Volume 9 - Year 2022 - Pages 43-48
DOI: 10.11159/jffhmt.2022.006
CFD Approach to the Influence of Particle Size on Erosive Wear in Coal Riser Pipes
Paul T Ogunlela1*, Donald Giddings1, Chris Bennett2, Stefan Born3, Margot Klaassen3, Isaac Gennissen3, Richard Farnish4
1FLUTE Research Group, Faculty of Engineering, University of Nottingham
Nottingham, NG7 2RD United Kingdom
22G2TRC Research Group, Faculty of Engineering, University of Nottingham
Nottingham, NG7 2RD, United Kingdom
3Research and Development, Engineering Department, Tata Steel Europe
Ijmuiden, North Holland, Netherlands
4The Wolfson Centre for Bulk Solids Handling Technology, Faculty of Engineering & Science,
University of Greenwich, Chatham, Kent, ME4 4TB, United Kingdom
*Paul.Ogunlela@nottingham.ac.uk
Abstract - Pneumatic conveying of finely pulverised coal particles is an important process in the steelmaking industry, used to transport coal to the blast furnace. Erosive wear caused by high velocity particles impacting on the inner wall surfaces of pneumatic conveying riser pipes causes a severe problem in the steel-making industry. Continuous erosion left unmaintained eventually leads to pipe punctures. This paper aims to help minimise the erosive wear in industrial risers by investigating the effects of different particle sizes on the wear rates in industrial coal conveying ducts to control the grind size in industrial gas-solid flow processes and optimise reduced wear. Computational fluid dynamics (CFD) simulations and 4 semi empirical erosion models were used to analyse these effects, with an Eulerian-Lagrangian technique to model the multiphase gas-solid flow in the riser. The continuous phase (air) was modelled by solving Eulerian Reynolds-averaged Navier Stokes equations and the discrete phase (coal) was modelled using the Lagrangian discrete phase model (DPM) approach. The particle sizes investigated ranged from 1 to 1000 µm. The results showed the curves for each erosion model representing the changes in erosive wear with an increase in particle size for each erosion model. Every model showed similar curve shapes but varied in degree of wear rates. The curves of each model showed a steady increase in wear between particle diameters of 1 and 150 µm, followed by a sharp increase in wear at 200 µm, with the maximum erosion rates recorded between 300 and 350 µm. Subsequently, the wear rates began to drop, with a steady decrease in wear with particle diameters between 600 and 1000 µm. The behaviour of the curves was characterised by analysing the Stokes’ number and kinetic energy at each particle size. It was concluded that the sharp increase at 200 µm occurred, due to the number of particles (which possess sufficient kinetic energy) and the number density escaping the continuous phase and impacting the riser walls. Larger particles may have possessed greater individual kinetic energies; however, the fewer particles tend to impact the riser walls at higher particles sizes due to significantly lower number densities, resulting in a decrease in wear rates.
Keywords: Particle, wear, size, erosive, model, rate, impact, pipe.
© Copyright 2022 Authors - This is an Open Access article published under the Creative Commons Attribution License terms Creative Commons Attribution License terms. Unrestricted use, distribution, and reproduction in any medium are permitted, provided the original work is properly cited.
Date Received: 2022-05-10
Date Accepted: 2022-05-20
Date Published: 2022-06-06
1. Introduction
Gas-solid erosion is caused by the repetitive impact of abrasive solid particles suspended in a gas phase which is usually air, on a surface material (Zhang et al., 2017). Essentially it is a solid wall abstraction process due to the material experiencing a loss of mass following continuous impacts. It has been recognised in countless literature sources, that it is a difficult obstacle to overcome and exists in multitudes of engineering processes, especially involving any kind of pipeline process that transports solid particles such as gas lift systems, pneumatic conveying processes, valves, hydraulic turbine, compressor pumps, etc. The material erosion rate in gas-solid erosion is based on an aggregation of parameters such as the impact angle and velocity of impact. A great number of interrelated parameters, however, seem to construct the basis for the most affecting parameters such as the properties of the erodent (Crocker, 2014). In order to fully grasp the gas-solid erosive wear phenomena, we need to clearly analyse and clarify the fundamentally intertwined erosion mechanism. The result could be the total prevention, or at least the significant minimisation of erosive wear in gas-solid and other multiphase flow processes.
A study carried out by Lynn et al. (1991) observed the particle size effect on P110 steel in slurry pot tests. When looking at the kinetic energy of the particles, they concluded that the erosive wear rate is proportional to the bulk kinetic energy of particles after carrying out direct impingement tests. More recently, Jafari & Hattani (2019) in their work have tried to correlate the erosion rate wear with various parameters such as impact angle, impact velocity as well as the general shape and size of solid particles using discrete element modelling. There is a consensus that the wear rate rises, the greater the size of the solid particles. Furthermore, researchers such as Fourvy & Merhej (2013), use an equation to show a power-law relationship between the erosion rate and the mean size of solid particles; however, the size ranges in which these equations are valid are too narrow to be considered practical for industrial use.
This study aims to investigate the effects of particle size on erosive wear during the pneumatic transport of coal particles using air in an industrial scale riser pipe. A computational fluid dynamic (CFD) approach is taken, coupled with the use of existing empirical erosive wear models. Although there is no existing erosive wear model that can accurately predict wear in any given scenario, similarities in the results from multiple existing models can help provide a more accurate and clear view of the effect of a much wider range of particle sizes on erosive wear. Research has highlighted four distinct and widely accepted erosive wear models that will be used in this study to investigate the effects of particle size on erosive wear in industrial coal riser pipes.
The Generic Model
The generic model is the default erosion fluid dynamics model embedded in ANSYS FLUENT developed by Hamed & Tabakoff (2006) and is mainly based on the particle’s size, impact angle and impact velocity. The Generic model is shown in Equation 1.1 below.

Where; m𝑝 is the mass flow rate of the particles, 𝑓 (∝) is the impact angle function, 𝐶(𝑑𝑝) is a concentration function in terms of the particle diameter, vp is the particle impact velocity and n is the velocity exponent.
The Finnie Model
The Finnie model was developed by Finnie (1960) aimed to predict the wear caused by particles impacting a surface. This model takes impact angle and velocity as the underlying factors that influence wear and is shown in Equation 1.2 below.

Where, E is mass of eroded material, V1n is the velocity of the impacting particle, and f(γ1) is the following function of the impact angle:

The value of n is often contested between different experiments, but is usually chosen to be around 2 when considering metals (Brown, 2006). The Finnie model is more suited for ductile materials where there are dominant changes in impact angles and velocity.
The Oka Model
The Oka model is a three-part equation developed by Oka & Yoshida (2005). This model aims to provide a more realistic correlation by including the effect of wall material hardness and is shown below.



Where, E(∝) is the erosion rate at a specified impact angle and g(∝) is a function of the impact angle and E90 is the erosion rate at a 90o impact angle.
The Mclaury Model
The McLaury erosion model was developed to predict the erosion rate of solid particles in water; it has been primarily used in slurry flows and is shown in the set of equations below (Mclaury et al., 1996).


Where, E is the erosion rate, f(γ) is the function of the impact angle, F is an empirical constant, Bh is the Brinell’s hardness of the material, V is the particle impact velocity, k is the material exponent (-0.59 for carbon steel), γ is the impact angle and γlim is the transition angle. Finally, b, c, n, w, x, y and z are all experimentally derived constants.
2. Methodology
This study aims to investigate the effects of particle size on maximum erosive wear in a typical industrial coal riser pipe for steelmaking industries. Solidworks 18 was used to generate a 3D model of a typical riser pipe used for pneumatic transport of fine coal particles. A diameter of 1.2m, a thickness of 10mm and a total length of 36m of pipe geometry, which is more than enough for a fully developed flow to travel through each of the pipe bends. The material assigned to the pipe geometry was mild steel with a density of 7700kg/m3. The dimensions, materials and properties of the riser were obtained from real life plant data. A labelled diagram of the pipe geometry is outlined In Figure 2.1a below. The 3D model of the riser pipe was uploaded into ANSYS FLUENT 19.1 for meshing and multiphase flow simulations.
Figure 3.1b below shows the mesh constructed for multiphase flow simulation in the test bend. A fine adaptive triangular mesh with an element sizing of 0.1m and the mesh resolution set to 7.
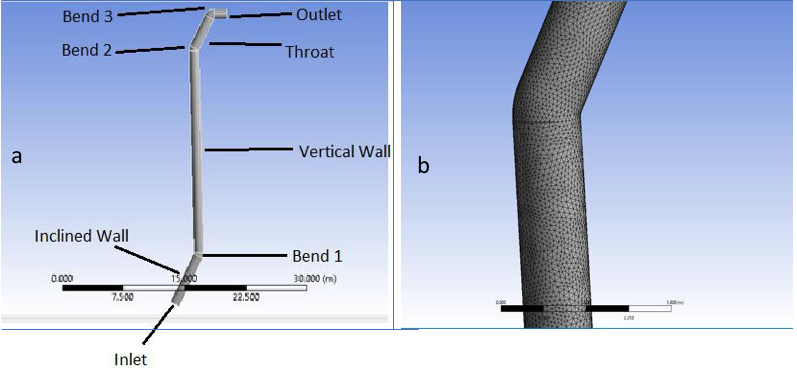
An Eulerian-Lagrangian approach was used as the multiphase modelling method to describe the flow within the pipe. The Eulerian model describes the flow of the continuous phase using Reynolds- averaged Navier Stokes (RANS) equations and the Lagrangian approach tracks the behaviour of the secondary phase using discrete phase methods (DPM). The k-epsilon realizable model with scalable wall functions for near wall treatments was used to close the combined RANS equations for the multiphase model; by describing the turbulence within the system. Two-way coupling was also included in the simulation, to consider the exchange of momentum and energy between the discrete and continuous phase. The discrete phase model was turned on and the DPM erosion rate model which includes the Generic, Finnie, Oka and Mclaury models were added to the simulation to analyse the wear rates caused by the particles impacting the pipe’s surface. Details of the particle injection are shown in Table 2.1 below. A single particle size was selected, and flow simulations were repeated for particle sizes between 1 – 850µm.
Table 2.1: Particle injection details for multiphase flow simulations
Injection Type |
Surface |
Diameter Distribution |
Uniform |
Particle Diameter (µm) |
1 – 850 |
Total Flow Rate (kg/s) |
12.5 |
Velocity Magnitude (m/s) |
1 |
The boundary conditions were set as an inlet velocity of 20 m/s for the continuous phase and a pressure outlet of 0 Pag. The no-slip condition was set at the wall. The injected particles were set to reflect off the walls and rebound as many times as possible.
Finally, the solution was initialized using hybrid initialization. The transient simulations were run till a convergence residual of 10-3 and all simulations reached convergence between 350 – 520 iterations.
3. Results & Discussion
The The effect of particle size can be investigated accurately by analyzing the similarities between each of the erosion models. This is done by analyzing how each erosion model predicts the change in erosive wear rate as the particle size is increased. The range of particle sizes investigated was between 1 and 850µm and, It is important to note that the particle shape was not taken into consideration and all particles were modelled to be perfectly spherical. Figure 4.1 shows the plots of particle size against maximum erosion rate for each erosion model.
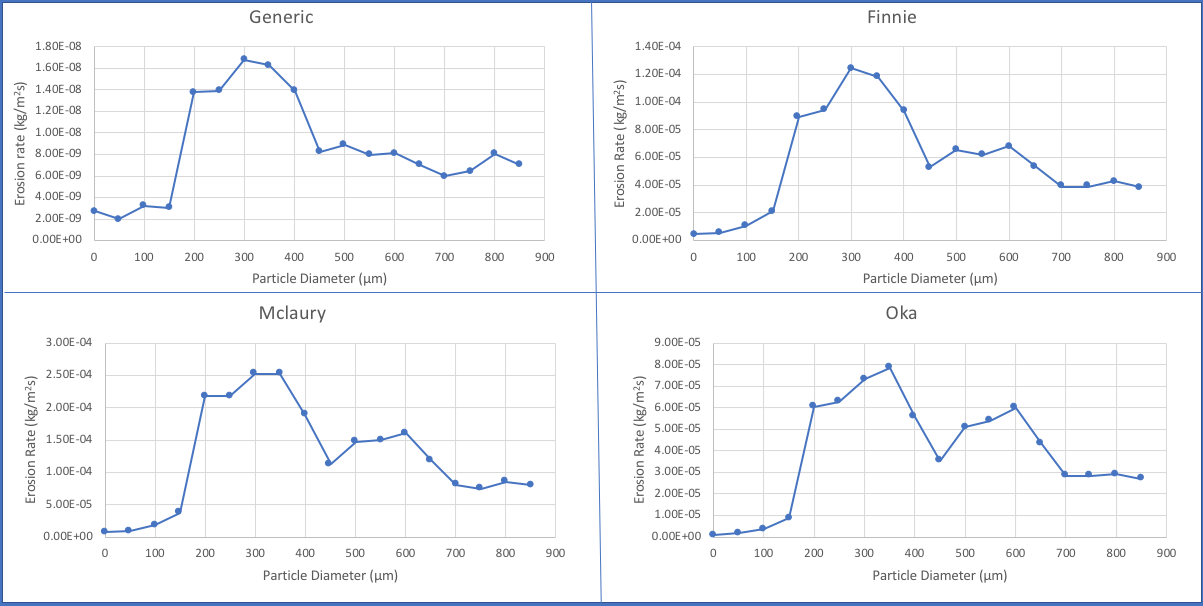
The similarities between the curves of each erosion model can be separated into four distinct phases. The first phase shows a relatively small and steady increase in the erosive wear between 1 – 150 µm followed by the second phase which shows the sharp increase in the erosive wear rate between 150 and 200 µm. The third phase shows a surprisingly sharp drop in wear between 350 and 450 µm with a subsequently small increase in wear rate at 500 µm before remaining relatively constant until 600 µm. The fourth and final phase shows another decrease in erosive wear rate between 600 and 700 µm followed by a relatively constant wear rate between 700 and 850 µm. It can be argued that the fourth phase is not present for the generic model; however, the generic model predicts erosive wear rates to an order of magnitude that is ten thousand times less than the other three erosion model which makes it more difficult to notice.
The linear behaviour of the curves in phase one follow the expected results, in that the erosive wear rate would be greater if the particle size is increased. Larger particles possess more kinetic energy and would subsequently have a greater impact when coming into contact with the pipe walls. However, the sudden increase in wear at 200 µm suggests that more complex mechanisms are taking place within the system. Abouel-Kasem (2011) investigated the effects of particle size at similar size ranges on erosive wear in various types of steels using direct impingement experiments and noticed similar behaviour at 200 µm. It was concluded by Abouel-Kasem (2011) that 200 µm could be described as the critical transitional size, where the particles switch from indentation to a more aggressive wear mechanism known as micro-ploughing. However, only the Oka model contains variables that can describe this phenomenon; yet all models were still able to accurately predict the sharp increase in wear at that specific particle size. Hence, this suggests that the sharp increase in erosive wear at 200 µm is largely due to the particle behaviour within the continuous phase rather than particle-wall interactions although, micro ploughing could have second order effects.
The behaviour of the particles within the continuous gas phase can be investigated further by analyzing the Stokes’ number of each particle size, which is a dimensionless number that characterizes the suspension of the particles as they travel within the continuous phase. The Stokes number of each particle size was calculated using Equation 4.1 to analyze the behaviour of the particles within the continuous phase, provided by Sehgal (2012).

Where, 𝑆𝑡 is the Stokes number, 𝜌𝑝 is the particle density (1600kg/m3), 𝑈𝑓 is the fluid velocity (20m/s), 𝑑𝑝 is the particle diameter in m, μf is the fluid viscosity (0. 000018Pa.s), and D is characteristic length which was set to be the diameter of the riser pipe as 1.2m.
Nguyen et al. (2016) investigated the effect of particle size on erosive wear, caused by a water-sand slurry and investigated the behaviour of the sand particles within the water flow using the Stokes’ number. Nguyen et al. (2016) stated that particle sizes with a Stokes’ number less than 1 follow the path of the continuous phase closely, while particles with a Stokes’ number greater than one still follows the path of the continuous phase, but particles begin to escape and fall out of the continuous phase as the Stokes’ number increases. Hence, smaller particles travelling through the riser pipe would change their trajectories according to the flow of the gas as they approach a bend, while larger particles are more likely to escape the trajectory of the gas when approaching a bend. This implies that larger particles are more likely to impact the walls of the riser pipe at the bend than smaller particles with a Stokes’ number < 1. Figure 3.2 shows the change in Stokes number with an increase in particle size. The curve shows that the Stokes number reaches 1 at around 130 µm hence, at this size some particles begin to fall out of the continuous phase. This is because the carrier fluid becomes unable to entrain all the particles in a continuous flow stream. This suggests that; at 200 µm a substantial number of particles fall out of the continuous gas stream and they possess sufficient kinetic energy to impact the bend walls and cause severe wear. This can be proven further by analysing the number density and kinetic energy of the particle at various sizes just before and after striking the area of maximum erosive wear in the riser pipe.
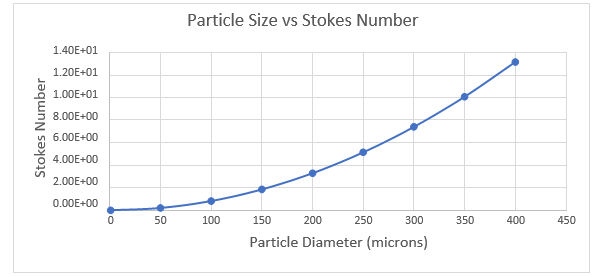
The number density was calculated using the maximum discrete phase concentration which is measured in FLUENT as the mass of particles per cubic meter of air as it flows through the riser pipe. Equation 3.2 below shows how the number density at each particle size was calculated, which represents the number of particles impacting the riser pipe at the area of maximum erosive wear. It was assumed that the region with the maximum discrete phase concentration corresponded with area of maximum wear.

Where, 𝐶𝑝 is the maximum discrete phase mass concentration of coal in a volumetric unit of air, Qg is the volumetric flowrate of the gas in m3 /s, 𝑑𝑝 is the particle diameter in m and 𝜌𝑝 is the particle density in kg/m3.
The maximum kinetic energy at each particle size was subsequently calculated by multiplying the number density by the maximum kinetic energy of a single particle traveling through the riser pipe. This is mathematically represented in Equation 4.3 below.

Where, 𝑢𝑝 is the maximum particle velocity, which was obtained from the transient flow simulations for each particle size and analysing the particle tracks in ANSYS FLUENT.
Figure 3.3 shows the relationship between the maximum kinetic energy of the bulk particles as the particle size increases. There is a significant increase in the maximum kinetic energy between 100 and 200 µm. This confirms that the particles that are 200 µm in size deviate from the gas phase, in relatively more substantial amounts and that they possess significantly higher kinetic energies than particles with Stokes’ numbers < 1, causing significantly more erosive wear at that critical size. The behaviour of the maximum kinetic energy with changes in particle size also correlates with the behaviour of the erosive wear rates in Figure 4.1. This suggests that even though larger particles > 300 µm which possess more kinetic energy in a single particle, fewer particles impact the pipe walls due to a significant reduction in number density, causing a reduction in erosive wear. Further research which analyses the particle trajectories near the pipe bend walls is required to confirm this phenomenon.
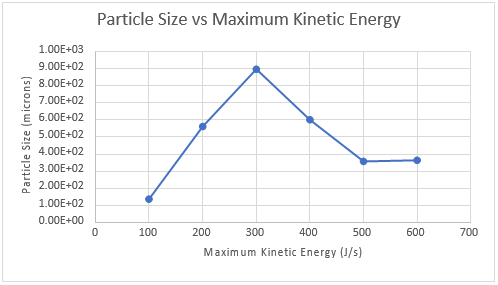
5. Conclusion
The conclusions of this study have been listed accordingly below:
- There were very clear similarities between the curves of all four erosive wear models when predicting the effects of particle size on the erosion rate, even though the degree of erosive wear varied significantly in all models.
- The sharp increase in erosive wear rate at the critical size of 200 µm was caused by a significantly larger number of particles that also possessed a substantially higher kinetic energy and escaped the trajectory of the gas phase and impacted the bend walls more often. This subsequently led to an accelerated erosive wear rate in comparison to smaller particle sizes. It is worth highlighting that this phenomenon did not occur due to a change in wear mechanism. This is because, the variables for those mechanisms are only present in the Oka model, yet all four model were still able to predict the outcome.
- Particles larger than 300 µm still possess a higher kinetic energy individually and escape the trajectory of the gas phase. However, due to a significantly lower number density after 300 µm, the particles impact the pipe bends less frequently and subsequently cause less severe erosion.
- Further research such as, the investigation of the behaviour of the particle trajectories near the region of maximum erosion, is required to develop an accurate equation or model that can predict the effect of particle size on erosive wear over a wide range of particle sizes.
- The findings of this study can help select a suitable particle size to prevent excessive wear in industrial pneumatic transport processes.
Acknowledgements
This project is part of the EPSRC Centre for Doctoral Training in Carbon Capture and Storage and Cleaner Fossil Energy with reference EP/L016362/1.
References
[1] A. Hamed and W. Tabakoff, “Erosion and Deposition in Turbomachinery.” Journal of Propulsion and Power, Vol. 22, No. 2, pp. 350-360, 2006. View Article
[2] Abouel-Kasem, A., 2010. Particle Size Effects on Slurry Erosion of 5117 steels. Journal of Tribology, 133(1). View Article
[3] McLaury, B.S., Sjirazi, S.A., Shadley, J.R. and Rybicki, E.F. . "Modelling Erosion in Chokes". Proceeding of the ASME Fluids Eng. Summer Meeting. San Diego, California. 1996.
[4] Crocker, L. 2014. CFD Modelling of Erosive Wear. National Physical Laboratory, 146(1), pp.4 – 15
[5] Finnie, I. 1960. Erosion of surfaces by solid particles. Wear, 3(2), 87–103. View Article
[6] Fouvry, S. and Merhej, R., 2013. Introduction of a power law formulation to quantify the contact size effects on friction and wear responses of dry oscillating sliding contacts: Application to a chromium steel interface. Wear, 301(1-2), pp.34-46. View Article
[7] Jafari, A. and Abbasi Hattani, R., 2019. Investigation of parameters influencing erosive wear using DEM. Friction, 8(1), pp.136-150 View Article
[8] Lynn, R. S., Wong,K. K., and Clark, H. McI., 1991, “On the Particle Size Effect in Slurry Erosion,” Wear, 149, pp. 55–71. View Article
[9] Nguyen, V., Nguyen, Q., Zhang, Y., Lim, C. and Khoo, B., 2016. Effect of particle size on erosion characteristics. Wear, 348-349, pp.126-137. View Article
[10] Oka, Y.I. and Yoshida, T., 2005. “Practical Estimation of Erosion Damage Caused by Solid Particle Impact. Part 2: Mechanical Properties of Materials Directly Associated with Erosion Damage.” Wear, Vol. 259, pp. 102-109. View Article
[11] Zhang, H., Dong, X. and Chen, S., 2017. Solid particle erosion-wear behaviour of Cr3C2–NiCr coating on Ni-based superalloy. Advances in Mechanical Engineering, 9(3), pp.168-181. View Article