] predominates over reaction [RZ-4], the HO2 concentration enhances and new reaction paths become more prominent i.e., [RZ-16]: HO2 + HO2 → H2O2 + O2 and [RZ-20]: H2O + HO2 → H2O2 + OH.
These reactions increase the concentration of H2O2, which main consumption route is carried out by means of reaction [RZ-17]:
This step produces two OH radicals, which in turn generate H radicals through the reaction [RZ-8]:
[RZ-8] H2 + OH → H2O + H.
- Investigated Detailed Mechanisms
Large full mechanisms were analysed in order to strengthen the kinetic assessment and to achieve a more complete chemical description of the ignition and combustion processes. The considered detailed schemes are the GRI-Mech 3.0 [14] and Aramco-II [11-13].
GRI-Mech 3.0 is a widely known and well-consolidated detailed scheme formulated and thoroughly optimized with robust sensitivity studies to model the ignition and combustion of natural gas, essentially methane, including NO formation and the reburn chemistry. It was developed through computational and experimental research sponsored by the Gas Research Institute (GRI) and carried out at The University of California Berkeley, Stanford University, The University of Texas at Austin and SRI International [14].
Aramco-II was developed by the National University of Ireland Galway in a hierarchical way using a bottom-up approach and starting with an H2/O2 sub-mechanism, followed by a C1 sub-mechanism and has grown to include larger carbon species such as ethane, ethylene, acetylene, allene, propyne, propene, n-butane, isobutane, isobutene, 1-butene and 2-butene, and oxygenated species including formaldehyde, acetaldehyde, methanol, ethanol, and dimethyl ether. This mechanism was validated against a large array of experimental measurements including data from shock tubes, rapid compression machines, flames, jet-stirred and plug-flow reactors [11-13]
3. 0D Kinetic Modelling
0D time-dependent simulations of perfectly stirred i.e., homogeneous and isochoric, adiabatic batch reactors, filled with premixed gaseous reacting hydrogen/air mixtures were carried out by using the kinetic and thermodynamic open-source Cantera software [27] under Python interface and the seven investigated mechanisms.
The mathematical-chemical model consists in the following mass and energy balance equations:
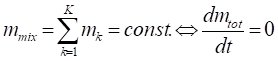
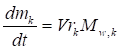
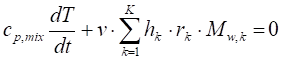
where m stands for the mass, V for the volume Mw for the molar amount, h for the enthalpy, T temperature, cp the specific heat at constant pressure, t the time and r the reaction rate, while the subscript mix refers to the overall reacting mixture and k to a single kth chemical species.
4. Results and Discussion
In this section, from Figure 2 to Figure 6 the comparison between the computational ignition delay times, calculated as described in the previous paragraph using the seven investigated kinetic mechanisms and the corresponding experimental data associated to the same initial temperature, pressure and equivalence ratio provided by several researchers and measured within shock tube tests is presented.
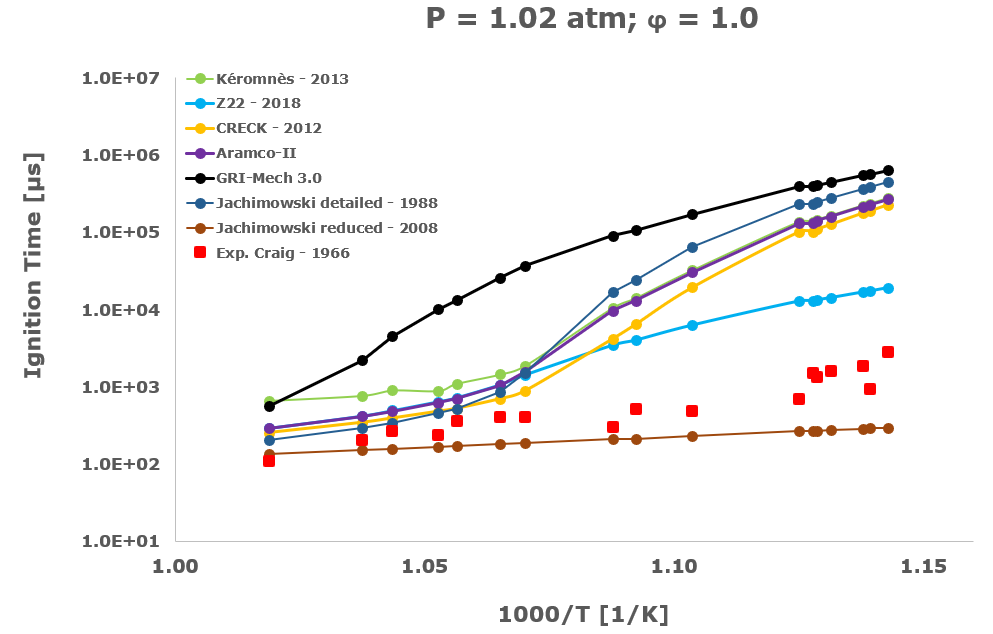

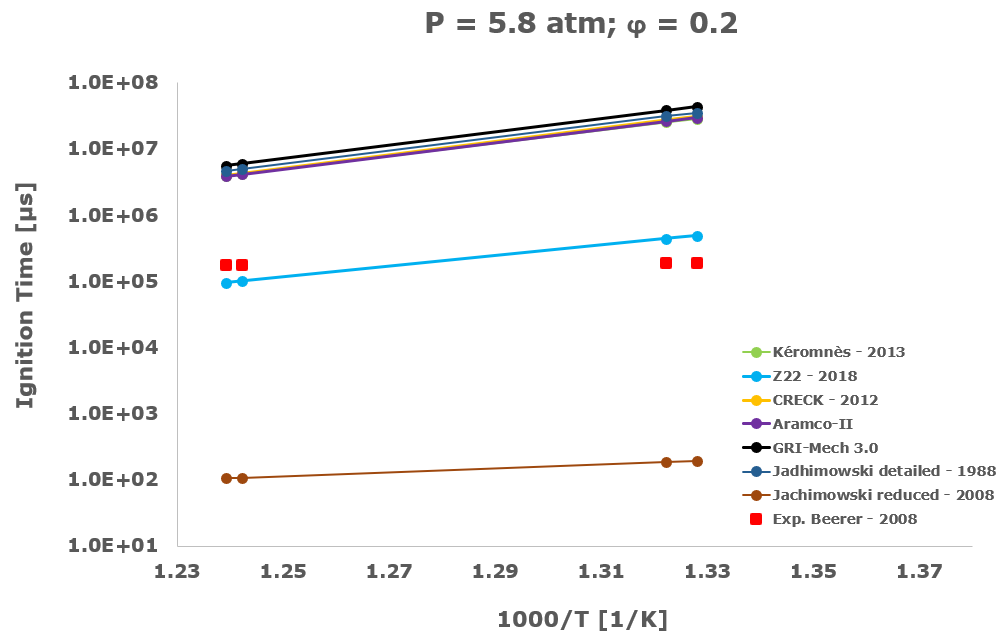
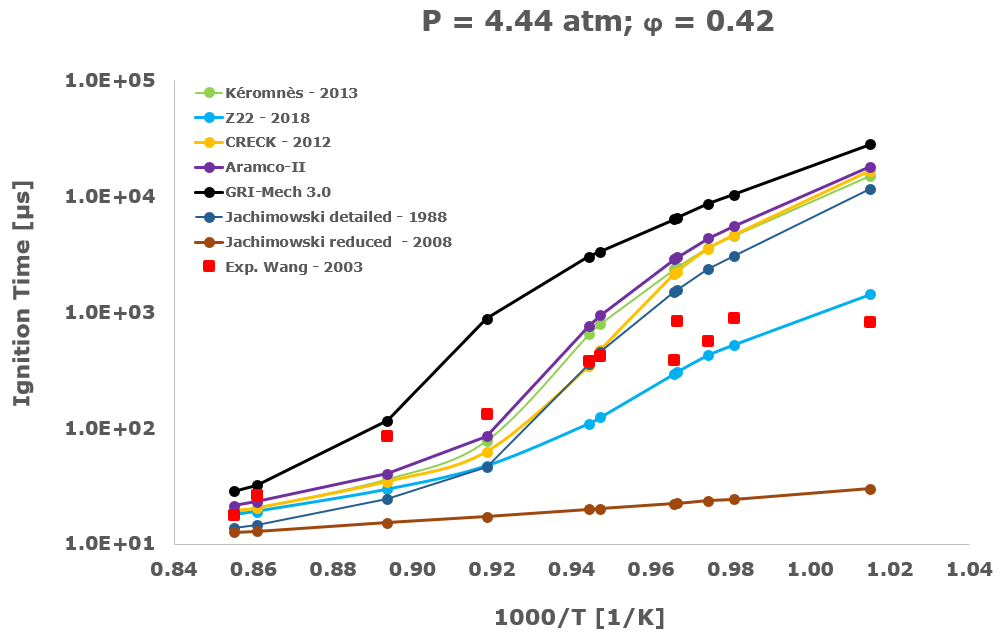
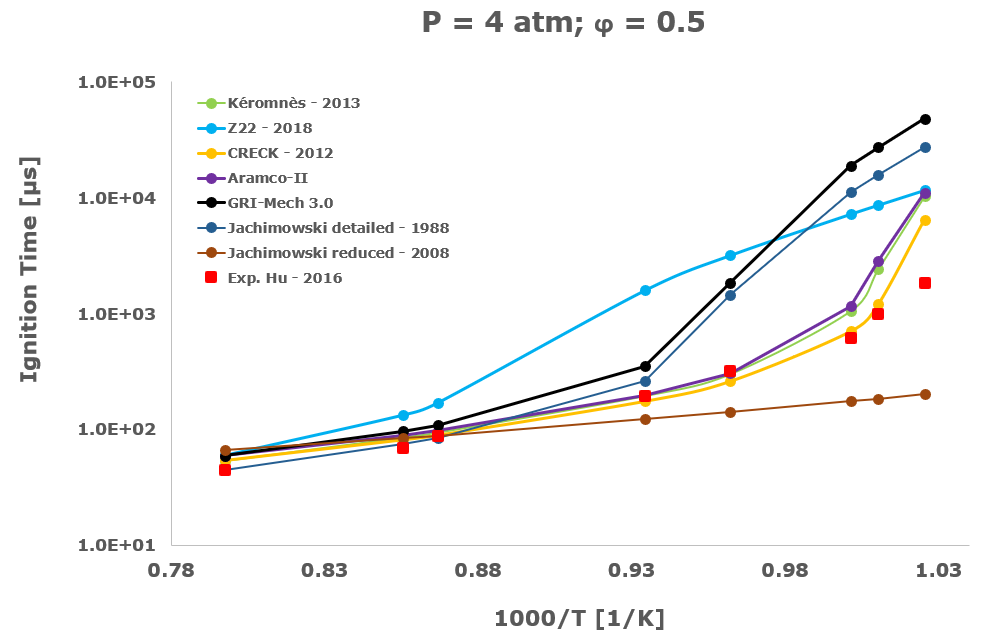
Among the several literatures available experimental datasets, the measurements performed by Craig – 1965 [28], Wang – 2003 [29], Beerer - 2008 [30], and Hu [4] were selected since acquired at experimental conditions, listed in Table 1, which better suits the STRATOFLY vehicle propulsive system working regime i.e., pressure up to ~6 bar, reacting mixture between stoichiometric and fuel lean composition and the lower possible inlet temperatures.
Table 1. Operative conditions for Cantera simulations.
Temperature [K] |
~750 |
~1800 |
Pressure [atm] |
1.2 |
5.8 |
Equivalence ratio |
0.2 |
1 |
Considering the experimental measurements of hydrogen ignition and combustion in which the oxidant is direct air i.e., Craig – 1965 [28], Wang – 2003 [29] and Beerer – 2008 [30], the best agreement between computational and experimental data was achieved by the Z22 [10] kinetic mechanism. On the contrary, the CRECK [8] and the Kéromnés [9] kinetic schemes show a satisfactory agreement only for high temperatures and low pressures. Otherwise, in the crossover region, associated with intermediate-low temperatures and pressure above 2 bar, only the Z22 [10] exhibits quite good behaviour.
Instead, examining the results obtained with the Hu dataset [4], they show that at a pressure equal to 4 atm and, above all, in presence of argon as bath and thermal diluent gas, the hydrogen oxidation is well described only by the CRECK [8], Kéromnès – 2013 [9] and by the Aramco-II schemes [11-13], while the Z22 [10] exhibits a significant mismatch compared to the test measurements also at the simulated low-temperature conditions. This peculiar behaviour is probably due to the rate-limiting effect exerted by the pressure-dependent reactions, in which the Chaperon efficiency plays an important role, and is sensitive to the geometrical characteristics of the atoms or molecules used as bath diluent gases.
The Jachimowski reduced mechanism arising from the chemical/mathematical optimization and the refinement work carried out by Battista et al. [7] shows a good agreement with the experimental data only at near atmospheric pressure. At these conditions, the ignition behaviour is surprisingly better than the Jachimowski detailed version [5] and also more satisfactory than the other investigated full or compact schemes. The better matching achieved by the Jachimowski reduced scheme [7] is probably justified by the suitable cancellation from the original mechanism of the slow and high activation energy steps included in the detailed release [5] of this scheme. These steps are exactly responsible for an increase in the ignition delay times at practically all the tested initial temperature conditions.
Finally, the ignition delay times calculated using the GRI-Mech 3.0 [14] are always very far from the experimental data. This behaviour confirms the accuracy and reliability of the GRI-Mech 3.0 scheme only for natural gas and especially methane combustion, while at low temperatures and medium pressures it is not able to capture the complex and strongly non-linear ignition characteristics of the hydrogen/air combustion.
Based on the present data, the most suitable kinetic mechanism to be embedded in mathematical models for CFD simulations of supersonic combustion in ramjets, scramjets and dual-mode engines is exactly the hydrogen oxidation scheme by Zettervall and Fureby [10]. Moreover, to adequately describe the hydrogen/air combustion, the three fundamental NO generation reactions by Zel'dovič [18] were included.
4. CFD Results and EXP comparison
During the H2020 STRATOFLY project, a ground-based testing of a small-scale version of LAPCAT-II M8 vehicle was successfully tested in HEG wind tunnel at the German Aerospace Center - DLR [31]. Through the test campaign, several experimental data (EXP) were collected useful for comparison to CFD predictions. Simulations were performed by means of Ansys Fluent®, according to experimental boundary conditions and implementing the chemical/kinetic sub-model assessed and 0D validated as described in the previous section.
In Figure 7, experimental data are reported as square dots.
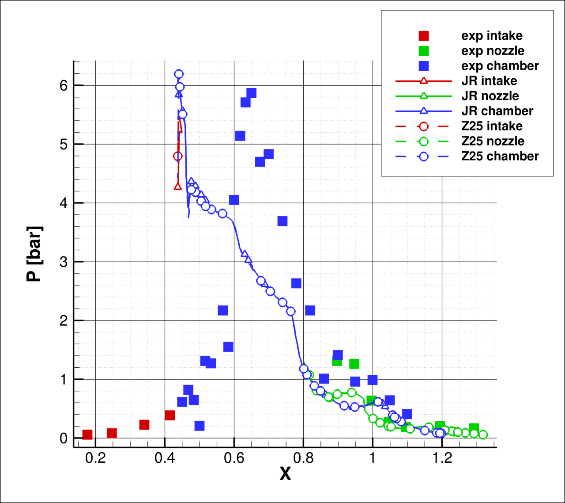
Different colours represent different acquisition lines: intake line (red), on the middle section of the intake; chamber line (blue), on the side of the combustion chamber; nozzle line (green), on the middle section of the expansion nozzle. In order to perform faster CFD simulations, the vehicle geometry was simplified. In particular, the intake was removed and only the combustion process, along with nozzle expansion, was simulated. In addition, only one-half of the vehicle was considered, thanks to the symmetry of the configuration. Without the intake, it was not possible to apply wind tunnel conditions. The inlet of the computational domain was the initial section of the combustion chamber (X=0.41 in Figure 8).
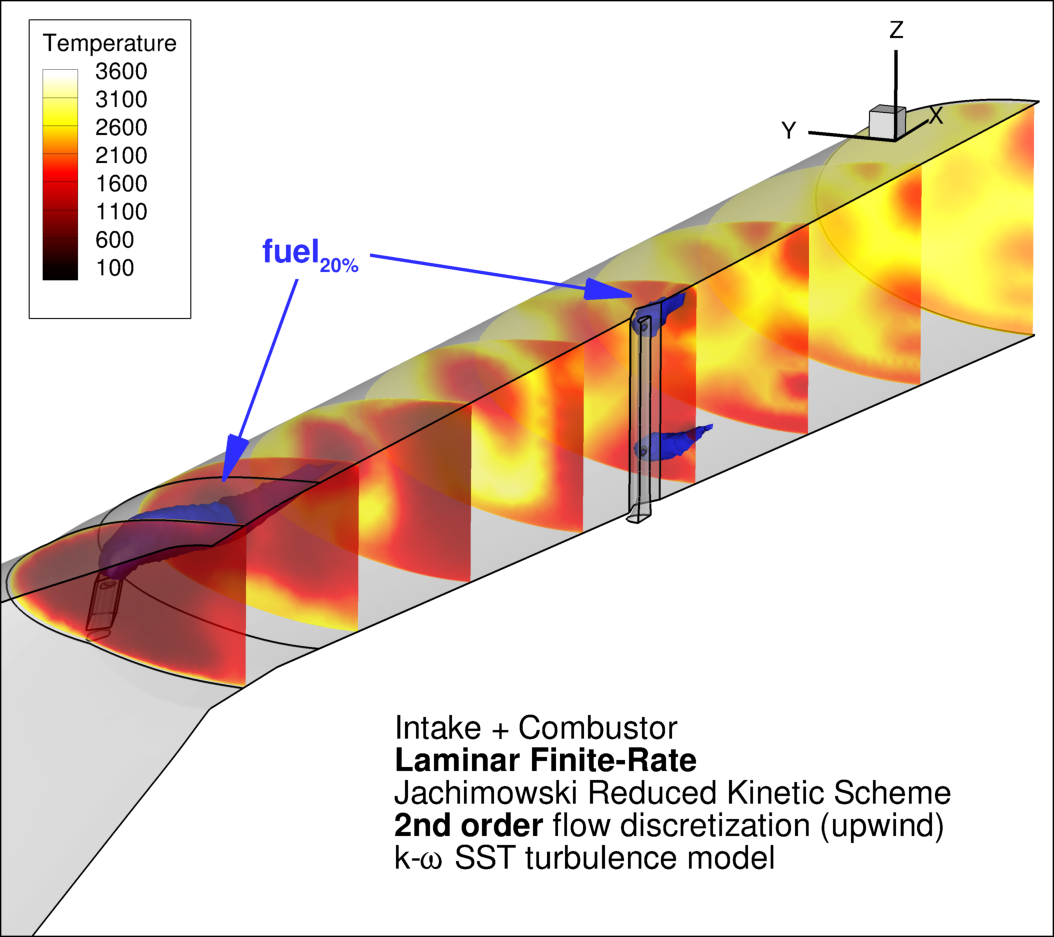
This is the reason why CFD results start over experimental data. In Figure 7, triangle markers represent the solution obtained by means of the reduced scheme due to Jachimowski [7] (JR label); circle markers represent the Z25 [10, 18] solution. The results provided by the two schemes are quite similar.
An unexpected compression occurs just after the domain inlet. This is due to the abrupt temperature increase caused by the combustion process. Even if the intake CFD and EXP data cannot match each other, due to this assumption, the predicted pressure value is consistent. This enables both kinetic schemes (JR as well as Z25) to be accountable for 3D CFD simulations of the H2-O2 combustion.
In Figure 9, some temperature contour plots are reported over slices of the combustion chamber.
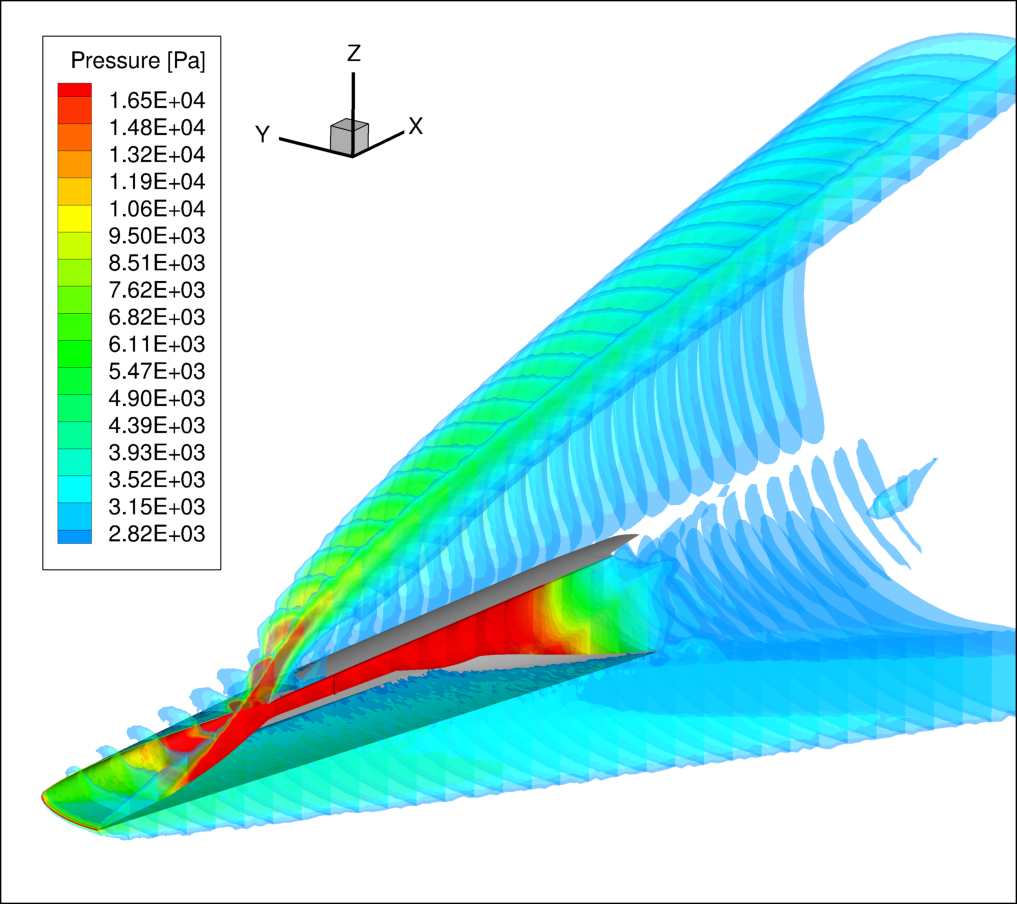
This solution relates to JR solution (see Figure 8). Iso-surface of 20% mass-fraction of fuel (hydrogen) is also reported. The CFD run was carried out using the Eddy Dissipation Concept combustion model, standard k-ε turbulence model SST and second-order upwind discretization scheme.
Once kinetic schemes were both enabled for CFD, the reduced version of Jachimowski mechanism [6-7] was selected because associated with a lower computational cost. The full vehicle was simulated, using the wind tunnel conditions. In Figure 9, pressure plots over X-coordinate slices are reported for the full vehicle CFD run. Thanks to the Tunable Diode Laser Absorption Spectroscopy (TDLAS) technique, the test campaign performed by DLR-HEG (High Enthalpy Shock Tunnel in Göttingen, Deutsches Zentrum für Luft- und Raumfahrt) collected information about mass fraction along several lines of sight. Indeed, TDLAS is a technique for concentration measurement able to achieve very low detection limits (order of ppb). In addition, it can be used for temperature, pressure and velocity observation, very useful for specific applications. The measure is obtained as an integral of the measured quantity along the line of sight. For this reason, the presented numerical results will be averaged by several methods, in order to achieve a better matching representation. In Figure 10, measurement points are reported over the geometry of the small-scale vehicle.
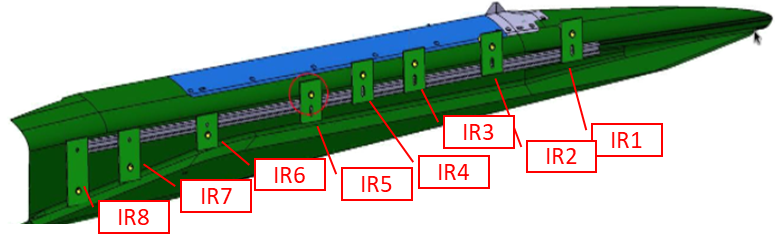
The lines of view cross those points and are aligned in Y-direction (cfr. Fig. 9 for the coordinate system). In Figure 11, the measurements of NO mass fraction concentration are reported.
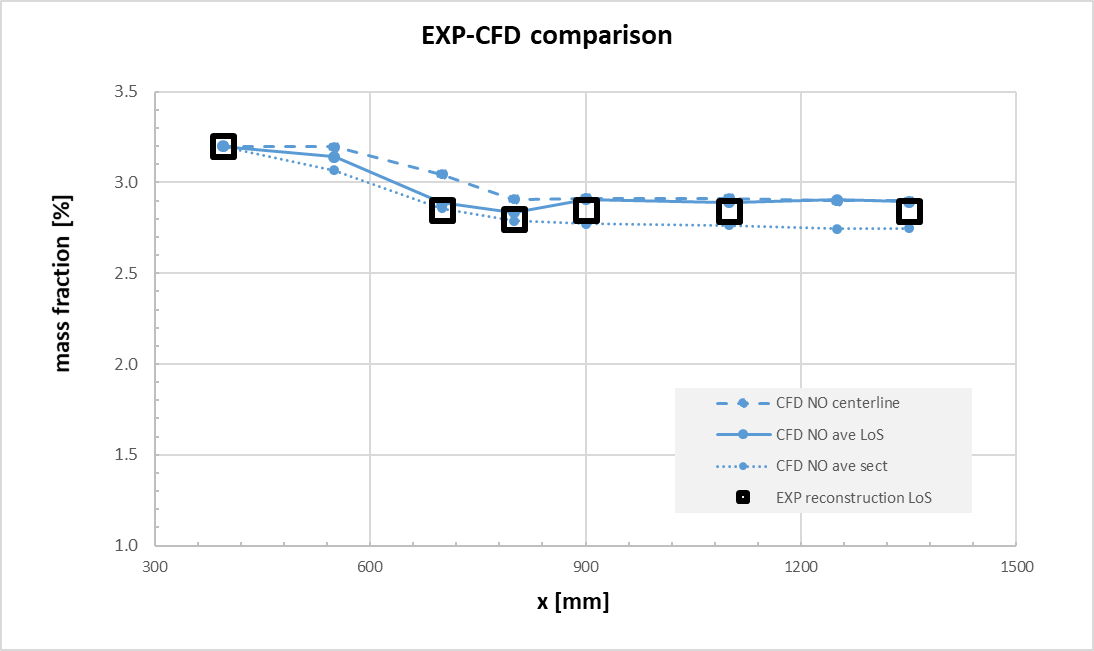
Square markers represent experimental data, while lines represent CFD results. Several averaging methods were used in order to compare measurements at the intersection of the centreline; average along the section (at the same X coordinate); average along the line of sight. Figure 11 confirmed that NO prediction is quite matching the experimental results. This enabled the use of the Zel’dovich mechanism for NOx production [18]. Moreover, in Figure 12, the comparison of water content, confirmed also that the selected kinetic scheme can predict the proper combustion production rate, even if it is a reduced one.
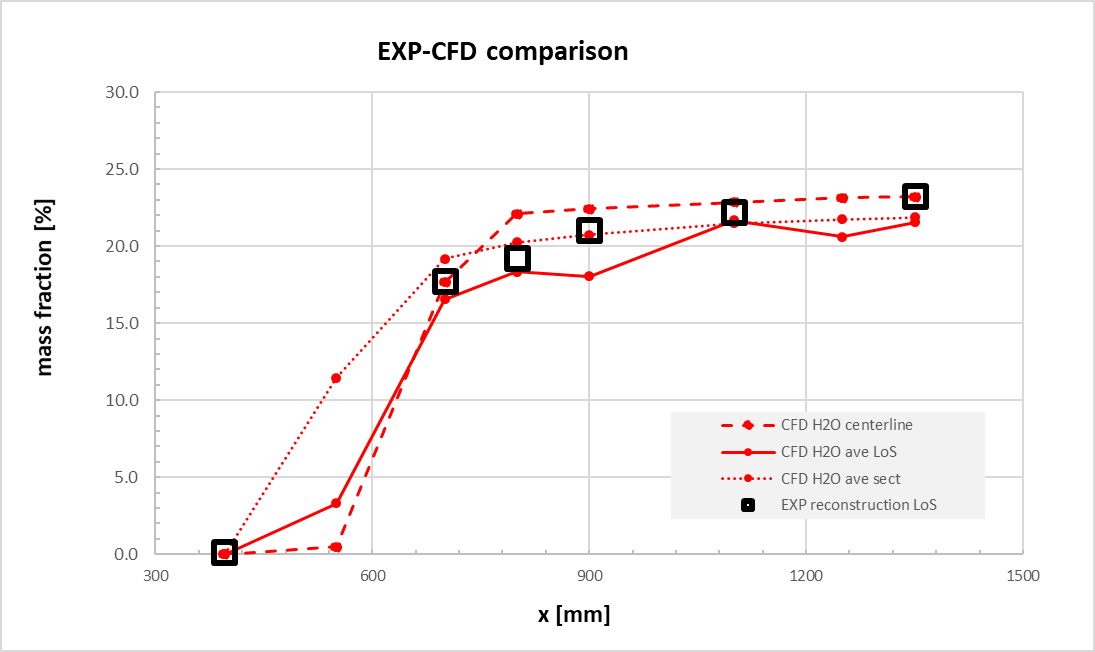
In Figure 13, NO concentrations are reported over IR locations (see Figure 10) for three different levels of mesh-grid refinement. By this comparison, the mesh convergence is checked and enabled CFD results.
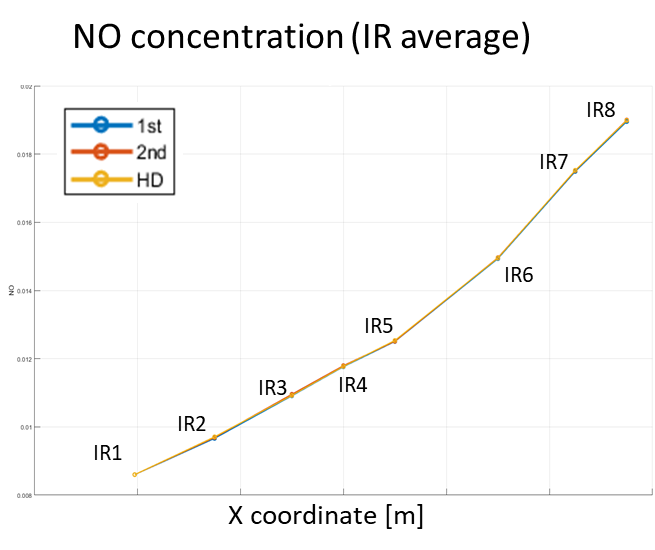
Mesh-Grid convergence check.
5. Summary of CFD comparison
Thanks to the HEG test campaign data, it was possible to enable the CFD results presented.
Even if the computational domain is not suitable to predict a proper in-chamber pressure distribution due to computational limitations, the averaged values as a result of line-of-sight integration (as long as cross-section average), exhibited a very good agreement with the experimental results.
This matching enables the adoption of the scheme (reduced Jachimowski [7]) along with the combustion model (Eddy Dissipation Concept) for this kind of investigation..
The presented comparison is intended only for the main species concentration obtained by the combustion (nitrogen monoxide and water). It shall be improved if more information about combustion gases content will be accessible.
The presented CFD results seemed not to be affected by the model and mesh setup.
6. Conclusion
The hydrogen/air supersonic combustion process was analysed both from chemical kinetics and computational fluid dynamic points of view.
A 0D kinetic assessment in the operative conditions experienced in scramjet engines was carried out on literature available combustion mechanisms, and the best agreement with experimental shock ignition delay times measurements was achieved with Z22 [10]. Indeed, this scheme was specially conceived for capturing the complex reaction paths followed by the radical pools in the crossover region at moderate pressure and intermediate temperatures.
In any case, fully-3D CFD simulations confirmed that kinetic schemes due to Zettervall and Fureby [10] and the reduced version of the Jachimowski mechanism [6-7] are quite good for pressure predictions when hydrogen/air combustion is under investigation.
Acknowledgements
The H2020 STRATOFLY Project has received funding from the European Union’s Horizon 2020 research and innovation programme under Grant Agreement No. 769246.
A special thanks to Jan Martinez Schramm, from DLR, for his special cooperation in setting up experimental measurements (TDLAS during DLR-HEG test campaign) and undeniable contribution to post-processing data.
References
[1] D. Cecere, A. Ingenito, E. Giacomazzi, L. Romagnosi, and C. Bruno, “Hydrogen/air supersonic combustion for future hypersonic vehicles,” International Journal of Hydrogen Energy, vol. 30, pp. 1-16, 2011. View Article
[2] Gerlinger, K. Nold, and M. Aigner, “Investigation of Hydrogen-Air Reaction Mechanisms,” Propulsion Conference & Exhibit, Hartford, U.S.A., 2008. View Article
[3] Olm, I. G. Zsély, R. Pálvölgyi, T. Varga, T. Nagy, H. J. Curran, and T. Turányi, “Comparison of the performance of several recent hydrogen combustion mechanisms,” Combustion and Flame, vol. 161, pp, 2219-2234, 2014. View Article
[4] Hu, L. Pan, Z. Gao, X. Lu, X. Meng, Z. Huang, “Shock tube study on ignition delay of hydrogen and evaluation of various kinetic models,” International Journal of Hydrogen Energy, 2016. View Article
[5] J. Jachimowski, “An Analytical Study of the Hydrogen-Air Reaction Mechanism With Application to Scramjet Combustion,” NASA Technical Paper 2791, 1988.
[6] B. Star, “Numerical Simulation of Scramjet Combustion in a Shock Tunnel”, Ph.D. Dissertation, Dept. Aerospace Engineering North Carolina State University.
[7] Battista, L. Cutrone, G. Ranuzzi, “Supersonic Combustion Models Application in Advanced Propulsion Concept,” 15th AIAA International Space Planes and Hypersonic Systems and Technology Conference, Dayton, Ohio, U.S.A. 2008. View Article
[8] Frassoldati, T. Faravalli, E. Ranzi, “A wide range modeling study of NOx formation and nitrogen chemistry in hydrogen combustion,” International Journal of Hydrogen Energy, vol. 31, pp 2310-2328, 2006. View Article
[9] Kéromnès , W. K. Metcalfe, K. A. Heufer, N. Donohoe, C. J. Sung, J. Herzler, C. Naumann, P. Griebel, O. Mathieu, M. C. Kreijci, E. L. Petersen, W. J. Pitz, H. J. Curran, and A. K. Das, “An Experimental and Detailed Chemical Kinetic Modelling Study of Hydrogen and Syngas Mixtures at Elevated Pressures,” Combustion and Flame, 2013. View Article
[10] N. Zettervall, and C. Fureby, “A Computational Study of Ramjet, Scramjet and Dual Mode Ramjet/Scramjet Combustion in a Combustor with a Cavity Flameholder,” Proceedings of AIAA Aerospace Science Meeting Kissimmee, 8-12 January (2018), Florida (U.S.A.). View Article
[11] Y. Li, C.W. Zhou, K.P. Somers, K. Zhang, H.J. Curran, “The Oxidation of 2-Butene: A High-Pressure Ignition Delay, Kinetic Modeling Study and Reactivity Comparison with Isobutene and 1-Butene.” Proceedings of the Combustion Institute, vol. 36, no. 1, pp 403–411, 2017. View Article
[12] C.-W. Zhou, Y. Li, E. O'Connor, K.P. Somers, S. Thion, C. Keesee, O. Mathieu, E.L. Petersen, T. A. DeVerter, M. A. Oehlschlaeger, G. Kukkadapu, C.-J. Sung, M. Alrefae, F. Khaled, A. Farooq, P. Dirrenberger, P.-A. Glaude, F. Battin-Leclerc, J. Santner, Y. Ju, T. Held, F. M. Haas, F.L. Dryer, and H. J. Curran, “A Comprehensive experimental and modeling study of isobutene oxidation,” Combustion and Flame, vol. 167, pp. 353–379, 2016. View Article
[13] U. Burke, W.K. Metcalfe, S.M. Burke, K.A. Heufer, P. Dagaut, H.J. Curran, “A Detailed Chemical Kinetic Modeling, Ignition Delay time and Jet-Stirred Reactor Study of Methanol Oxidation.” Combustion and Flame, vol.165, pp 125–136, 2016. View Article
[14] G. P. Smith, D M, Golden, M. Frenklach, N. W. Moriarty, B. Eiteneer, M. Goldenberg, C.T. Bowman, R.K. Hanson, S. Song, W.C. Gardiner, V.V. Lissianski Jr, Z. Qin, GRI-Mech 3.0 [Online]: available at http://www.me.berkeley.edu/gri_mech/, 1999.
[15] M. Slack and A. Grillo, “Investigation of Hydrogen-Air Ignition Sensitized by Nitric Oxide and by Nitrogen Dioxide,” NASA Contractor Report, CR-2896, 1977.
[16] J. Warnatz, “Concentration-, Pressure-, Temperature-Dependence of the Flame Velocity in Hydrogen-Oxygen-Nitrogen Mixtures,”, Combustion Science and Technology, vol. 26, no. 5-6, 1981. View Article
[17] B.E. Milton and J. C. Keck, “Laminar Burning Velocities in Stiochiometric Hydrogen and Hydrogen-Hydrocarbon Gas Mixtures, Combustion and Flame, vol. 58, pp. 13-22, 1984. View Article
[18] Y.B. Zel'dovič, “The Oxidation of Nitrogen in Combustion Explosions”, Acta Physicochimica 21, 577–628, (1946).
[19] E. Ranzi, A. Frassoldati. S. Granata, T. Faravelli. Ind Eng Chem Res, vol. 44, no. 14, pp 5170-5183, 2005. View Article
[20] B. Ruscic, A.F. Wagner, L.B. Harding, R.L. Asher, D. Feller, D.A. Dixon et al., J Phys Chem A, vol. 106, pp 2727, 2002. View Article
[21] W.K. Metcalfe, S.M. Burke, S.S. Ahmed, H.J. Curran, “A hierarchical and comparative kinetic modeling study of C1− C2 hydrocarbon and oxygenated fuels,” Int. J. Chem. Kinet., vol. 45, pp 638-675, 2013. View Article
[22] G. Bagheri, E. Ranzi, M. Pelucchi, A. Parente, A. Frassoldati, T. Faravelli, “Comprehensive kinetic study of combustion technologies for low environmental impact: MILD and OXY-fuel combustion of methane,” Combustion and Flame, vol. 212, pp 142-155, 2020. View Article
[23] E. Ranzi, A. Frassoldati, A. Stagni, M. Pelucchi, A. Cuoci, and T. Faravelli, “Reduced kinetic schemes of complex reaction systems: Fossil and biomass-derived transportation fuels,” International Journal of Chemical Kinetics, vol. 46, no. 9, pp 512-542, 2014. View Article
[24] M. Ó Conaire, H-J. Curran, J. M. Simmie, W. J. Pitz, C K. A Westbrook, “Comprehensive Modeling Study of Hydrogen Oxidation,” Intersience.Wiley.com, 2004. View Article
[25] A. Larsson, N. Zettervall, T. Hurtig, E. J. K. Nilsson, A. Ehn, P. Petersson, M. Alden, J. Larfeldt. & C. Fureby, “Skeletal Methane-Air Reaction Mechanism for Large Eddy Simulation of Turbulent Microwave-Assisted Combustion,” Energy Fuels, vol. 31, pp 1904, 2017. View Article
[26] V. A. Alekseev, M. Christensen, & A. A. Konnov, “The Effect of Temperature on the Adiabatic Burning Velocities of Diluted Hydrogen Flames: A Kinetic Study using an Updated Mechanism,” Combustion and Flame, vol. 162, pp 1884, 2015. View Article
[27] D. Goodwin, H. K. Moffat, and R. L. Speth, “Cantera: An Object-oriented Software Toolkit for Chemical Kinetics, Thermodynamics, and Transport Processes,” (Version 2.6) [Online]. Available: View Article
[28] R.R. Craig, “A Shock Tube Study of the Ignition Delay of Hydrogen-Air Mixtures Near the Second Explosion Limit,” Technical Report AFAPL-TR-66-74, 1966.
[29] B.L. Wang, H. Olivier and H. Grönig, “Ignition of schock-heated H2-air-steam mixtures,” Combustion and Flame, vol. 133, pp 93-106, 2003. View Article
[30] D.J. Beerer, V.G. McDonell, “Autoignition of Hydrogen and Air Inside a Continuous Flow Reactor with Application to Lean Premixed Combustion,” Journal of Engineering for Gas Turbines and Power, vol. 130, 2008. View Article
[31] K. Hannemann, J. M. Schramm, S. Karl, S. J. Laurence, “Free Flight Testing of a Scramjet Engine in a Large Scale Shock Tunnel”, AIAA 2015-3608, Session: Propulsion Systems V, Jul 2015. View Article