Volume 3 - Year 2016 - Pages 8-16
DOI: 10.11159/jffhmt.2016.002
Numerical Investigation of Heat Transfer Characteristics for the Annular Flow of Nanofluids using YPlus
Mohamed H. Shedid*, M. A. M. Hassan
Department of Mechanical Engineering, Faculty of Engineering at El- Mattaria,
Helwan University, Cairo, Egypt.
*mshedid@hotmail.com
Abstract - In the present work, two turbulence models namely, Spalart-Allmaras (S-A) and K-Ɛ models, are used to study numerically thermal behavior for annular flow of nanofluids. The nanofluids considered are alumina (Al2O3) and oxide titanium (TiO2) nanoparticles and water as the base fluid. To conduct the investigation, a grid is constructed that give y+ for all velocities below 1. The model is validated with Gnielinski correlation for the flow of pure water. Validated model was used for different concentration ratios of Al2O3 and TiO2 for different Peclet numbers. The results were compared with many correlations for convection of nanofluids flow and revealed better agreement with Spalart-Allmaras model rather than k-Ɛ model. Results of numerical simulations are compared and showed an enhancement of Nusslet number as Peclet number grows with increasing concentration ratio.
Keywords: Nanofluid; Heat Transfer; YPlus; Spalart-Allmara; Annular flow.
© Copyright 2016 Authors - This is an Open Access article published under the Creative Commons Attribution License terms Creative Commons Attribution License terms. Unrestricted use, distribution, and reproduction in any medium are permitted, provided the original work is properly cited.
Date Received: 2014-11-06
Date Accepted: 2015-12-27
Date Published: 2016-03-07
Nomenclature
- CP: Specific Heat, [J/kg.K]
- dh: Hydraulic diameter, [m]
- h: Heat transfer Coefficient, [W/m2.K]
- k: Thermal conductivity, [W/m.K]
- Nu: Nusselt number, [-]
- Q: Heat flux, [W/m2]
- R: Radius, [m]
- Re: Reynolds number, [-]
- T: Temperature, [K]
Greek Symbols
- φ: Nanoparticle Volumetric Concentration, [%]
- µ: Dynamic Viscosity, [kg/m.s]
- ρ: Density, [kg/m3]
Subscripts
- bf: Base fluid
- i: Inlet, inner
- nf: Nanofluid
- o: Outlet, outer
- p: Particle
- w: Wall
1. Introduction
Heat transfer by convection is very important for many industrial heating and cooling applications. The heat convection can passively be enhanced by changing flow geometry, boundary conditions or by enhancing fluid thermophysical properties. With presenting the concept of nanofluid (Choi, 1995), it attracted the attention of many researchers who were interested in increasing the heat transfer coefficient of liquids in many industrial applications.
They show that use of nanofluids does enhance heat transfer coefficient for heat transfer applications. Such enhancement mainly depends upon factors such as the shape of particles, the dimensions of particles, the volume fractions of particles in the suspensions, and the thermal properties of particle materials.
Pak et al., 1998; Qiang et al., 2002; Xuan et al., 2003; Yang et al., 2005; Heris et al., 2007; Nguyena et al., 2007; VELAGAPUDI et al., 2008; Duangthongsuk et al., 2010; Nasiri et al., 2011; Murugesan et al., 2012; Darzi et al., 2013; Nield et al., 2014 have investigated the convective heat transfer of nanofluids. They show that use of nanofluids does enhance heat transfer coefficient for heat transfer applications. Such enhancement mainly depends upon factors such as the shape of particles, the dimensions of particles, the volume fractions of particles in the suspensions, and the thermal properties of particle materials.
Pak and Cho (Pak et al., 1998) published a correlation for the turbulent connective heat transfer for dilute dispersed fluids with submicron metallic oxide particles which is given by the following equation:
While Xuan and Li (Xuan et al., 2003) correlate Nusslet number for both laminar and turbulent flow as follows;
For laminar flow
For turbulent flow
(Qiang et al., 2002) highlighted that the conventional convective heat transfer correlation of the pure fluid is not applicable to the nanofluid and recommended the correlation for Nusslet number for convective heat transfer with nanofluid flows in Equations (2) and (3).
(VELAGAPUDI et al., 2008) recommend a new correlations (4) and (5) for water-Al2O3 and water-CuO when the flow is turbulent;
(Bianco et al., 2009) concluded that single phase and two phase methods revealed approximated results, especially in the case of using temperature dependent properties. Demir (Demir et al., 2011) mentioned that although the nanofluid is actually a two-phase fluid in nature, the results show that the nanofluid behaves more like a pure fluid than a liquid-solid mixture. Kumar (Kumar, 2011) after validation his numerical study with experimental works, he emphasized single phase approach does not predict heat transfer coefficient as accurately as in the turbulent regime.
(Maїga et al., 2005) studied forced convection flow of water-Al2O3 and ethylene glycol-Al2O3 nanofluids inside a uniformly heated tube at the wall and a system of parallel, coaxial for both laminar and turbulent flow. Numerical results showed better heat transfer enhancement. Finally, he recommends with a correlation (Maїga et al., 2006) to estimate Nu, Equation (6).
(Namburu et al., 2009) found in his numerical analysis for different nanofluids (CuO, Al2O3 and SiO2) in ethylene glycol and water mixture flowing through a circular tube under constant heat flux condition that Gnielinski correlation can be used in determining the Nusselt number with volume concentration up to 6%.
(Sharifi et al., 2012) examined the heat transfer coefficient for laminar flow inside tube subjected to constant heat flux with a concentration ratio from 1 to 10% by experimental and numerical methods. Good agreement was achieved between both methods and increase of heat transfer coefficient of about 60%.
Most numerical researches in convection heat transfer for nanofluids flow were in a cylindrical shape, (Rostamani et al., 2010) in rectangular duct, (Manca et al., 2012) in a triangular cross sectioned, (Bhattacharya et al., 2009) in rectangular micro-channel, (Pathipakka et al., 2010) in a circular tube fitted with helical twist inserts, (Vajjha et al., 2010) in flat tubes of the radiator and (Manca et al., 2012) in a ribbed channel and square cross section tubes. While others considered the natural convection for annular enclosures (Cianfrini et al., 2011; Abouali et al., 2012) and horizontal tube (Rashmi et al., 2011).
Turbulent flows are significantly affected by the existence of walls, where the areas that described by viscosity-affected areas have large gradients in the solution variables and accurate presentation of the near-wall region determines successful prediction of wall bounded turbulent flows. (Gerasimov, 2006) proposed in his seminar a strategy of computed wall y+ that dealing with near-wall turbulent flows using Fluent from ANSYS. This technique eliminates the traditional step of what is termed the grid independence test that requires a lot of time and computational effort. This strategy assists in selecting the most suitable near-wall treatment (wall functions or near-wall modeling) and the corresponding turbulence model based on the wall y+ (Salim et al., 2009).
The aim of this paper is to investigate numerically the application of YPlus strategy in heat transfer characteristics for Al2O3/water and TiO2/water flow through an annulus by applying two turbulence models of k-e and Spalart-Allmaras (S-A), evaluating its performance and assessment of the results with the proposed correlations.
2. Mathematical Formulation
2. 1. Problem Statement
The geometry of the annular channel has an outer diameter, inner diameter and length of 30, 10 and 1500 mm, respectively. This geometry is represented by a two-dimensional rectangular duct of height h (difference between outer and inner diameter) and length l. The tube has an appropriate length in order to obtain fully developed profiles (velocity and thermal) at the outlet section (L/Dh > 10), (Incropera et al., 2007). The outer wall is subjected to a constant wall temperature. The nanofluid enters the duct with uniform velocity and temperature and is affected only by the duct conditions. The nanofluid is incompressible and the flow is turbulent.
Also, it is assumed that the liquid and solid are in thermal equilibrium and they flow at same velocity. The resultant mixture may be considered as a conventional single phase fluid. The assumption of single phase for a nanofluid is validated to an extent by (Choi et al., 2001; Bianco et al., 2009; Demir et al., 2011; Kumar, 2011). Model is constructed and discretized using the strategy of computed wall y+ that is recommended when dealing with such flows as proposed by Gerasimov in using Fluent from ANSYS (Gerasimov, 2006). This strategy assists in selecting the most suitable near-wall treatment (wall functions or near-wall modeling) and the corresponding turbulence model based on the wall y+ (Salim et al., 2009).
The CFD commercial code, Fluent, is employed to solve the problem by means of finite volume method. Two turbulence model namely k-e and Spalart-Allmaras (S-A) are implemented. Spalart-Allmaras model is the most popular one-equation model. This model has been shown to give acceptable results for a wide variety of situations and is known for its stability. The numerical simulation results are also compared with correlations found by (Pak et al., 1998, Xuan et al., 2003, Maїga et al., 2006, and VELAGAPUDI et al., 2008). To save computational time, half of the domain is selected as the computational domain since the problem is Axi-symmetric (Fig. 1).
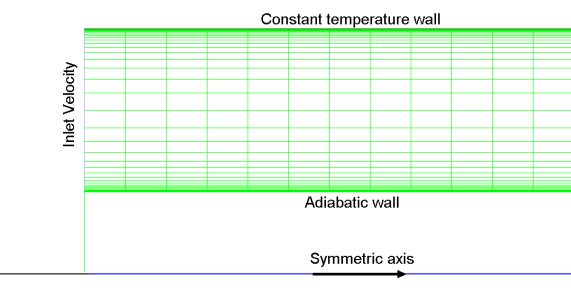
2. 2. Governing equations
The single-phase model, which has been used frequently for nanofluids, is also implemented to compare its predictions with the mixture model. The following equations represent the mathematical formulation of the single-phase model by (Choi et al., 2001; Bianco et al., 2009; Demir et al., 2011; Kumar, 2011):
Conservation of mass:

Momentum equation:

Energy equation:

The compression work and the viscous dissipation are assumed negligible in the energy equation; the source/sink terms Sm and Se represent the integrated effects of momentum and energy exchange with base fluid, as shown in the following, and they are equal to zero in the case of single-phase model.
The previous equations can be solved with the following boundary conditions;
At outer wall:

At inner wall
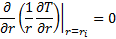
2. 3. Thermophysical Properties of Nanofluid
In the absence of experimental data for nanofluid densities, constant value temperature independent values, based on nanoparticle volume fraction, the following parameters were used as reported by (Pak et al., 1998; Maїga et al., 2004; Roy et al., 2004) and others.
Density:

Specific heat:

Effective thermal conductivity:
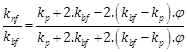
Viscosity
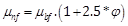
where, µbf, Cpnf, Cpbf, Cpp, rp, kbf, kp, and ϕ are basefluid viscosity, nanofluid heat capacity, base fluid heat capacity, nanoparticles heat capacity, nanoparticles density, thermal conductivity of base fluid, thermal conductivity of nanoparticles, and volume fraction of nanoparticles respectively.
The results of (Duangthongsuk et al., 2010) showed that use of the viscosity models to describe the Nusselt number of nanofluids gives different values compared with use of the measured data, by about 2-3%.
Specifications of nanoparticles used in this study are available in Table 1.
Table 1. Nanoparticles specifications.
Particle | Size (nm) | r (kg/m3) | k (W/m.K) | Cp (J/kg.K) |
Al2O3 | 25 | 3970 | 46 | 750 |
TiO2 | 10 | 3840 | 11.7 | 710 |
2. 4. Data Analysis
Heat transfer (q") between nanofluid and outer wall is obtained through the following equation:

Where DTLM is mean logarithmic temperature deference and is defined by:
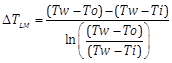
In order to calculate Reynolds number (Re), Nusselt number (Nu) and Peclet number (Pe) for annular tube, hydraulic diameter (dh) of the channel is used.
Where dh is hydraulic diameter and calculated by:



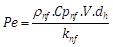
Where do, di is the outer and inner diameter of the annular passage. Knf, rnf, V and µnf are thermal conductivity, density, velocity, and viscosity of nanofluid respectively.
3. Results and Discussions
The results of this investigation obtained for distilled water for both k-Ɛ and S-A turbulence models were compared with famous equation of Gnielinski (Incropera et al., 2007) as shown in Fig. 2. It is clear to note that S-A model and k-Ɛ models exhibited good agreement with Gnielinski equation with a maximum deviation of 6% for a S-A model rather than k-Ɛ model which revealed 34% maximum error decreased with increasing Re to reach 2% in the end of the range (about Re = 56000).
The study were conducted for volumetric concentrations of 0.2, 0.5, 1.0 and 5% of Al2O3 and TiO2 nanoparticles. The convection heat transfer coefficient related to Al2O3/water nanofluid versus Peclet number is presented through Fig. 3. The Peclet number (Pe) is a comprehensive parameter to describe such effects, (Xuan et al., 2000).
Based on the results, for definite Peclet number, the convective heat transfer coefficient (h) of nanofluid is higher than that of base fluid. This enhancement considerably is dependent on the concentration of nanoparticles. For example at Peclet number about 21,800, the heat transfer coefficients are 6.4% and 36.1% greater than those of the base fluid when the nanoparticle concentration are 1.0 vol.% and 5.0 vol.% respectively.
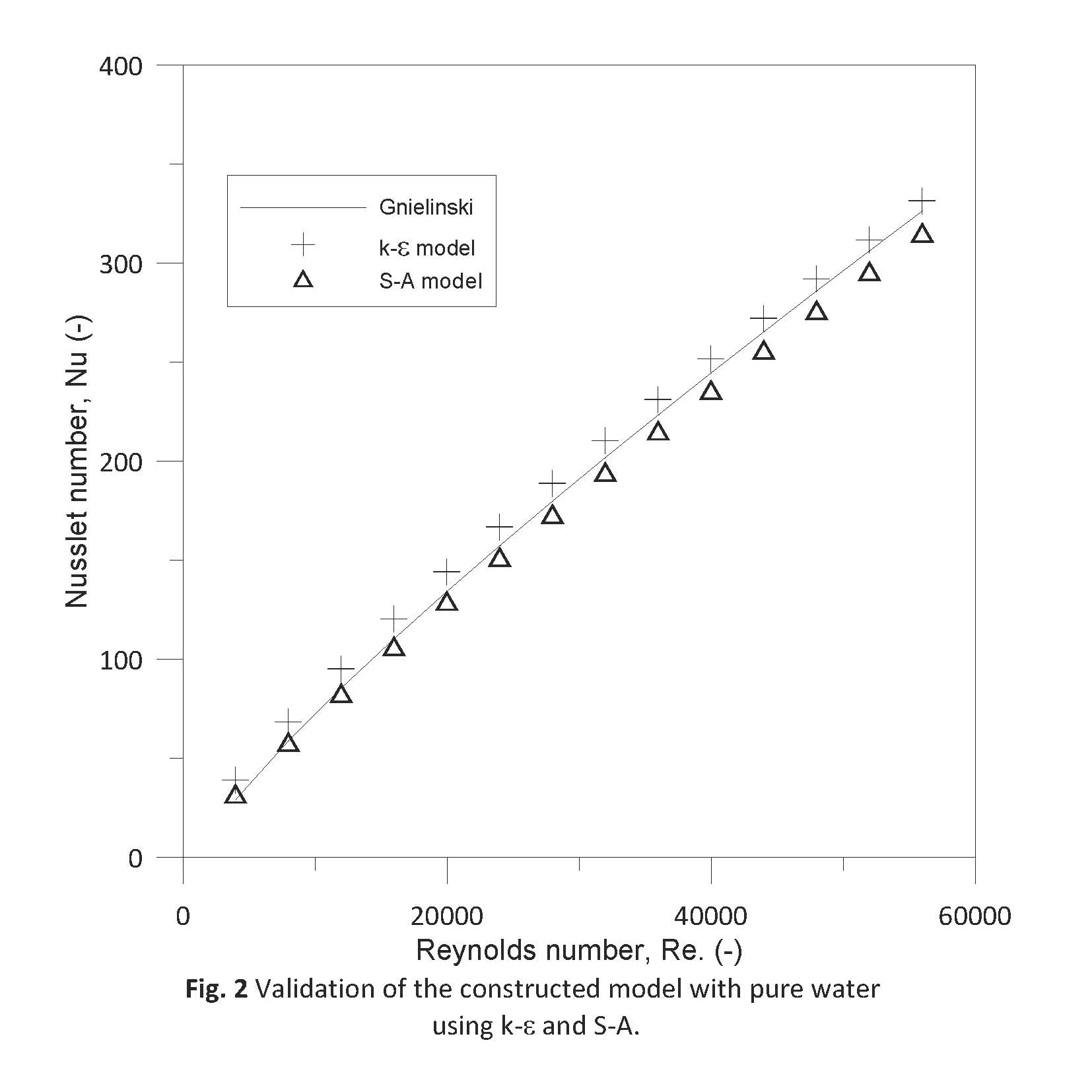
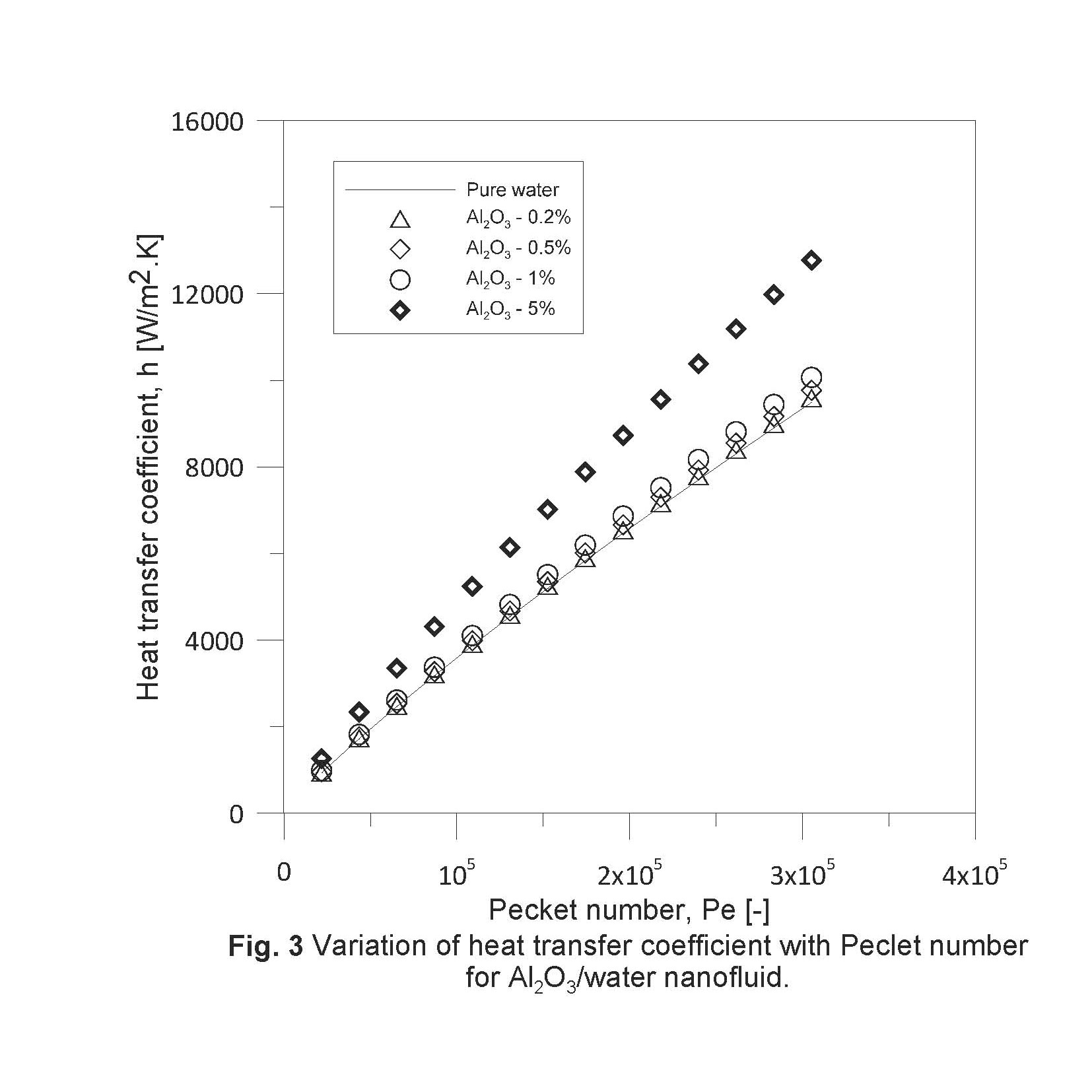
The results related to TiO2/water nanofluid are demonstrated through Fig. 4. The behavior of this nanofluid is similar to that of Al2O3/water. For example the enhancements of heat transfer coefficient for TiO2/water nanofluid at Peclet number about 21,800 are about 5.7% and 31.7% for nanoparticle concentrations of 1.0 vol. % and 5.0 vol. % respectively.
Figures 5 and 6 demonstrate the Nusselt number for Al2O3/water and TiO2/water nanofluids for different Peclet numbers. Both nanofluids show higher Nusselt number than those of the base fluids and enhancement increases with nanoparticle concentration. For example at Peclet number about 21,800, the enhancement of Nusselt number for Al2O3/water nanofluid with nanoparticles concentrations of 0.2, 0.5, 1.0 and 5.0% are 0.48%, 1.1%, 2.2% and 11.1% respectively.
For TiO2/water nanofluid at Peclet number about 21,800, the increment of Nusselt number for TiO2 nanoparticle concentrations of 0.1, 0.5, 1.0 and 1.5% are 0.43%, 1.0 %, 2.1% and 10.8 % respectively. It is be noted that for both nanofluids, there is no significant enhancement in Nusselt number for concentrations less than 0.2%, which noted by (Kumar, 2011). Moreover, the relative enhancement of heat transfer is remarkably not affected by change of Peclet number (Pe) as observed in Figs. 7 and 8.
Such improvement of heat transfer becomes more pronounced with the increase of the particle concentration. The reduction of the thermal boundary layer thickness due to the presence of particles and their random motion within the base fluid may have important contributions to such heat transfer improvement as well.
The heat transfer enhancement of nanofluids has been reported for annular channel. (Nasiri et al., 2011) presented the experimental results for Al2O3/water nanofluid with concentrations of 0.5% and 1% at Peclet number about 59,000 under turbulent regime in annular circular tube and showed the increments of Nusselt number were 6.2 % and 13.6% respectively. The corresponding results, for the present study, at the same Peclet number and nanoparticle concentrations are 1.1%, 2.3%.
In order to compare the performance of two employed nanofluids in this research, Nusselt number plotted for concentrations of 1.0 and 5.0% in Fig. 9. Based on the results of this figure, there is no significant difference between the Nusselt numbers of two employed nanofluids.
Validation of results with correlations found by (Pak et al., 1998; Xuan et al., 2003; Maїga et al., 2006; VELAGAPUDI et al., 2008) are presented for concentrations of 1.0 and 5.0% for both nanofluids. Validation with the correlations was also done with both results obtained by k-Ɛ and S-A turbulence models. Figures 10 and 11 are the validation for Al2O3/water for concentrations of 1.0 % and 5.0%, respectively. It is obvious that correlations of (Pak et al., 1998) and (VELAGAPUDI et al., 2008) are best fitted with results of S-A model with maximum error of 2%, while (Maїga et al., 2006) has overestimated results, (Xuan et al., 2003) has diversion that gets growing with increasing Re. Validation of (Pak et al., 1998) correlation also emphasized to give better results for comparison by (Bianco et al., 2011) for single phase fluid.
Similar trends can be found for TiO2/water validation Figs. 12 and 13. No correlation from (VELAGAPUDI et al., 2008) for TiO2/water nanofluid.
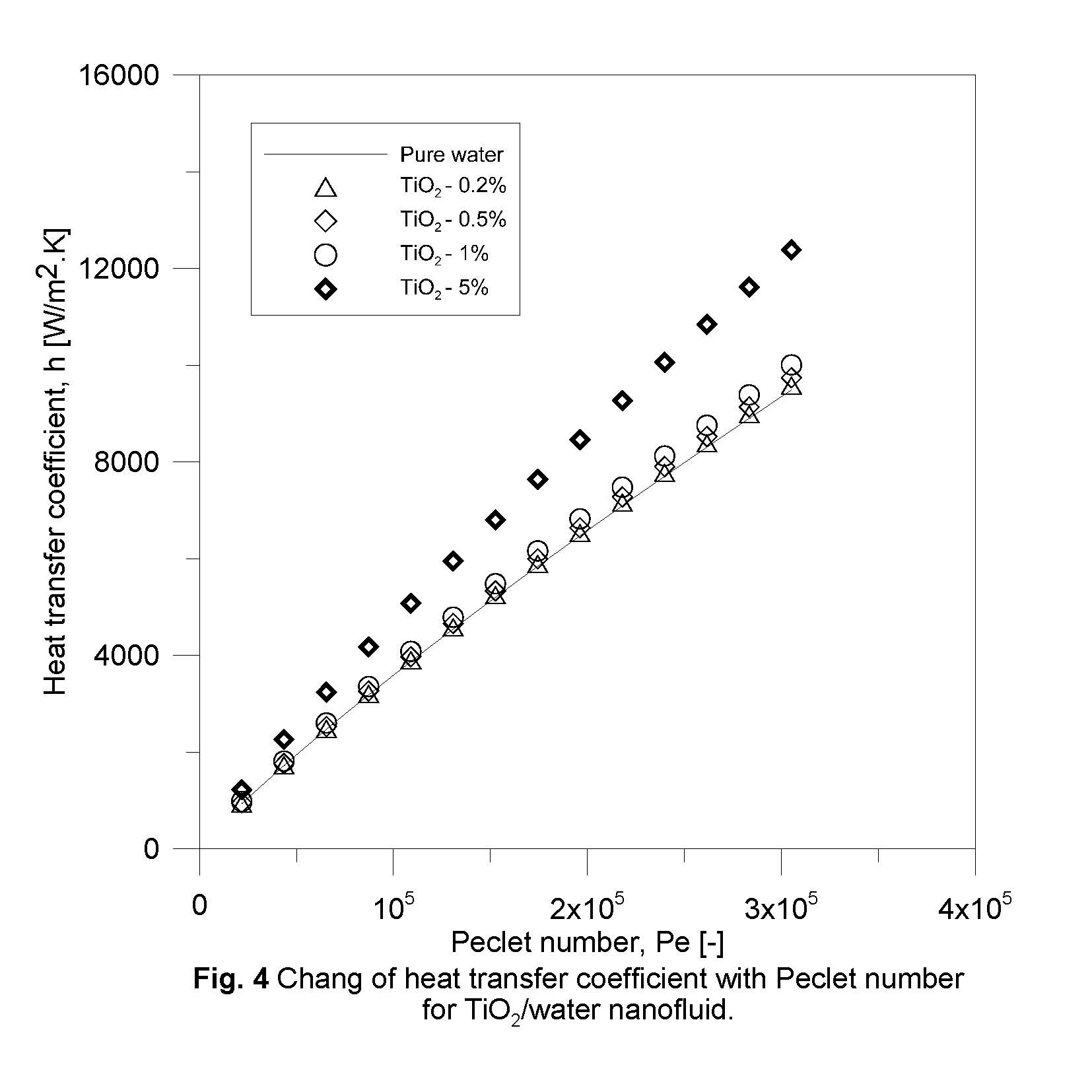
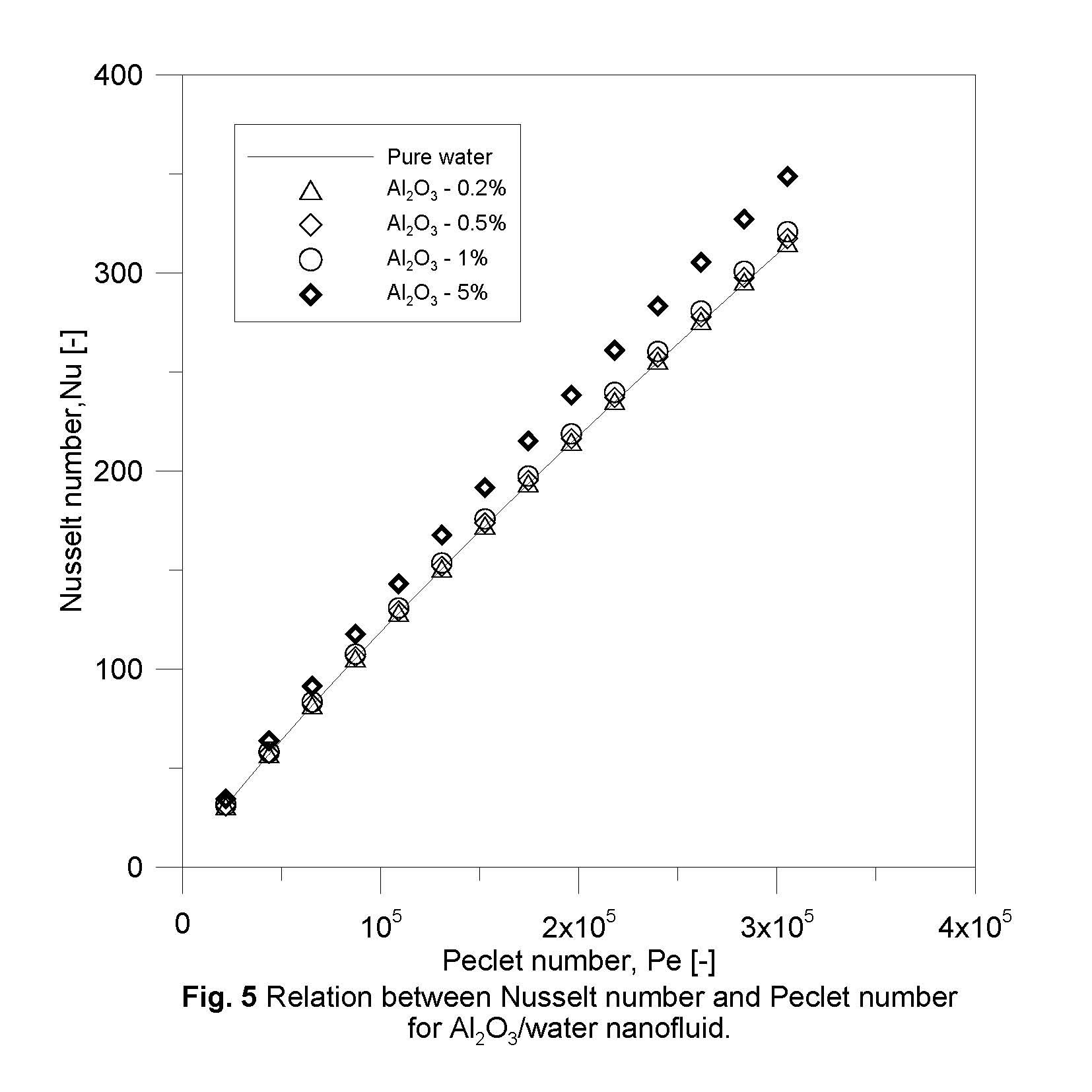

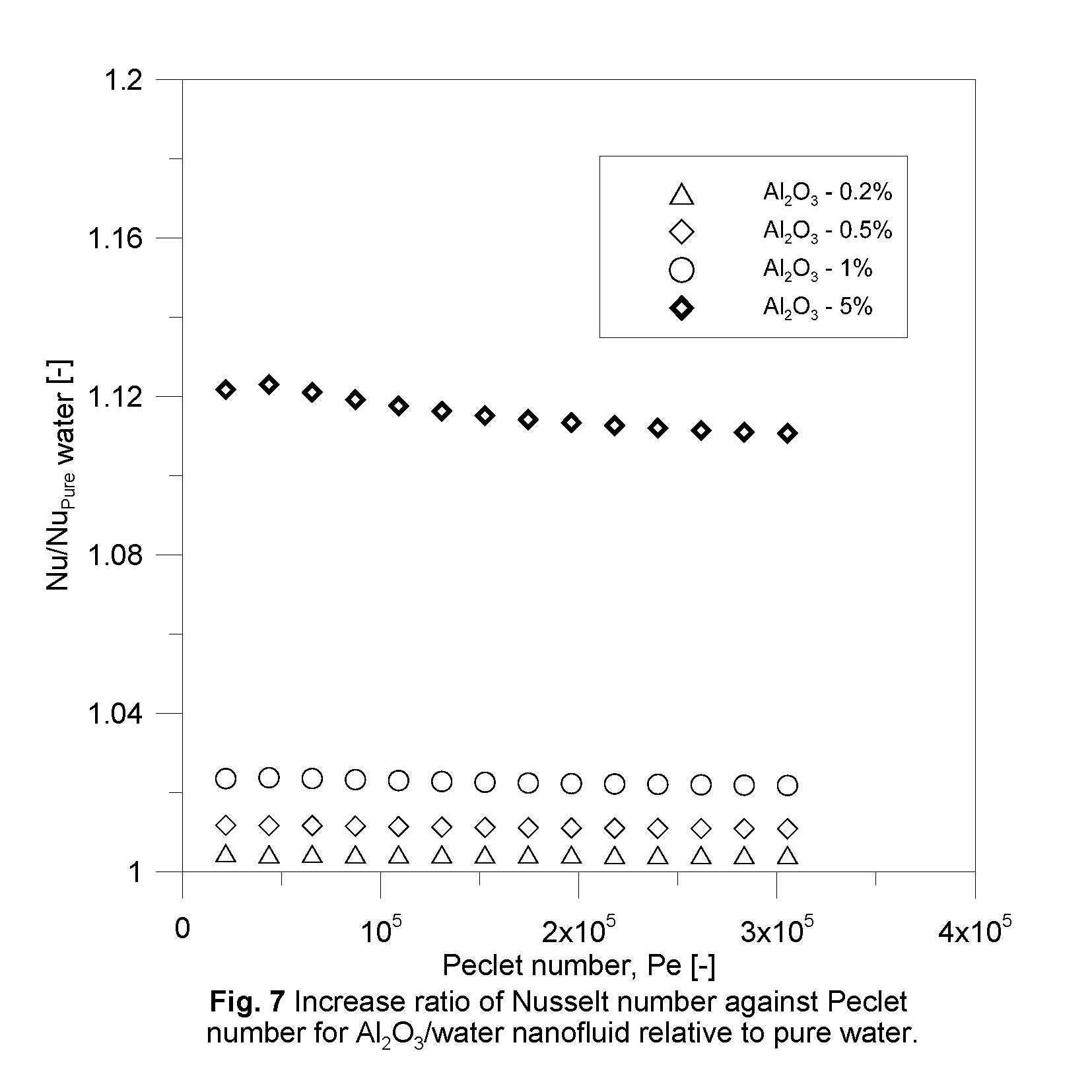
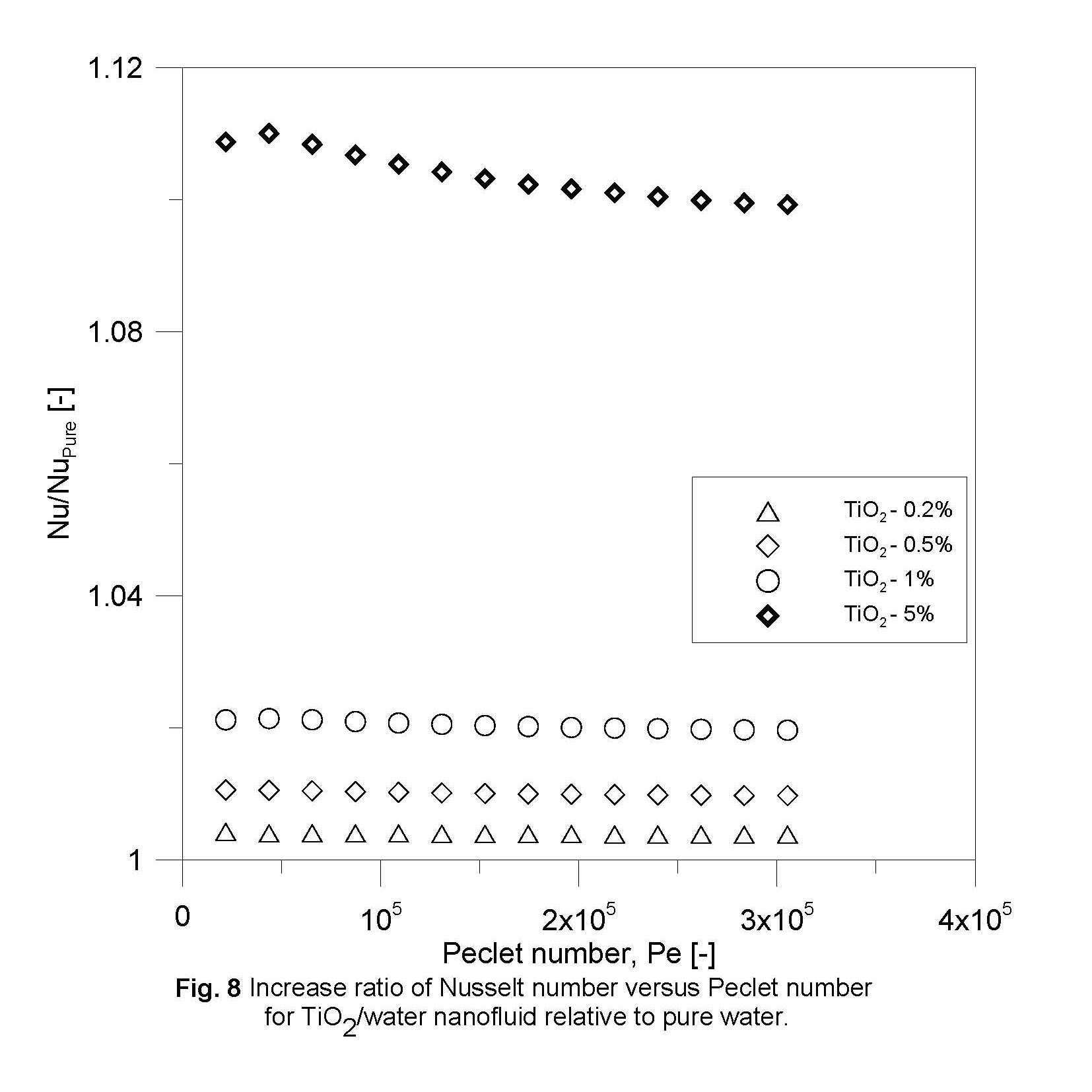
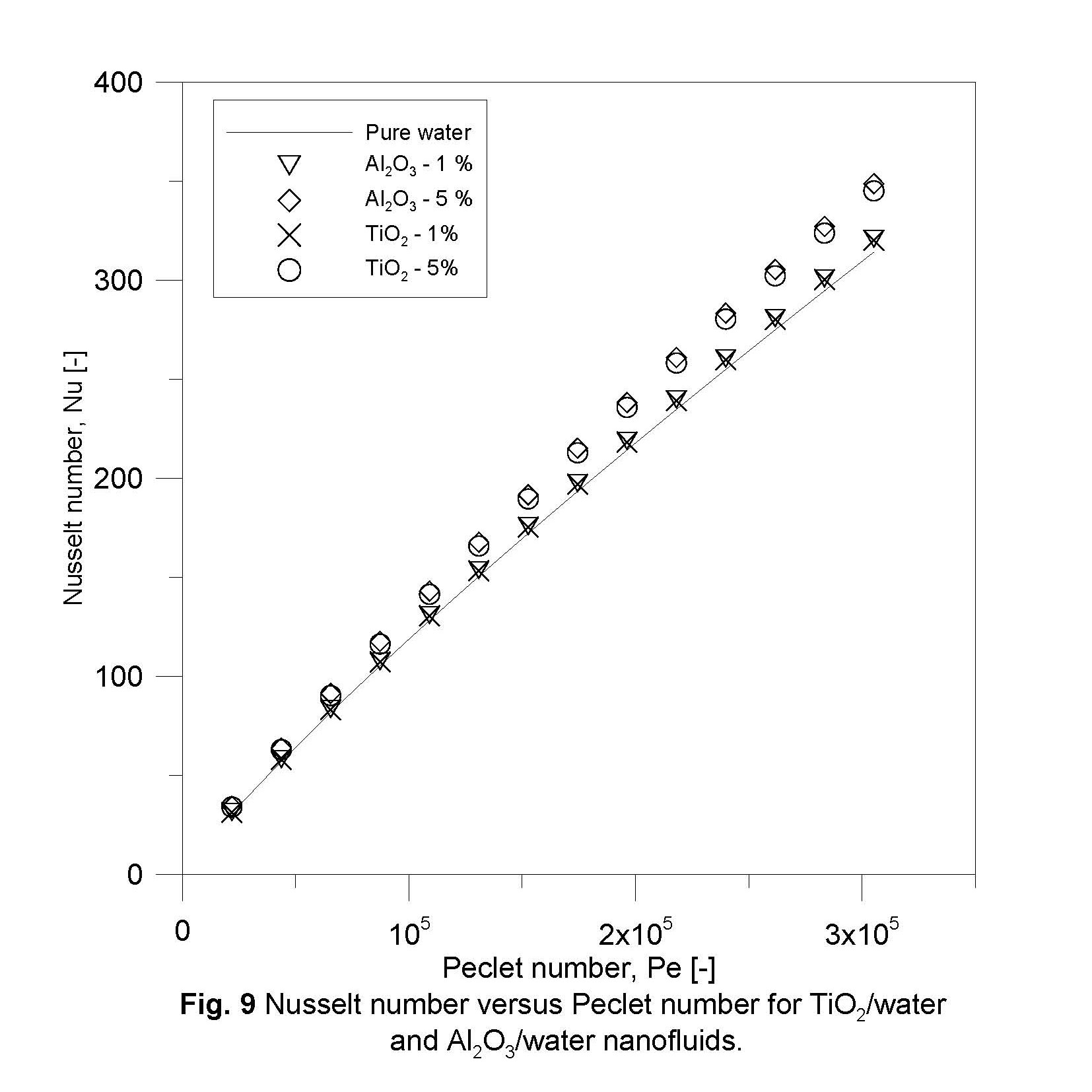
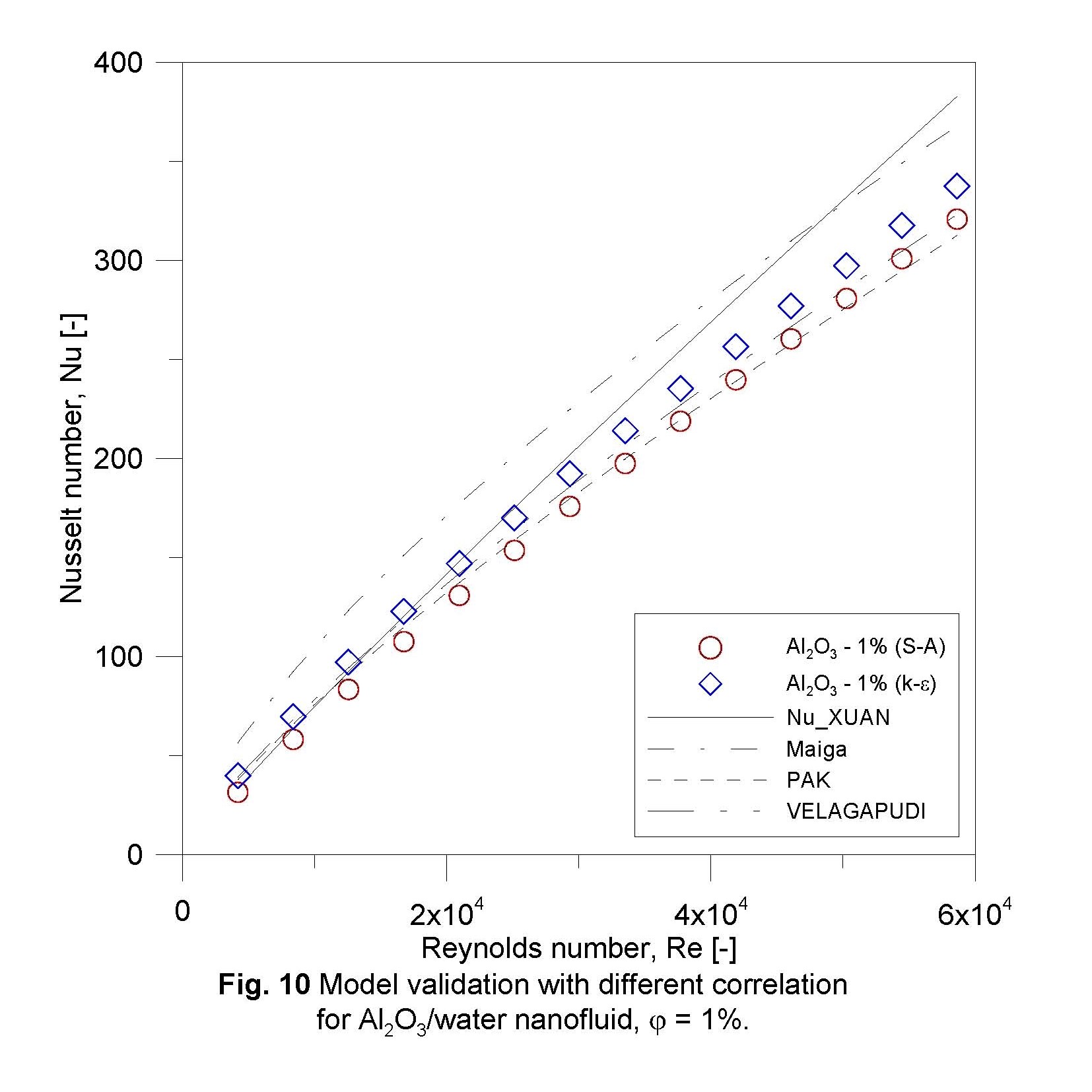
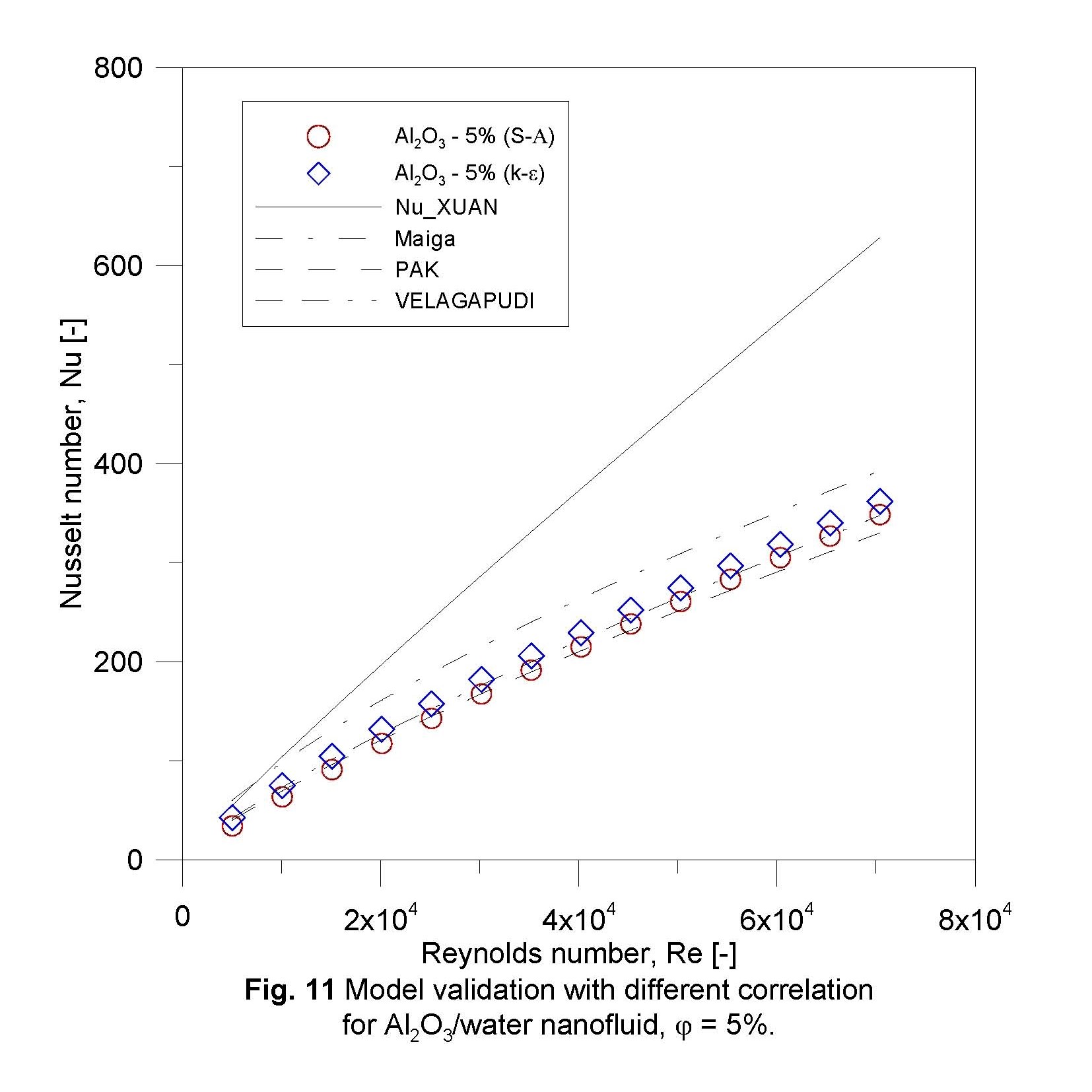
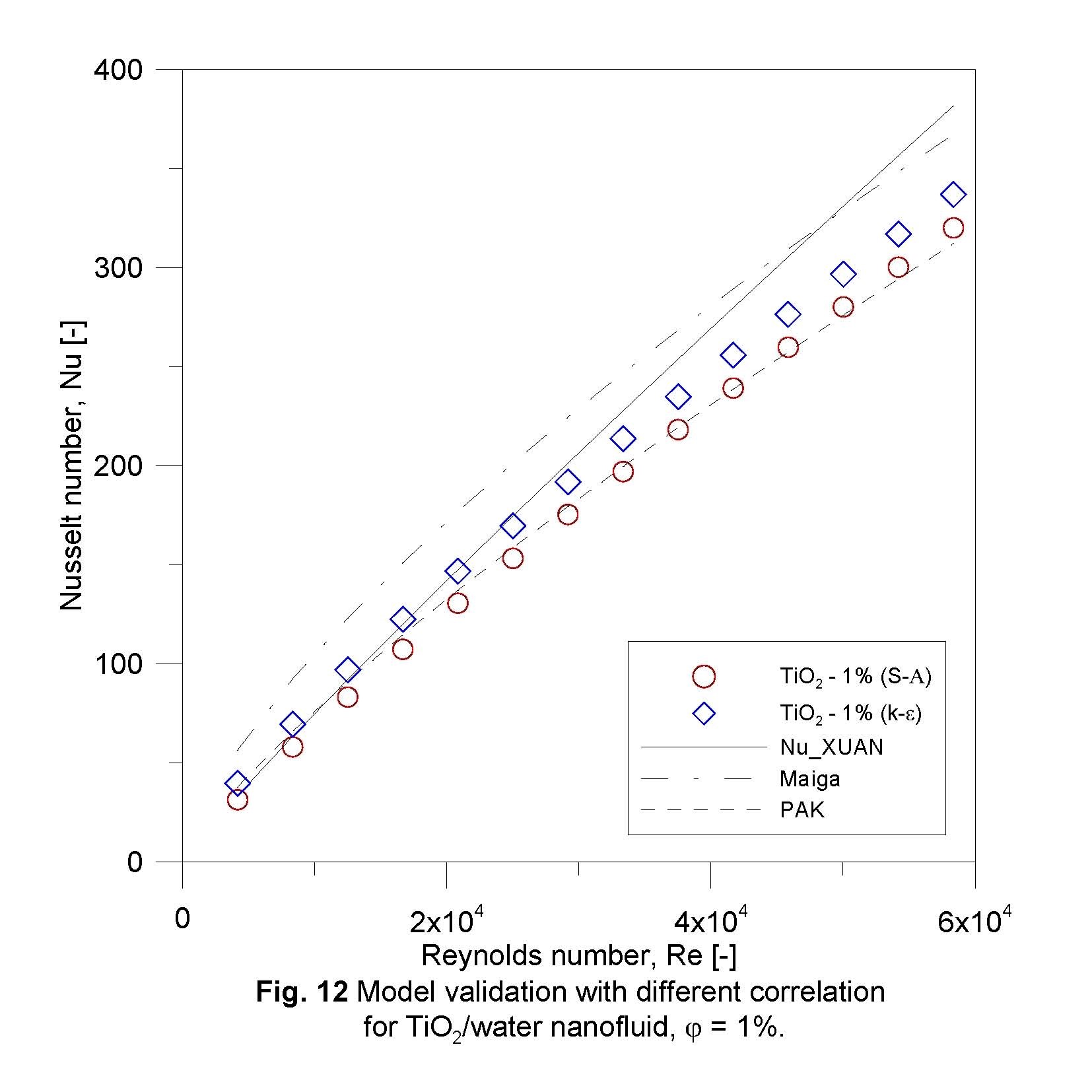
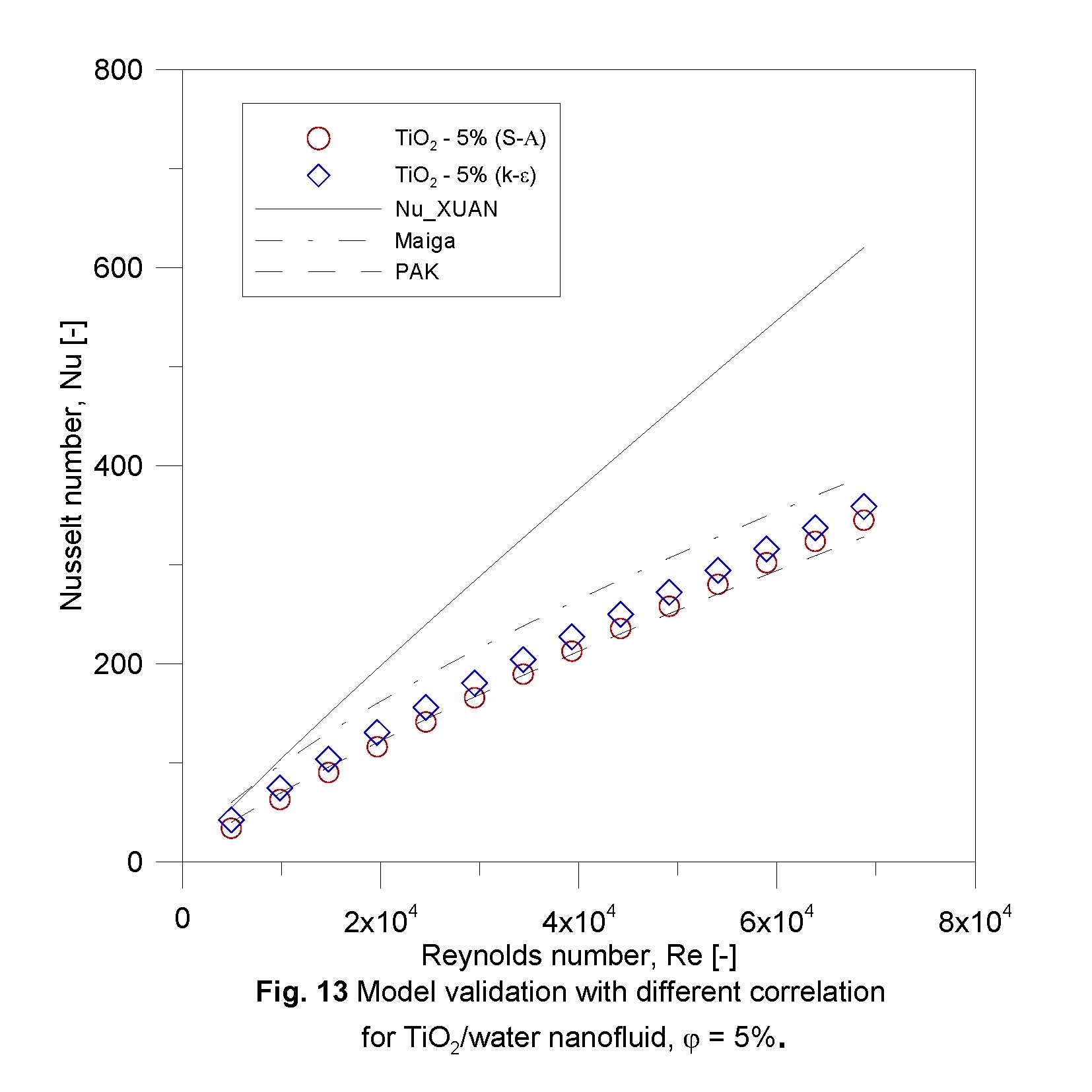
4. Conclusion
Numerical investigation for heat transfer enhancement for flow inside annular tube was done using two turbulence models, k-Ɛ and S-A. A grid was constructed with condition that y+ is always below 1. The following concluded;
- Spalart-Allmaras turbulence model gives better convergence and more stability throughout validation with pure water flow.
- Heat transfer coefficient does enhanced by increasing concentration ratio of nanoparticles for each Al2O3 and TiO2.
Although (Pak et al., 1998) correlation is the eldest correlation, however, it gives best results when dealing nanofluid as single phase fluid.
References
[1] O. Abouali and G. Ahmadi, "Computer simulations of natural convection of single phase nanofluids in simple enclosures: A critical review," Applied Thermal Engineering, vol. 36, pp. 1-13, 2012. View Article
[2] P. Bhattacharya, A. N. Samanta and S. Chakraborty, "Numerical study of conjugate heat transfer in rectangular microchannel heat sink with Al2O3/H2O nanofluid," Heat Mass Transfer, vol. 45, p. 1323-1333, 2009. View Article
[3] V. Bianco, F. Chiacchio, O. Manca and S. Nardini, "Numerical investigation of nanofluids forced convection in circular tubes," Applied Thermal Engineering, vol. 29, p. 3632-3642, 2009. View Article
[4] V. Bianco, O. Manca and S. Nardini, "Numerical investigation on nanofluids turbulent convection heat transfer inside a circular tube," International Journal of Thermal Sciences, vol. 50, pp. 341-349, 2011. View Article
[5] S. Choi, Z. Zhang, W. Yu, F. Lockwood and E. Grulke, "Anomalously thermal conductivity enhancement of in nanotube suspensions," Applied Physics Letters, vol. 79, no. 14, pp. 2252- 2254, 2001. View Article
[6] S. U. S. Choi, "Enhancing thermal conductivity of fluids with nanoparticles, developments and applications of non- Newtonian flows," FED, vol. 231, pp. 99-105, 1995. View Article
[7] M. Cianfrini, M. Corcione and A. Quintino, "Natural convection heat transfer of nanofluids in annular spaces between horizontal concentric cylinders," Applied Thermal Engineering, vol. 31, pp. 4055-4063, 2011. View Article
[8] A. A. R. Darzi, M. Farhadi, K. Sedighi, S. Aallahyari and M. A. Delavar, "Turbulent heat transfer of Al2O3-water nanofluid inside helically corrugated tubes: Numerical study," International Communications in Heat and Mass Transfer, vol. 41, pp. 68-75, 2013. View Article
[9] H. Demir, A. S. Dalkilic, N. A. Kürekci, W. Duangthongsuk and S. Wongwises, "Numerical investigation on the single phase forced convection heat transfer characteristics of TiO2 nanofluids in a double-tube counter flow heat exchanger," International Communications in Heat and Mass Transfer, vol. 38, pp. 218-228, 2011. View Article
[10] W. Duangthongsuk and S. Wongwises, "Comparison of the effects of measured and computed thermophysical properties of nanofluids on heat transfer performance," Experimental Thermal and Fluid Science, vol. 34, no. 6, pp. 616-624, 2010. View Article
[11] A. Gerasimov, Modeling Turbulent Flows with Fluent, Europe: ANSYS lnc., 2006. View Book
[12] S. Z. Heris, M. N. Esfahany and S. G. Etemad, "Experimental investigation of convective heat transfer of Al2O3/water nanofluid in circular tube," International Journal of Heat and Fluid Flow, vol. 28, pp. 203-210, 2007. View Article
[13] F. P. Incropera, D. P. DeWitt, T. L. Bergman and A. S. Lavine, Fundamentals of Heat and Mass Transfer, Hoboken: Wiley, 2007. View Book
[14] P. Kumar, "A CFD Study of Heat Transfer Enhancement in Pipe Flow with Al2O3 Nanofluid," World Academy of Science, vol. 81, pp. 746-750, 2011. View Article
[15] O. Manca, S. Nardini and D. Ricci, "A numerical study of nanofluid forced convection in ribbed channels," Applied Thermal Engineering, vol. 37, pp. 280-292, 2012. View Article
[16] O. Manca, S. Nardini, D. Ricci and S. Tamburrino, "Numerical Investigation on Mixed Convection in Triangular Cross-Section Ducts with Nanofluids," Advances in Mechanical Engineering, 2012. View Article
[17] S. E. B. Maїga, C. T. Nguyen, N. Galanis and G. Roy, "Heat transfer behaviours of nanofluids in a uniformly heated tube," Superlattices and Microstructures, vol. 35, pp. 543-557, 2004. View Article
[18] S. E. B. Maїga, C. T. Nguyen, N. Galanis, G. Roy, T. Maré and M. Coqueux, "Heat transfer enhancement in turbulent tube flow using Al2O3 nanoparticle suspension," International Journal of Numerical Methods for Heat & Fluid Flow, vol. 16, no. 3, pp. 275-292, 2006. View Article
[19] S. E. B. Maїga, S. J. Palm, C. T. Nguyen, G. Roy and N. Galanis, "Heat transfer enhancement by using nanofluids in forced convection flows," International Journal of Heat and Fluid Flow, vol. 26, pp. 530-546, 2005. View Article
[20] C. Murugesan and S. Tamilkolundu, "Mechanism of Forced Convective Heat Transfer in Al2O3/Water Nanofluid under Laminar and Turbulent Flow," in 2nd International Conference on Chemical, Ecology and Environmental Sciences, Singapore, 2012. View Article
[21] P. K. Namburu, D. K. Das, K. M. Tanguturi and R. S. Vajjha, "Numerical study of turbulent flow and heat transfer characteristics of nanofluids considering variable properties," International Journal of Thermal Sciences, vol. 48, pp. 290-302, 2009. View Article
[22] M. Nasiri, S. G. Etemad and R. Bagheri, "Experimental heat transfer of nanofluid through an annular duct," International Communications in Heat and Mass Transfer, vol. 38, pp. 958-963, 2011. View Article
[23] C. T. Nguyen, G. Roy, C. Gauthier and N. Galanis, "Heat transfer enhancement using Al2O3-water nanofluid for an electronic liquid cooling system," Applied Thermal Engineering, vol. 27, no. 8-9, pp. 1501-1506, 2007. View Article
[24] D. A. Nield and A. V. Kuznetsov, "Forced convection in a parallel-plate channel occupied by a nanofluid or a porous medium saturated by a nanofluid," International Journal of Heat and Mass Transfer, vol. 70, pp. 430-433, 2014. View Article
[25] B. C. Pak and Y. I. Cho, "Hydrodynamic and Heat Transfer Study of Dispersed Fluids with Submicron Metallic Oxide Particles," Experimental Heat Transfer, vol. 11, pp. 151-170, 1998. View Article
[26] G. Pathipakka and P. Sivashanmugam, "Heat transfer behaviour of nanofluids in a uniformly heated circular tube fitted with helical inserts in laminar flow," Superlattices and Microstructures, vol. 47, pp. 349-360, 2010. View Article
[27] L. Qiang and X. Yimin, "Convective heat transfer and flow characteristics of Cu-water nanofluid," Science in China, vol. 45, no. 4, pp. 408-416, 2002. View Article
[28] W. Rashmi, A. F. Ismail, M. Khalid and Y. Faridah, "CFD studies on natural convection heat transfer of Al2O3-water nanofluids," Heat Mass Transfer, vol. 47, pp. 1301-1310, 2011. View Article
[29] M. Rostamani, S. F. Hosseinizadeh, M. Gorji and J. M. Khodadadi, "Numerical study of turbulent forced convection flow of nanofluids in a long horizontal duct considering variable properties," International Communications in Heat and Mass Transfer, vol. 37, pp. 1426-1431, 2010. View Article
[30] G. Roy, C. T. Nguyen and P.-R. Lajoie, "Numerical investigation of laminar flow and heat transfer in a radial flow cooling system with the use of nanofluids," Superlattices and Microstructures, vol. 35, pp. 497-511, 2004. View Article
[31] S. M. Salim and S. C. Cheah, "Wall y+ Strategy for Dealing with Wall-bounded Turbulent Flows," in Proceedings of the International MultiConference of Engineers and Computer Scientists, Hong Kong, 2009. View Article
[32] A. M. Sharifi, A. Emamzadeh, A. A. Hamidi, H. Farzaneh and M. Rastgarpour, "Computer-Aided Simulation of Heat Transfer in Nanofluids," in Proceedings of the International MultiConference of Engineers and Computer scientists, Hong Kong, 2012. View Article
[33] R. S. Vajjha, D. K. Das and P. K. Namburu, "Numerical study of fluid dynamic and heat transfer performance of Al2O3 and CuO nanofluids in the flat tubes of a radiator," International Journal of Heat and Fluid Flow, vol. 31, pp. 613-621, 2010. View Article
[34] V. Velagapudi, R. K. Konijeti and C. S. K. Aduru, "Empirical Correlations to Predict Thermophysical and Heat Transfer Characteristics if Nanofluids," Thermal Science, vol. 12, no. 2, pp. 27-37, 2008. View Article
[35] Y. Xuan and Q. Li, "Heat transfer enhancement of nanofluids," Int. J. Heat Fluid Flow, vol. 21, pp. 58-64, 2000. View Article
[36] Y. Xuan and Q. Li, "Investigation on convective heat transfer and flow features of nanofluids," ASME Journal of Heat Transfer, vol. 125, no. 1, pp. 151-155, 2003. View Article
[37] Y. Yang, Z. G. Zhang, E. A. Grulke, W. B. Anderson and G. Wu, "Heat Transfer Properties of Nanoparticle-in-Fluid Dispersions (Nanofluids) in Laminar Flow," Int. J. Heat Mass Transfer, vol. 48, no. 6, pp. 1107-1116, 2005. View Article